Airfix 1/24 P-51D "Dallas Doll" Part 1
By Rodney Williams
"Dallas Doll"
A P-51D Mustang in 1/24th scale Part 1
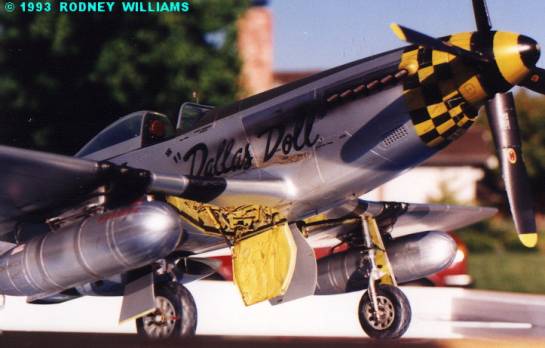
Just over a decade ago, I received two contracts to build a 1/24 scale P-51D, and the P-51B Mustangs. I used the "Airfix" kit, as it's the only game in town. My research material was next to nothing, and I do not recall exactly what I had.
I think my client Frank sent me the enclosed photo of "Dallas Doll," along with the art drawing. Frank wanted the name on both sides of the model!
You will note in the black and white photo of "Doll," that the first lower fuselage white invasion stripe has been removed. However, Frank wanted it on the model.
Several enclosed photos are marked for P-51D, and P-51B parts.
I started on the wheel wells, and what a rat race that turned out to be! I never seen so much stuff up inside a wheel well. Since it's been so long, I have no idea what thickness some of my material was made from. I made things out of styrene, brass, copper, and aluminum.
Since I was building two of them, I made a "master" for the main landing gear, and had some jeweler make a mold and cast my parts in what they call the "Lost Wax" process. The mold cost me $150.00, and each cast was $25.00.
