HK Models | 1/32 B-25J “Strafer”
Reviewed by Brian Leitch
Hong Kong Models B-25J “Strafer”
Scale: 1/32nd
Accessory/kit #: HKM 32 01E02
Kit type: Injection w/ 514 parts x1 decal sheet x1 b&w instruction manual x1 PE fret
Where to buy: Your local hobby shop & Pacific Coast Models, Inc.
Manufacturer's website: hk-models.com
Approximate Cost/USD: $169.95
I gave this monster kit an “in box” review for anyone wanting to see what you get when you purchase this big kit. This will be a review of how the kit itself goes together.
Thanks to Ken Lawrence of Pacific Coast Models (PCM) for this review sample, and a chance to see how this huge kit builds up.
I was always fascinated with the B-25 Mitchell ever since I was a little kid, and my dad brought home a copy of the Aurora 1/32 B-25, that was meant to have Cox .049 engines in them, and was intended to be used for “control line” flight. It was boxed such that that never happened, and as a young lad I just played with it as a toy. I fell in love from then on. I don’t remember what happened to that model, I just remember how cool it was, so when HKM announced this model was coming to fruition and would be released, I got very exited. I jumped at the chance when PCM/HKM came to me and offered me a chance to give it a build review.
So let's get started shall we?
The kit comes in a HUGE box that as I mentioned in the in-box review, could have had much better art work, but this review is about the build itself:
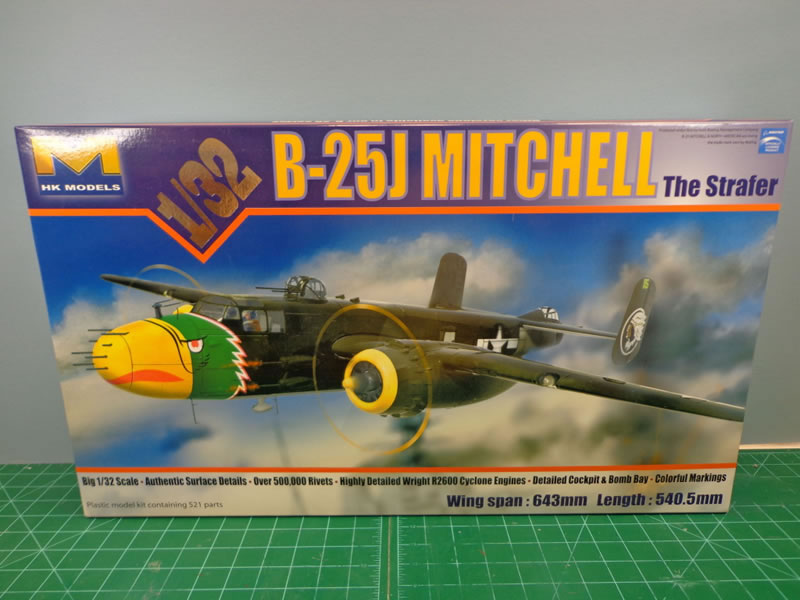
There are quite a few build reviews of this kit out there, and they are mostly OOB that I can see. This is NOT one of those. I decided early on, that this kit was big enough, detailed enough and will take enough time that I wanted to improve on things, and it would be worth throwing any and all AM/changes that it needed at it.
I did just that, and had a large pile of aftermarket I put into this kit, and let me just say up front, if you can afford it it was DEFINITELY worth it.
