Williams Brothers 1/32 P-35 Part 1
By Mike McLeod
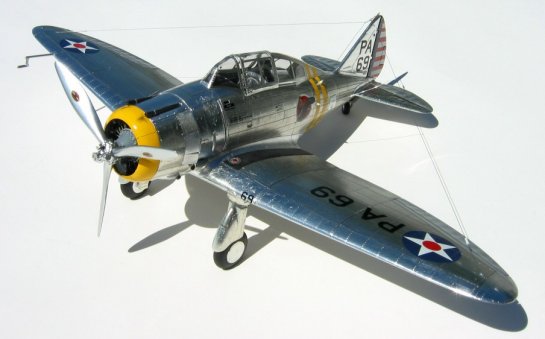
- Kit: Williams Brothers kit #32-135 1/32nd scale Seversky P-35/S2
- Price: $15.00 from vendor at contest
- Decals: Scale Master # 32-135 Seversky P-35/S2. Sheet is printed in red, yellow, light blue, dark blue, black, white, and gold. Nice quality, the clear portions were not yellowed and remained very clear (that is invisible) once applied. The print register was very good, almost no error.
This kit was built to replicate the P-35 flown by the Commanding Officer of the 27th Pursuit Squadron, 1st Pursuit Group, Selfridge Field, MI circa 1938.
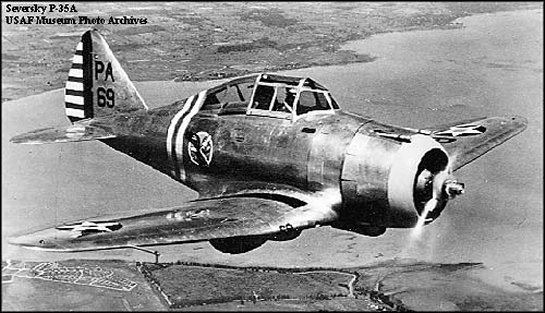
History
In the early '30s a pair of Russian immigrants, Alexander deSeversky and Alexander Kartvelli teamed up in the aviation business of building Pursuit planes in hopes of landing a lucrative US Army Air Corp contract. Their early designs evolved into the P-35 and later the famous P-47, whose basic outline is evident in the P-35. While aircraft designers struggled with weight and power constraints, the Seversky design emerged as the first all-metal high performance pursuit plane with the newly developed Pratt & Whitney R-1830 delivering almost 1,000 hp. The innovations incorporated in the P-35 included all metal semi-monocoque construction, fuel in a "wet" wing, good streamlining (except for the heinous main gear fairings!), and a superb wing airfoil and layout. On its debut, the P-35 was one of the fastest aircraft in the world (281 mph) and the modified version called the S2 Racer set may speed records (300 mph) and was faster than any USAAC planes in service. Although it had range and speed advantages over its rivals, it lacked in handling qualities until the flat wing was given some dihedral on the outer wing panels.
Production P-35s (the first aircraft delivered to the USAAC in natural metal finish) were in service beginning in 1937 at Wright Field, Ohio. Operational units included the 27th, 17th, and 94th Pursuit Squadrons which primarily operated from Selfridge Field, Michigan. Units of P-35s eventually deployed to the Pacific Theater and were involved in early air battles with the advancing Japanese Air Forces. Before emerging hostilities caused all US aircraft export contracts to be nullified, some P-35's found their way into service in Sweden as EP-106s. Oddly enough, and well concealed for obvious reasons, some 20 P-35s were sold to Japan and designated A8V-1, however they were taken from combat duty prior to Pearl Harbor.
While the P-35 GUARDSMAN never quite made it into the main spotlight of the times or found a spot as a famous aircraft, it was in fact an important evolutionary step in the development of US air power. The technology of the P-35 continued to evolve into the P-41, P-43 LANCER, and ultimately the P-47 THUNDERBOLT. As a testament to the design expertise of Seversky, his S-3 airfoil/wing design remained basically unchanged from 1930 through the last service roles of the P-47Ns in the 1950s. His designs were capable of flying efficiently, at high sub-mach speeds, and rugged enough to take the highest levels of punishment and continue to fly. The P-35 was the first of this new breed of modern fighter plane and led the way for future advancements in fighter-bomber development.
What's Inside the Box
Upon opening the box you will find several trees of medium gray styrene with a standard parts layout. The parts for both kit options are mixed in among the trees and numbered accordingly. The clear canopy/windscreen parts are in a separate bag and have both Pursuit and Racing versions. The decals were missing from my box and a call to Williams Brothers was answered by a friendly person who promptly shipped a new set gratis…thank you! Two black rubber tires are also included for the option if you care to risk the potential cracking and decomposition of the tires in the future. The instruction sheets consist of an 8.5x11 exploded view with all parts numbered and a 17.5x11 sheet with instructions on one side and 3-views on the reverse. The 3-views are very nice and appear to match closely the airframe outlines of photo documentation I have. The decal placement is annotated on the 3-views.