I have no idea how long it took to build these wheel wells for both of these models as I did not write down my hours. However, when I build another P-51D in 1/32 scale, I kept a work log. It took over 400 hours.
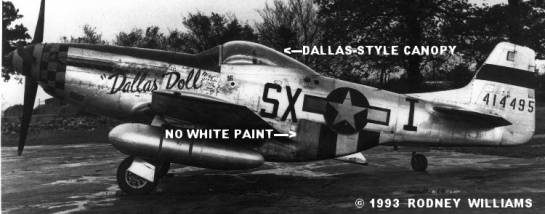
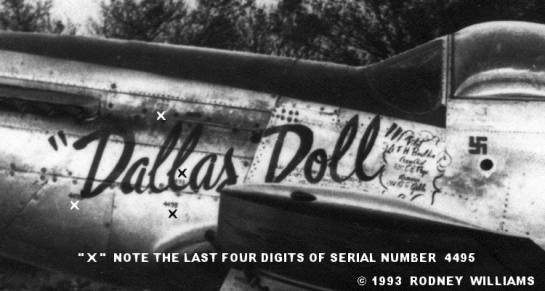
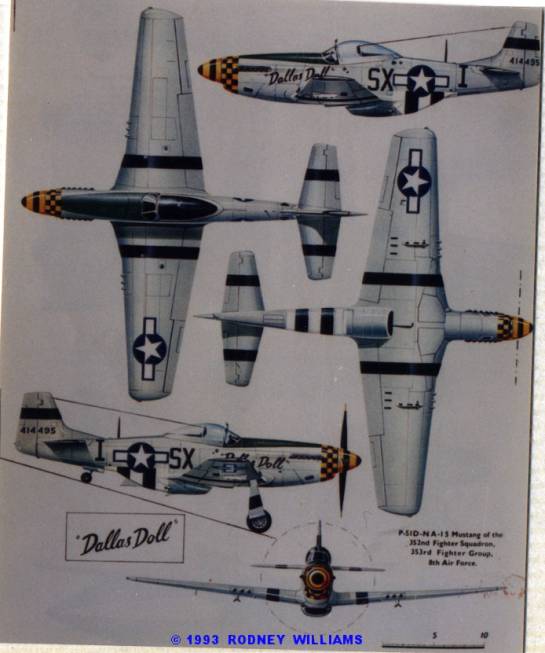
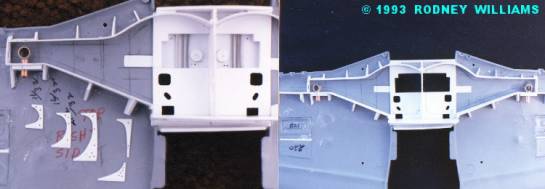
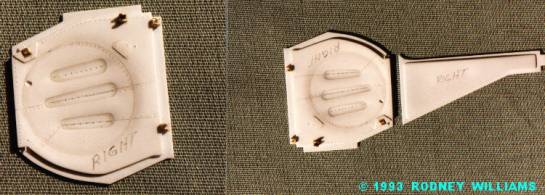
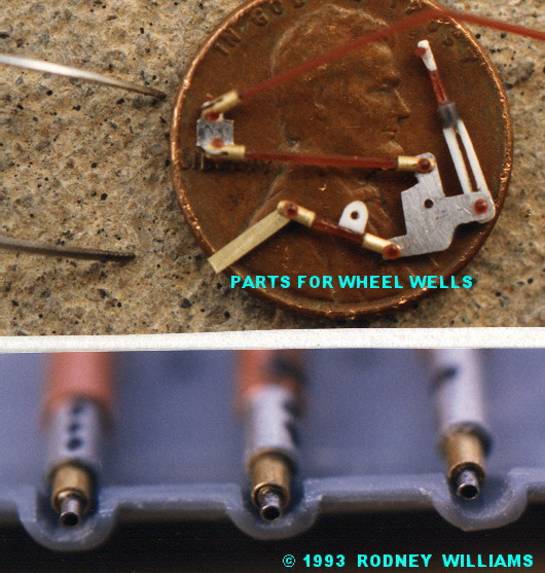
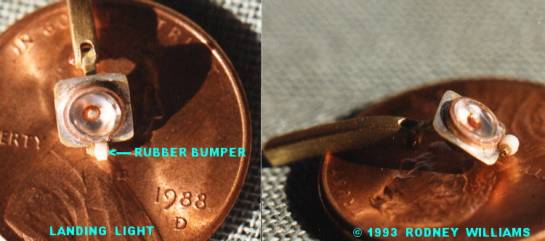
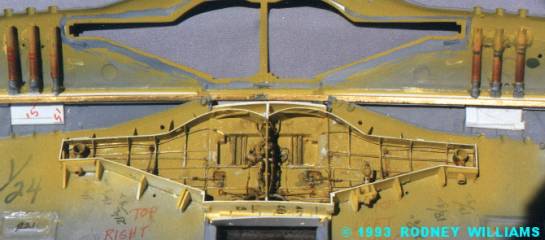
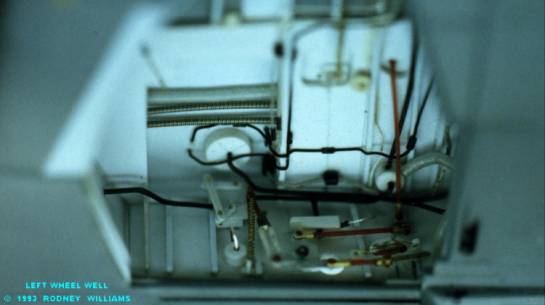
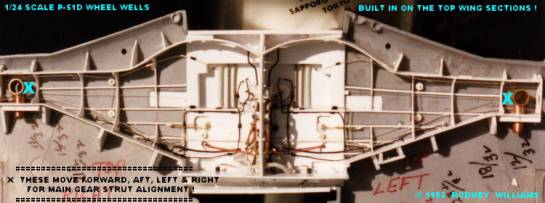
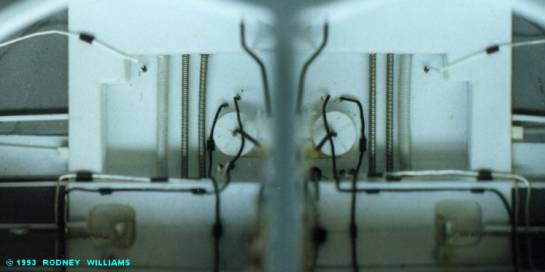
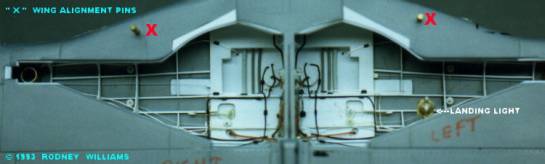
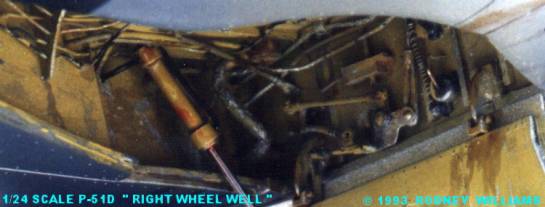
Many of my parts are made "moveable" on a "pin hinge" system. This way, when they are installed during the building process and/or on final assembly, they can be adjusted for correct alignment, or as close as possible. Note the photo of the bottom fuselage "vent" door for the water cooler. I made it so the door would open and close, using telescoping tubing. It was installed after the fuselage was glued together on a tiny brass rod. Look close and you will see the brass rod. I think the rod was about .015" in diameter.