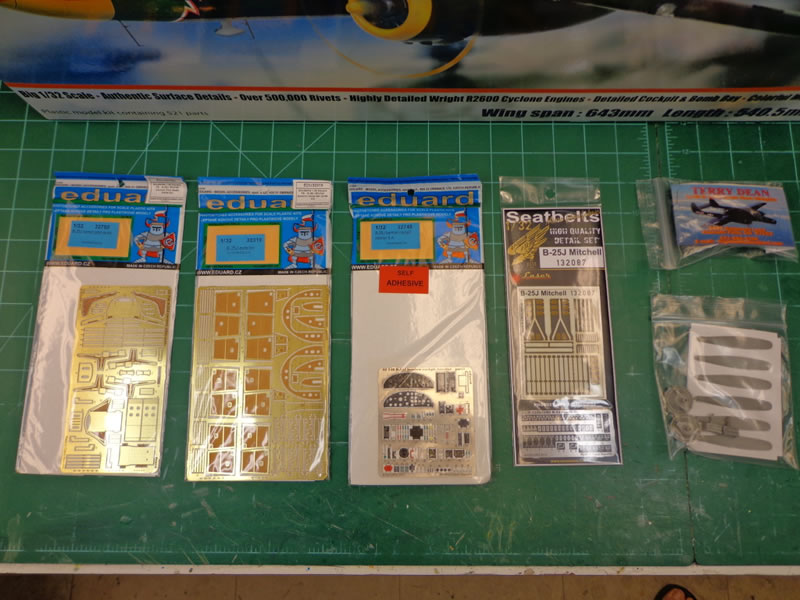
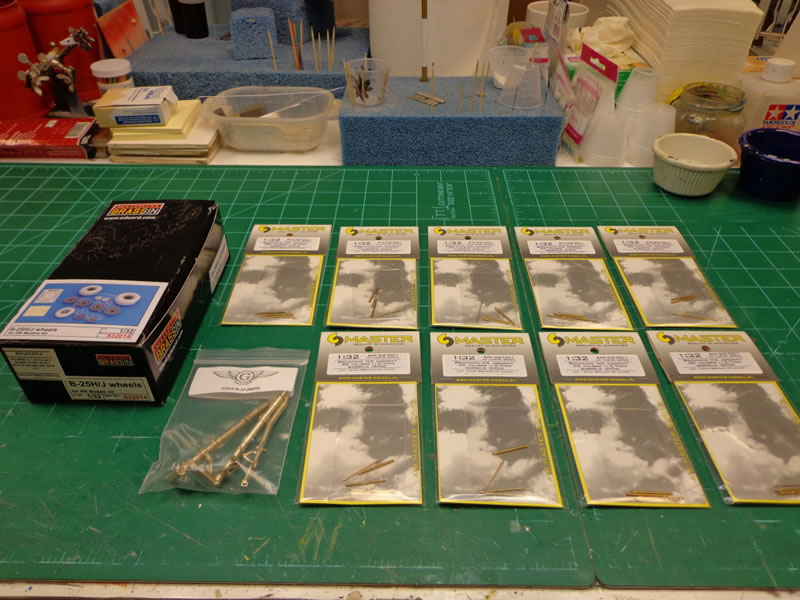
None of this aftermarket is needed, but as I indicated in the in-box review of this kit, there is some room for improvements, as no kit is perfect and we each want our own personal touches to things. There is a LOT HKM got right with this kit, and some things that really needed to be changed in this modelers humble opinion.
Again, there are plenty of OOB build reviews out there, so this BR of the HKM B-25 is for those who want to dump a little extra time/effort and AM into their kit.