Overall Assessment
While this is obviously not a high-end kit, it has all the necessary elements to allow an experienced modeler to "take it to the limit". While there are many minor mold inaccuracies, most can be fixed or worked around. Other significant issues with the kit include:
- Plastic - not "homogeneous" in that when scribing the tool will draw a nice, fine line and suddenly "dig in". In random areas the plastic is not the normal softer styrene but a harder, more brittle styrene. In these areas the scribing tool or scribing pin tends to make a ragged line or chip the plastic. Much care must be used when scribing/repairing these small, random areas.
- No alignment pins. Mating of major assembly halves takes great care. Scribes lines cannot go all the way to the edges. After assembly, the panel lines can be mated and run across the seam.
- Most of the raised panel lines were not in the correct locations and had to be replaced with recessed lines to allow correct orientation of the rivet lines.
- The horizontal stab fairings are not level and lined up side-to-side. This caused some great difficulty when attempting to layout matching, symmetrical panel lines prior to joining the fuselage halves. Fortunately, the stabs can be attached even and level despite the crooked fairings.
- Poor definition at each control surface hinge line. The weak line was not even suitable for a wash to bring up definition. Each hinge line had to be scribed out and deepened to provide adequate 3-D look. Also, tail surfaces needed to be drilled through at each hinge.
- The cowl flaps were cheesy at best. A simple raised outline of each set of flaps was not adequate. As the entire cowl was removed anyway, a set of thin styrene cowl flaps was installed with underlying linkages to provide a better look, that of a functional machine.
- No cockpit detail at all to speak of, even though the box cover says "Detailed Interior". The only parts I was able to use were the forward bulkhead, seat, and machine gun bodies. All other parts were scratched in. The seat was given a major rework and detailed up including photo-etch buckles and self-adhesive strap material. Decals were provided for the instrument/engine panel however, after market gauges and a precision punch set were employed to fabricate a much better looking set with color and dimension.
- Large gaps in wing joint where outer panels meet center section. Since this model has a flat wing/dihedral wing option, the gap will appear on the top or bottom, depending on which wing you build. The gap was too large for putty and had to be filled in with styrene strips to allow for subsequent panel line scribing and riveting.
- The landing gear mounting holes on the wing are too far aft and had to be re-drilled about 3 mm farther forward. This was seen coming during initial parts fit and the wing was built with a core of baked modeling clay epoxied inside to allow a sufficient structure to bond into. This also allowed the addition of the small ram-air inlet on the inner right leading edge.
- The main landing gear looked okay, but seemed too flimsy to last. New legs were fashioned from steel music wire, brass tube, and JB Weld steel epoxy. These are very strong and durable.
- The tailwheel assembly had insufficient detail and a "plate mount". A new strut was fashioned from styrene stock and brass tube and mounted on a correctly positioned pivot point. The wheel and tire were cut away from the assembly and used as a more believable tire on a music wire/JB Weld axle.
Construction Part 1
After studying all my documentation and staring at the parts in the box for a while it became time to hack on some styrene. The main thrust of this project was to build a reasonable "Natural Metal Finish" airplane, and a classic 30's vintage Pursuit plane was an obvious good subject. As construction began, I had some ideas of how I wanted the model to look in my mind, but not any specific idea on how to approach certain construction issues and methods; I would have to "wing-it". Consequently, much time was used in the project as I broke away from actual kit work to experiment with a new technique, learn about different materials, explore options, test new methods and materials, etc. This "off time" also allowed me to take a bit of a break from the core project and return to it fresh and ready for full effort on detail and exacting replication. To paraphrase "the Master" Dave Platt's Laws of Scale Modeling: "It is not about documenting what you did build, but rather about replication of what your documentation presents". With that approach, a few breaks were well received. Additionally, the somewhat scarce source data on the Seversky P-35 series of aircraft led to some times when details were derived from documented Seversky design and construction methods on other similar models/variants. With a suitable amount of data and photographs I was off to the shop for some late nights and the P-35 project was under way. In the end certain assumptions and tradeoffs were made. And not to forget another of "the Master's" laws: "We never finish a SCALE model, we just stop working on it…".