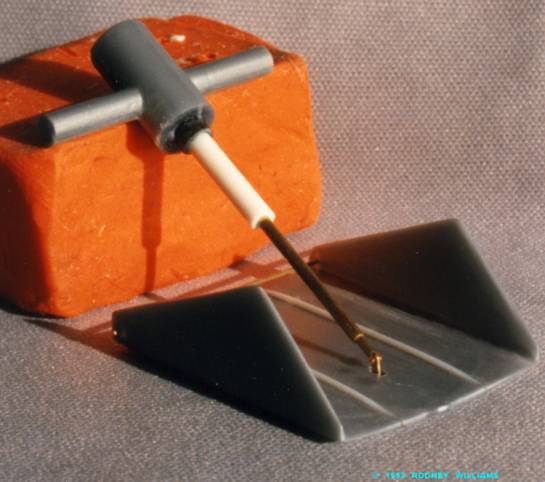
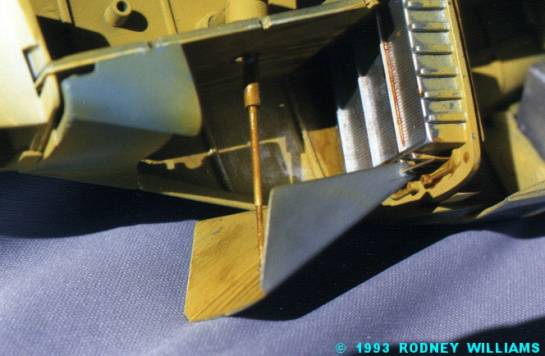
The enclosed cockpit photos show what kit parts I used, and what I scratch built in.
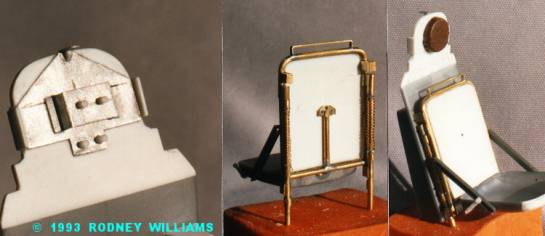
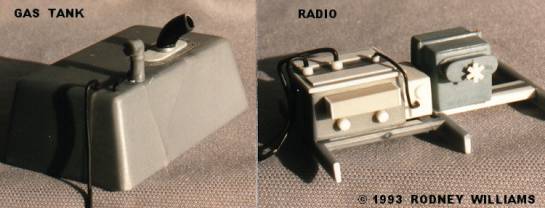
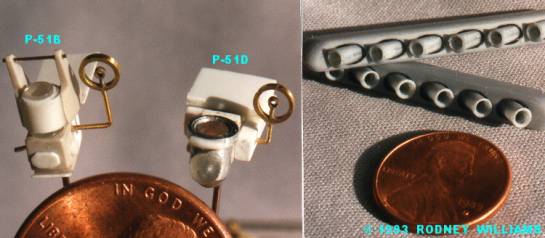
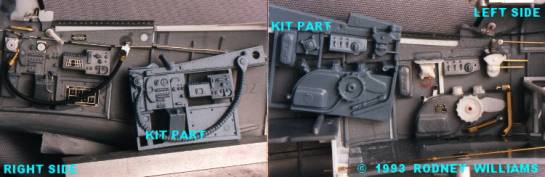
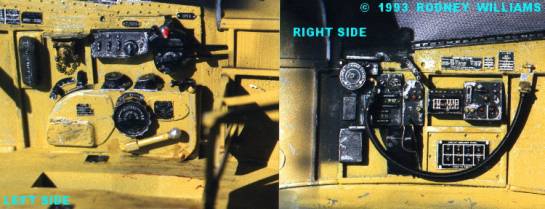
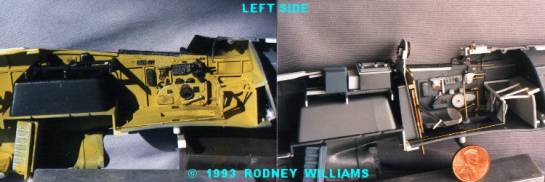
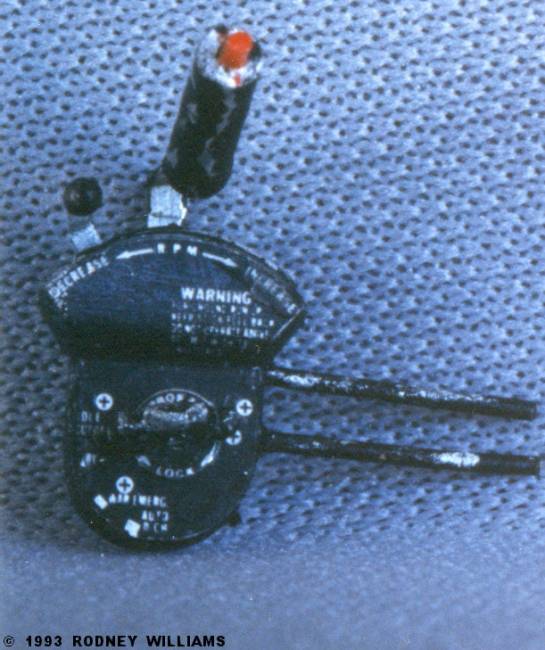
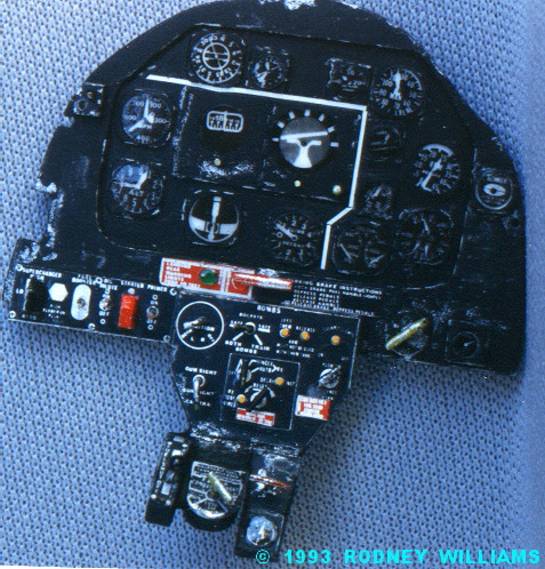