I started off in the normal place cockpit/interior. This kit has a LOT of it too! Here I replaced /added to the OOB interior replacing some parts with the VERY nice looking Eduard PE parts, and textile seatbelts from HGW, and some resin bits from Profimodeller:
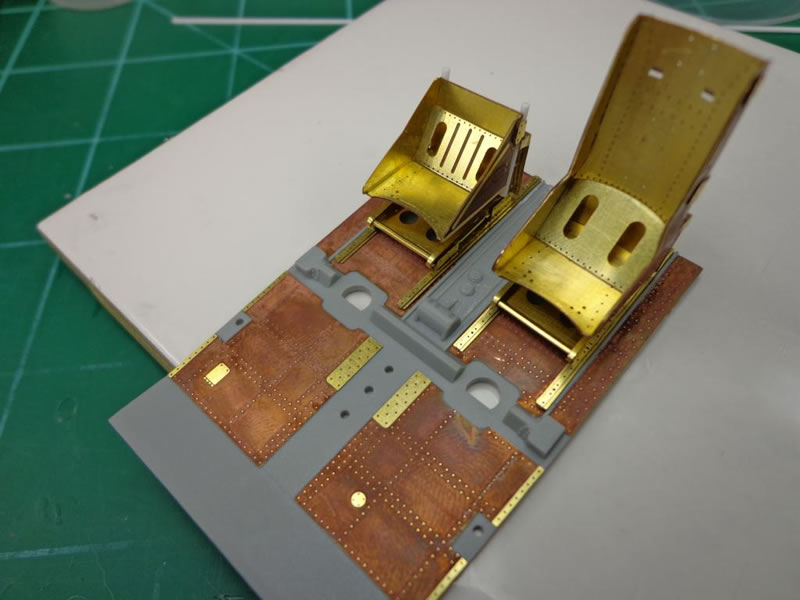
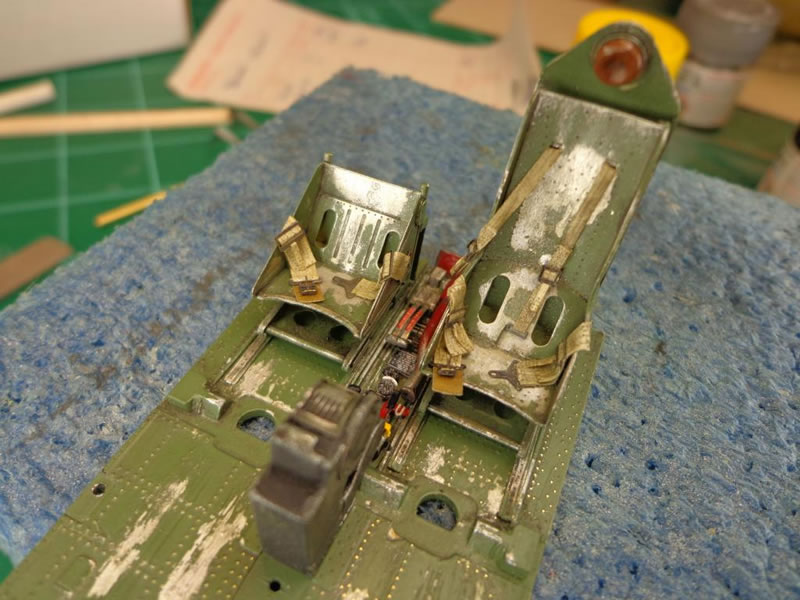
The cockpit was completed with the Eduard, Profimodeller, and HKM OOB parts along with some scratched bits and dry fitted to the fuse:
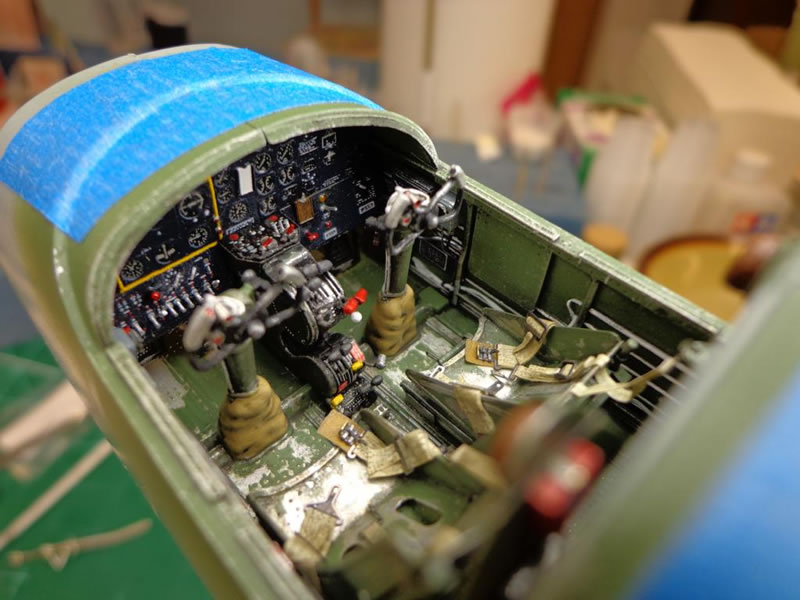
Next up I started on the separate bomb bay HKM gives you here. Now keep in mind in the end, really