ENGINE
The engine detail in this kit is very good. Crankcase is composed of three pieces with individual cylinders directly attached. Cylinders have nice cooling fin detail although comparison of cylinders side-by-side shows lots of variation in the shape and size of the heads and lifter/rocker arm covers. While each cylinder has an attach point for an intake and exhaust I elected to omit these details due to crowding and inability to see the finished detail easily. The front row cylinders have free standing lifter tubes running from the case to the rocker arm covers, a nice change from the cheap looking ones molded into the side of the cooling fins. For added detail I installed the oil cross feed tubes and drain lines (copper wire) between cylinders and on gearbox drain. The plug wires were tricky since a thin styrene plug wire conduit was molded into the reduction gear case. By drilling small pairs of holes at the correct locations, I was able to feed through short half-loops of 32-ga wire from inside the case and tack glue from behind the conduit ring with CA. This left the neat pairs of wires to be run up to the respective plugs on front and rear cylinder banks. Case was painted gloss machine gray, cylinders aluminum and lightly washed with magnesium. Other details on the engine were painted silver or gloss black per photos and plug wires brushed with a brassy-tan color to emulate the braided insulator covers. The engine was drilled through to accept a brass tube which acts as a bushing for the thick music wire prop shaft / light switch, but the brass was not glued until final assembly when prop shaft fit and alignment were set up.
COCKPIT
Cockpit work began with much planning. The only salvageable parts were the forward firewall and the seat, both of which needed extensive work. Using photo documentation...
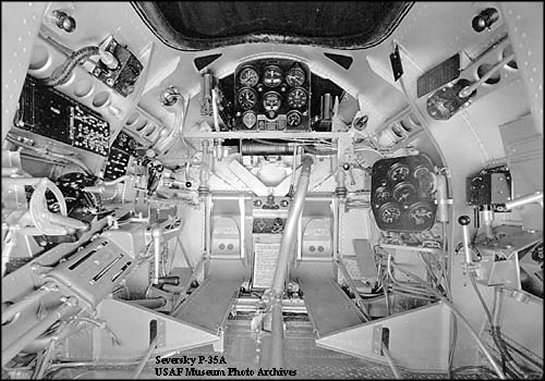
...the side walls were marked, scribed, riveted, and a "hole-punched" beam added
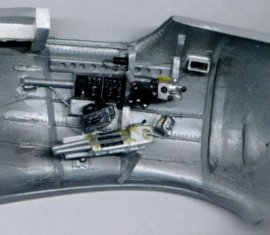
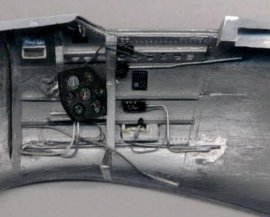
The canopy rails on the external fuselage were non-existent so some surgery was required to hack out a groove and install a styrene I-beam to run from the windscreen to the aft turtledeck. A rear cockpit bulkhead was fashioned and riveted.
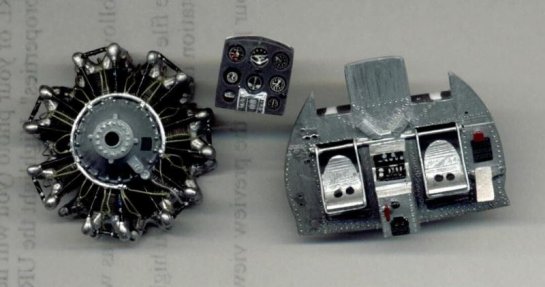
Using precision punches and instrument decals, custom main instrument and engine panels were made. The seat was reworked to include all steel mounting tubes, seat locks, and belts/buckles inertial reel. Side wall details were manufactured (in some cased a few times before being acceptable!) and set aside for installation. These included: throttle quad, oil/cowl control lever box, electrical panel, trim wheel box, gear/flap transmission, .50 cal shell ejector chutes, rudder pedals, floor boards, wiring and tubing. The cockpit in general was painted in aluminum metalizer, sealed with FUTURE, and washed with burnt umber for a slightly dirty look. The top of the center wing section was prepped at the same time with panel lines and rivets, as it is the floor of the cockpit. The control stick pushrod and torque tube was fashioned from styrene tube and a sewing pin, with the stick itself of music wire with JB Weld handgrip. The side wall details were not installed until after the fuselage halves were prepped with panel lines and rivets and the cavity vents scraped and reworked (see "surface preparation" below). That process requires lots of handling and any fine construction will be damaged.