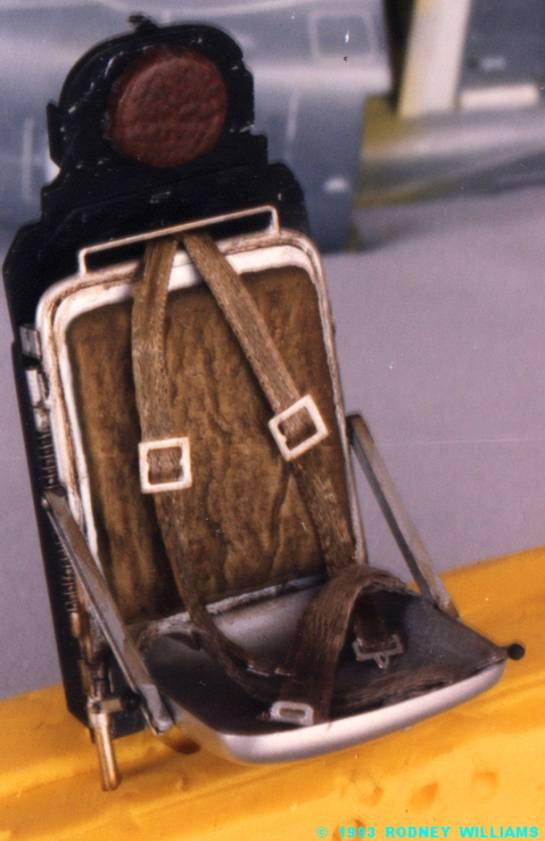
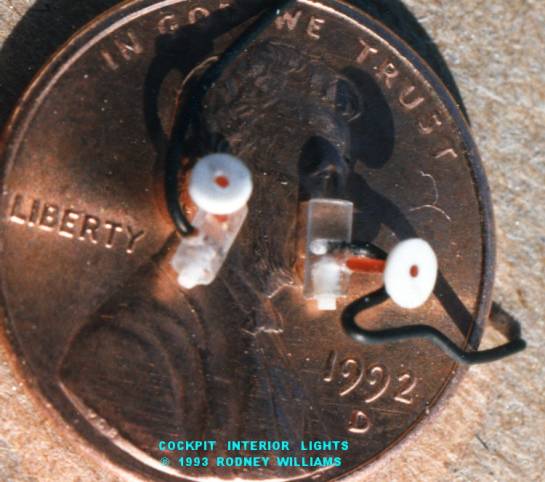
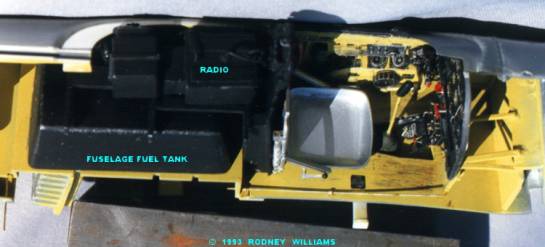
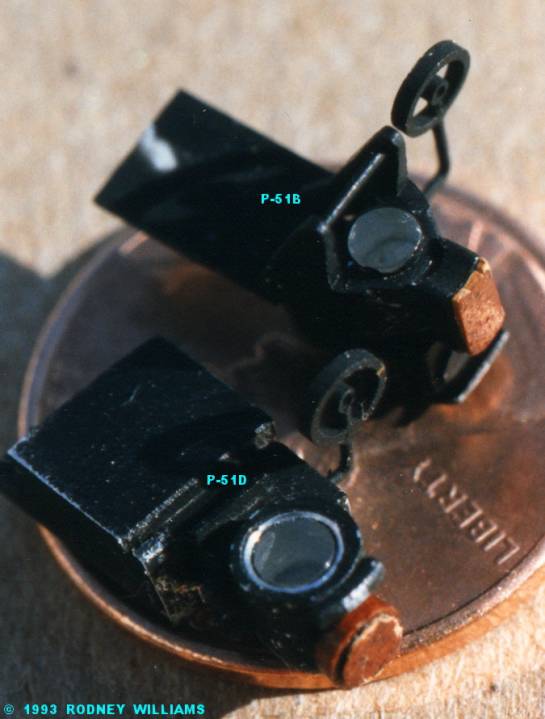
My client contacted me and wanted me to build the "Dallas Style" canopy. This aircraft was made in Dallas, Texas. For some reason, all the canopies were made different. You can see the raised part of the canopy, just aft of where it meets the windscreen. I used a kit canopy, then made a "plaster of paris" mold. I added more plaster to the top of the mold, then sanded it smooth. I place the regular canopy on the mold and it did not fit. I was satisfied with my results. I vacuformed a canopy using .030" clear vacuforming plastic. It looked like the canopy on my black and white photo. After sanding a few of them down from 320 grit to 2000 grit, including scribing the panel lines and adding all the rivets, I found two canopies that were just not up to my liking! It was back to square one (start over until you get a perfect one).