not much of this at ALL is going to be seen but in continuing with the AM theme, I used some Micro-Mark raised rivets here to add some detail, after filling and sanding all of the injector pin marks:
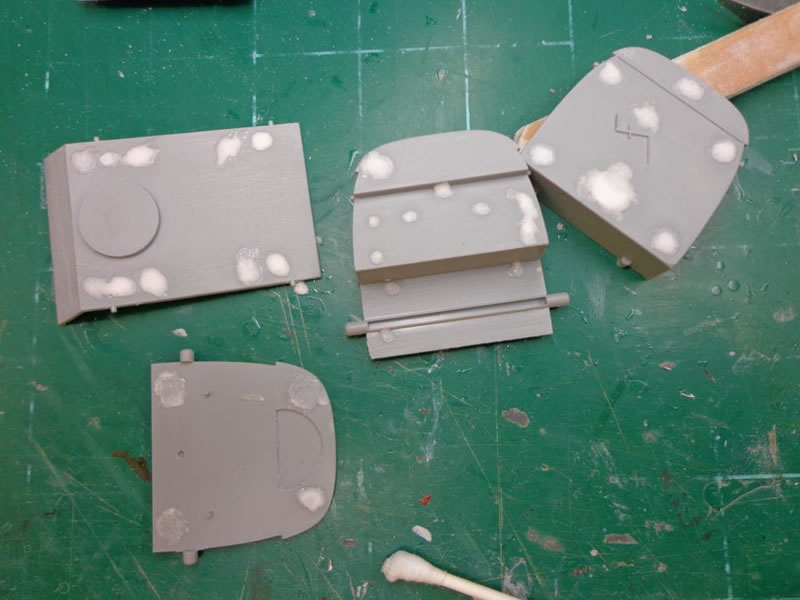
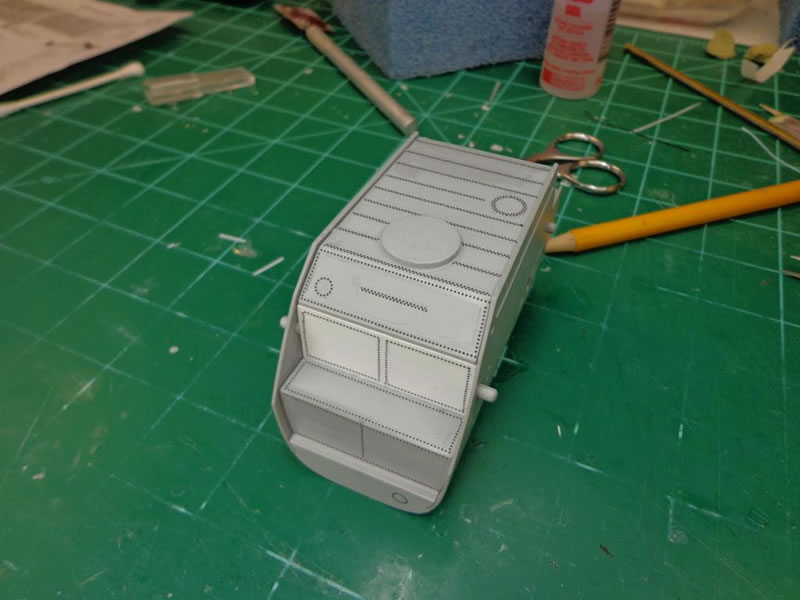
I also used Eduard PE here as well as using some lead fishing wire and mini brass nuts from Scale Precision:
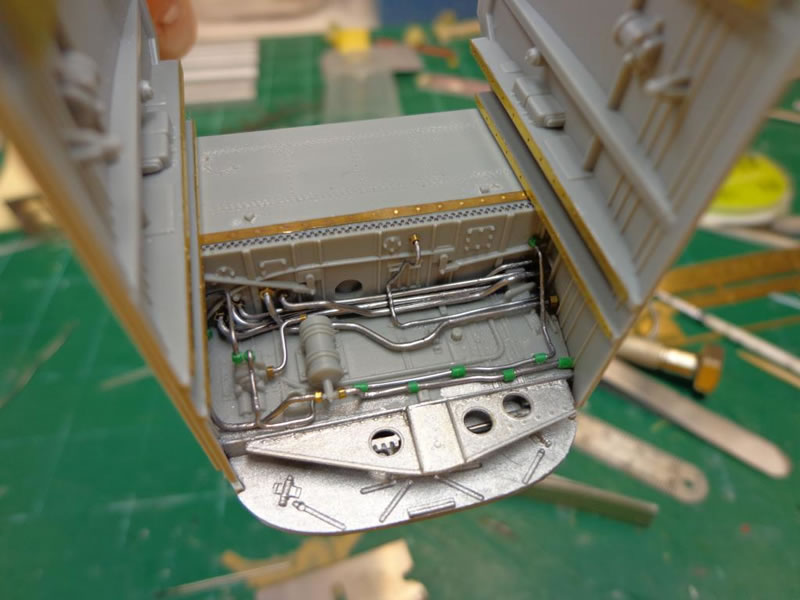
The bomb-bay was completed and painted using EZ Line for wiring and Alclad for paint:
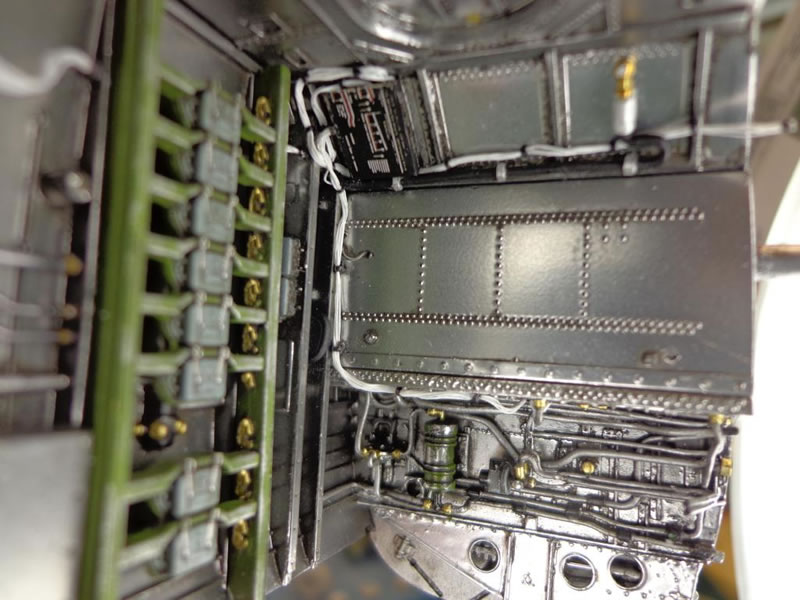