LANDING GEAR
The plastic landing gear supplied in the kit are adequate for a basic beginners build, but looked too flimsy to last…. and who wants to EVER have a main gear bust!? Consequently, new legs were built up by using thin steel music wire to bend and shape to hold a brass tube the same O.D. as the I.D. of the main wheel holes (use the HARD PLASITC wheels, not the rubber tires). The music wire was shaped and brass tube filled with JB Weld slipped over so that main strut and axle were in same alignment as molded gear. When cured, more brass was added to the strut, and more JB Weld swirled onto the thin music wire. When cured the JBW was filed and sanded to nearly the shape of the original mains. A second round of JBW was needed to get exact shape. These gear are VERY strong!
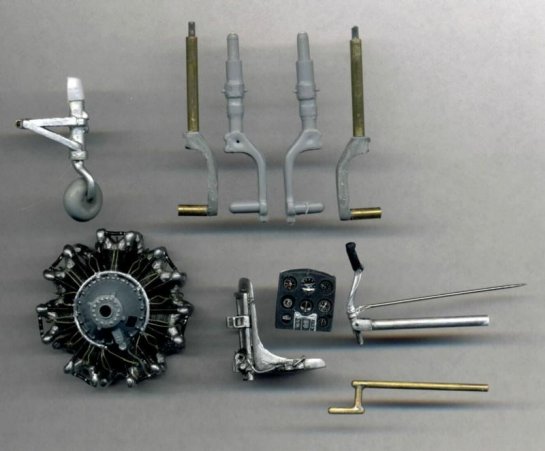
The tail wheel assembly is a single "blob" which glues into a plate in the aft fuselage…..no thanks. The wheel was salvaged from the unit, cleaned up, drilled and a thin brass tube axle bushing epoxied in. A new tail strut was made from, again, thin music wire and JBW which allowed the entire wheel to be free of the strut….nice. A styrene tail strut was made and the inner aft fuselage prepped to show interior structure with thin strips and rivet details.
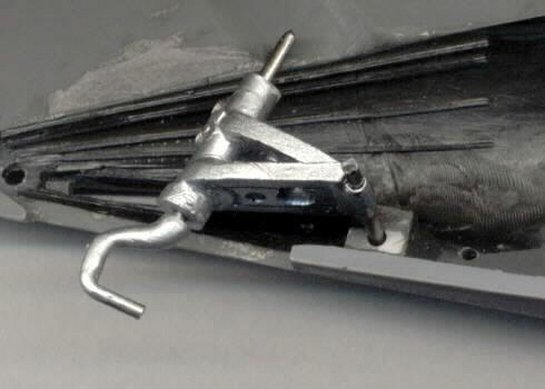
Assemblies were painted aluminum with a touch of burnt metal, sealed with Future, and lightly washed with black/umber mix. A small block was glued into each fuselage half to capture the strut pivot tube when joined, and the tail strut music wire is not glued in at all. It is held in by friction fit and a light coat of spray post-it adhesive so it remains able to rotate 360-degrees, yet won't fall out, and can be removed if desired for transport. While all the metal work was in progress I made a pitot tube of brass, since the itty-bitty plastic kit pitot tube would not last long at all. A tight fitting brass tube was mounted in the right outer wing panel to hold the pitot tube, yet leave it removable for transport. The brass one looks better too.
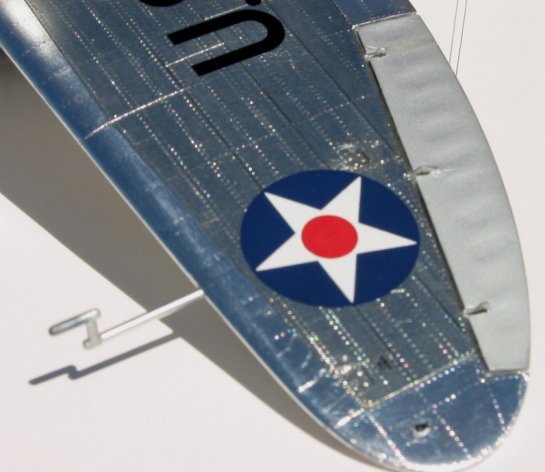
SURFACE PREPARATION
Now things start to get busy. The general layout of the HUGE raised panel lines was inaccurate. The entire model was sanded smooth and polished to a shine. Note from before, this must be done before any assembly as the parts will be handled very roughly! The fuse halves, wing panels, and tail surfaces were laid on my scanner and reproduced at one-to-one so I could carefully mark and layout all panel and rivet lines. Using many different photos from all possible angles I was able to map out the entire structure of the plane and derive the rivet patterns. First, panel lines were marked in soft pencil, masked with thin strips of DYMO LABEL tape, and scribed. Panel lines (and rivet lines) were not allowed to contact any edges as perfect alignment/continuation could not be guaranteed. After gluing halves, panel lines are "connected", and rivets "continued" through seams. Next, rivets "bumps" were pressed into the surface using pounce wheels, or freehand pin in tight spots. Again with the rivets, to keep lines straight they were masked with DYMO tape. At this point, the fine "wrinkles and dimples" that appear in an aluminum skin aircraft were applied. Using photos, the specific P-35 wrinkles & dents were mapped out, and scraped in along specific rivet lines with a #15 scalpel blade. The rough scrapes were finely smoothed with 600, then 1500 grit, and polished with old style Crest toothpaste to eliminate ALL scratches. This process eliminated many rivets, which were re-applied as needed. The fabric tail surfaces were given a light "dimpling" between stitch lines with the scalpel and sanded/polished. The cowl halves were sawed off at the aft cowl flap line and set aside. Two cavity vents on each side were back-scraped to thin the plastic (it is very thick here!) and cleaned up for a more crisp appearance. Now attentions was turned to the control surfaces. The hinges on the P-35 showed daylight through so each was drilled and jewelers filed appropriately. The hinge lines themselves are weak recessed lines that will not look good even with a wash applied. Using the various scribing tools and back edges of scalpels, the hinges were scraped and opened up to leave a rounded control surface and a deep recessed hinge gap. This looks much more 3-D and eliminates the need for washes. Also, the sides of the ailerons were opened up and trim tabs made "free". At this point the cockpit side wall details were installed and detailed (see "cockpit" above).