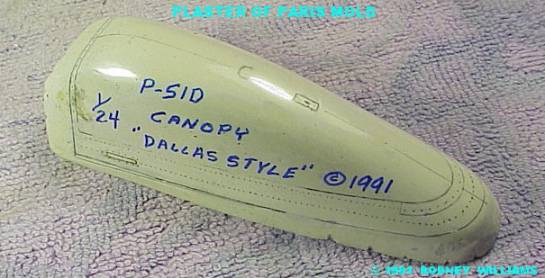
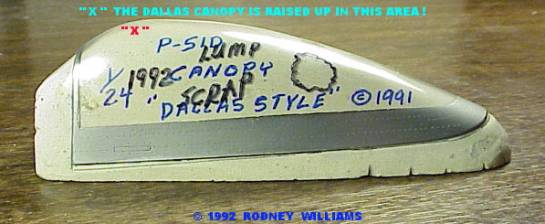
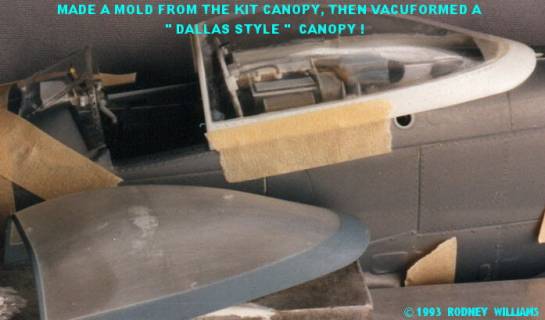
I wound up removing the entire instrument dash cover, and then scrath-built a new one. I had to be careful, as everything was in the cockpit, except the seat, and it was finished. What fun that was! The easy part was painting the underside of the dash cover, without getting over spray all over in the cockpit. I accomplished it, but I don't remember how I did it, so I can not tell you how it was done. Too many years have gone by.
I made a new mold for a one piece windscreen, including a portion of the front top of the fuselage. Note the holes in the front section of the mold. These holes are drilled through the mold. When you vacuform, these holes provide suction from your vacuum sweeper, and it sucks the plastic down very tight against the mold. The end result gives you a "perfect" new part, that fits, and looks "RIGHT!"
The last photo shows the windscreen on the model. Like the canopy, it was sanded using 320 grit to 2000 grit wet/dry sandpaper. I usually add the rivets, and panel lines when I'm finished sanding with 600 grit. In this case, I added the open/close handle, etc. I use a pointed pin, in a pin vise to place the rivets in there location. Caution:::: "if you use too much pressure," you can craze the plastic, especially if you use the kit injected mold windscreen/canopy. I polished the plastic with Blue Magic metal polishing cream, then I dip it several time's into Future Floor Wax. I always paint the insides of my canopies and windscreens, after the Future has dried for a week or more. (Yes! I even do it to my 1/72 scale models !!!).
I use Future Floor Wax; (f.f.w.) to glue on my windscreens. After a few days of drying time, I fill in the seams with super glue. This method prevents "fogging" on the inside of the windscreen. On some models, when I have a 99.9% perfect fit, I have glued on my windscreen with only f.f.w. Once the wax is dry, it's almost impossible to remove the part. In fact I use the f.f.w. on many parts on final assembly. TRY IT!
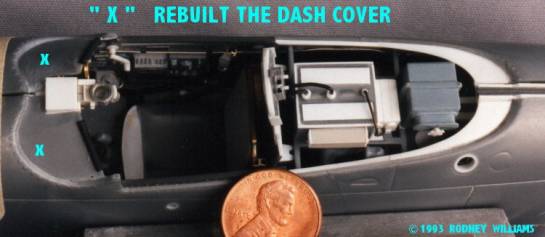
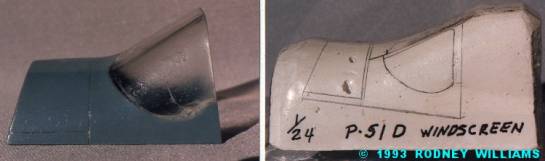
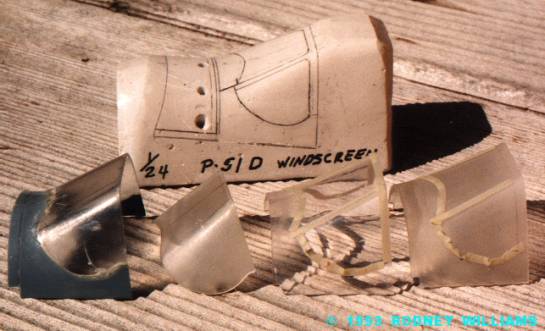
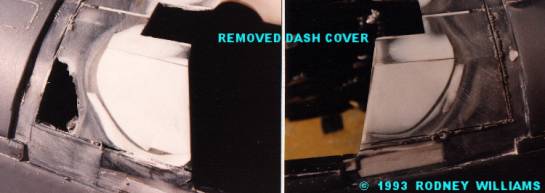
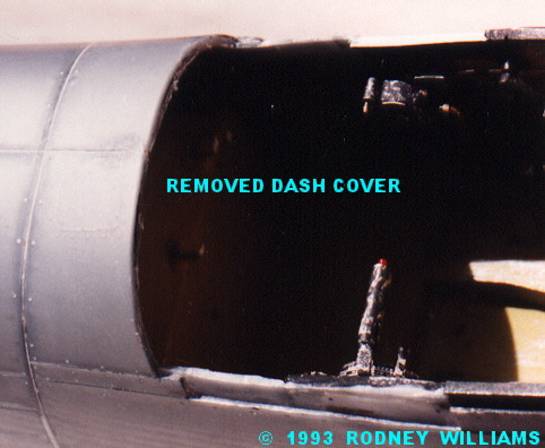
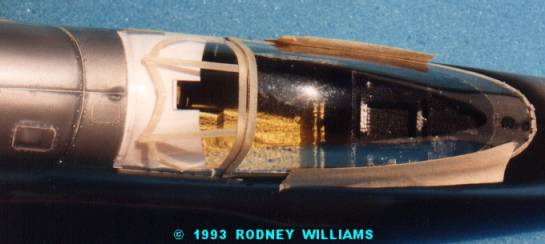
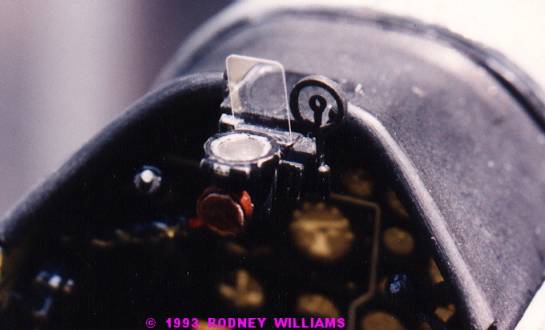
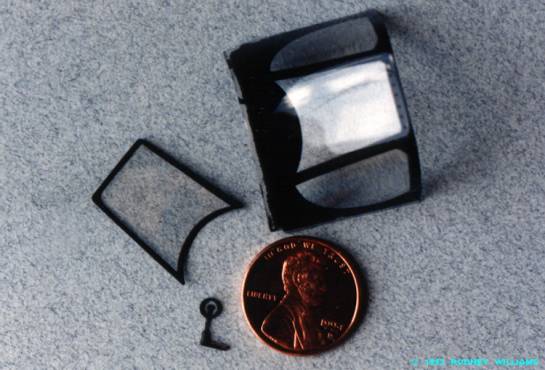
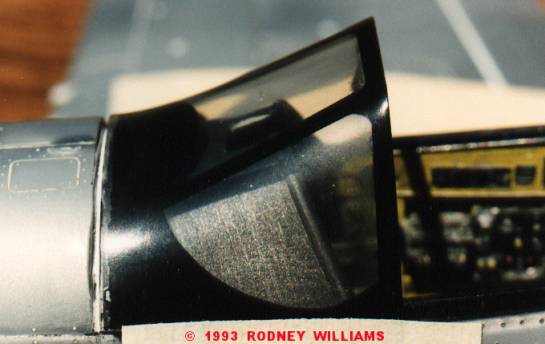
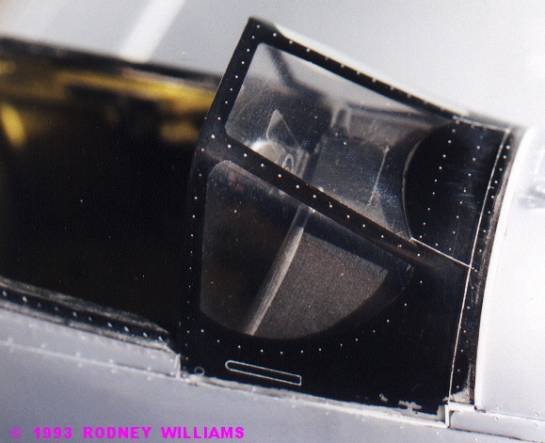
As I progressed on this model, I also built many items for the P-51B conversion, using the same Airfix P-51D kit.