LIGHTS
Now, I wanted this model to have some "special" thing and operational navigation lights seemed to be the right answer. After much research, the only viable method was to use light emitting diodes rigged in parallel on a 12v garage door opener battery. Needing red, green, and white seemed easy, but white LED's are hard to find…and expensive. Tests showed that the red and green LED's were not bright enough to show through the lens, so the extremely bright, white LED's were used throughout. The peculiar nav light setup on the P-35 has teardrop shaped lenses on upper/lower and left/right surfaces. Each location uses a single LED, filed down to minimum thickness, and epoxied in place next to the nav light. Each nav light "pair" has a "lens", actually a rod, of the required color that passes through the tail/wingtip, and is shaped and polished on the end. When the white LED is lighted, the light shines up and down through each "lens", and generates almost zero heat…without a bulb filament to burn out. Due to clearances, even at min thickness, the LED's did not fit, so each wingtip/tail had to be internally ground down until light showed through the plastic to make room for the LED. Each LED was color checked (they do vary a bit) and matched to a position, wires soldered on, and tacked in place with a dab of medium CA. All part were mated and clearance checked. When satisfactory, the thin mounting areas were reinforced with 5-minute epoxy.
WING OUTER PANELS
Drilling out nav light lens holes, and allowing for wire runs into center section prepped outer wing panels. The lower aileron has external Friese hinges and the molded "lumps" are a poor replication. Each hinge was drilled out and a small slot left. Pairs of matching left and right hinges (the three on each aileron are different) were filed from thing brass stock and JB Weld epoxied into place. (see picture above) The excess brass/epoxy protruding into the inner wing was ground off with a Dremel cutting wheel, and a small dot of JBW applied to the hinge points to simulate pivot bolts and nut.
WING CENTER SECTION
The center section of the wing is a major structural piece on this model as it ties several sub assemblies together and sets the alignment of the entire model. The main wheel bays are barren and I detailed them by adding styrene strips/rivets to the inner surface of the upper center section. To make bay walls, I formed blobs of bakable clay into each half, carefully removed it, and baked it to harden. These clay pieces were closely formed and when hard baked, epoxied in nicely to fill in the center wing structure and provide a firm mounting point for the improved landing gear. As it turned out when fitting the main struts, the mounting holes were 3 mm too far aft and had to be re-drilled forward. Fortunately the baked clay allowed a strong structure to work with…whew!! Holes were allowed for running the nav light wires through to an exit point in the center of the wing below the front firewall. The clay also allowed me to use a small tipped Dremel grinding ball to bore out and shape the ram air inlet on the right wing leading edge which is not molded into the kit.
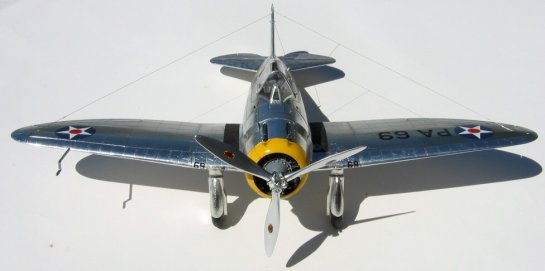
...more to come in Part 2
© Mike McLeod 2002
This article was published on Wednesday, July 20 2011; Last modified on Saturday, May 14 2016