Frank wanted the big paper drop tanks on his model. I read that they were 108 gallons, then another statement said they were 110 gallons. I can't recall how I came across the dimensions for the paper tank. I got some aluminum tubing and added the styrene stock on both ends with super glue. Once finished, I added the panel lines, gas cap, etc. I had either Roy Sutherland of "Cooper Details" cast the tanks, and/or Bill Ferrante.
Study the photo of the two drop tanks! The wing pylon on the "B" model differs from the pylon on the "D" model.
The tanks were painted with "SnJ" SPRAY METAL ALUMINUM," then weathered with artist oils. I made my own decals by typing up the words on my IBM electric typewriter. I printed them on clear decal film, using my old 1987 Panasonic copy machine, as it could print in red and black.
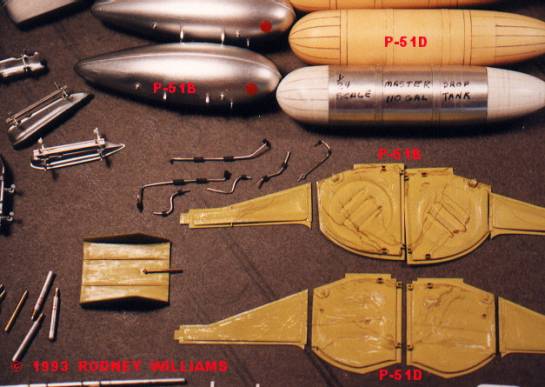
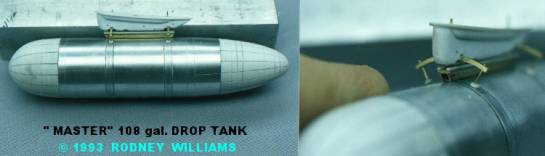
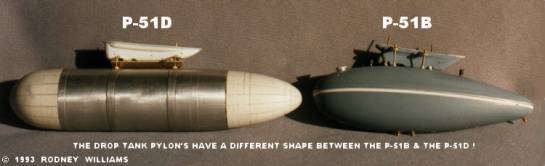
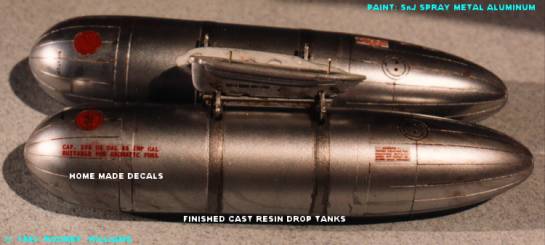
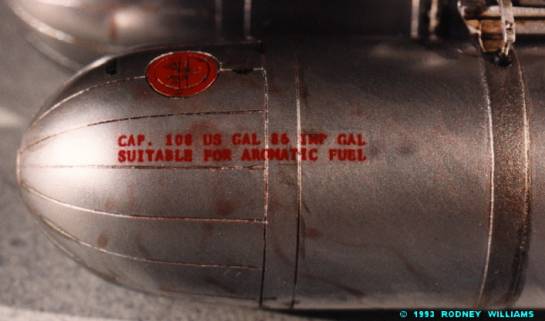
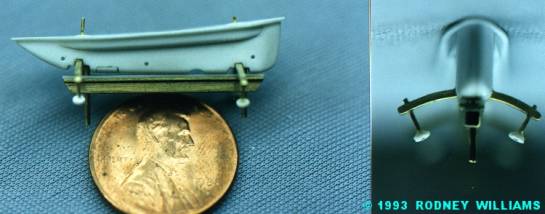
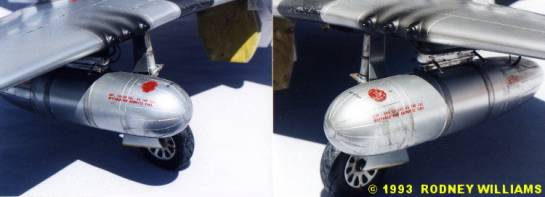
© Rodney Williams
This article was published on Wednesday, July 20 2011; Last modified on Saturday, May 14 2016