I then moved on to the main fuselage interior, which included using the OOB HKM .50 cal bodies (not much seen here for the waist guns either) and some Master Model .50 barrels. I also got to work assembling the empennage parts as well. For the interior waist guns, I also filled and sanded a TON of injector pin marks and capped the bottom shelf of the waist gun windows for the .50 supports with card stock:
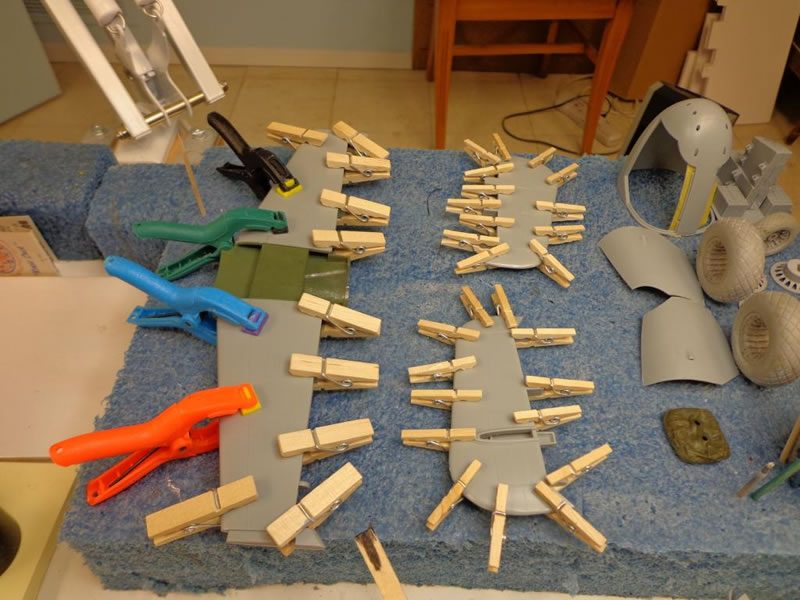
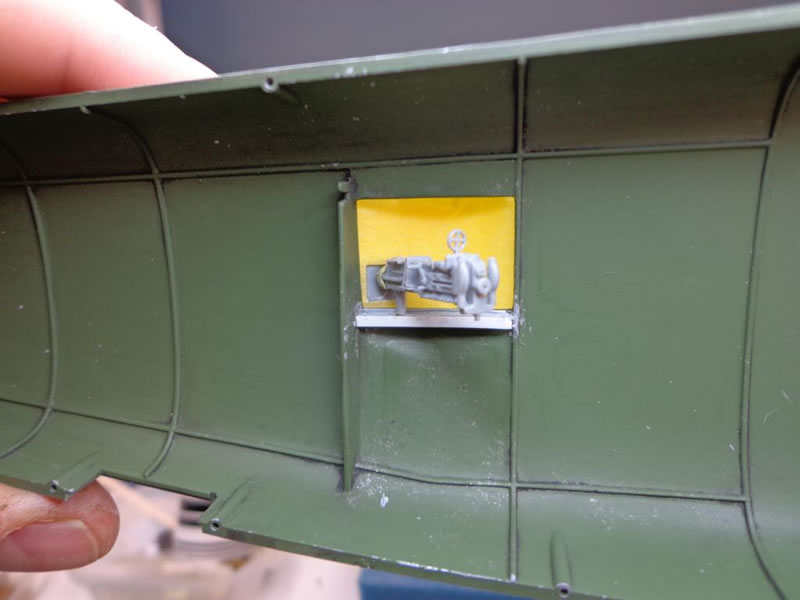
Next up for this big kits interior was the top turret (which I did NOT use PE on as the OOB parts seemed to look OK for what you could see):
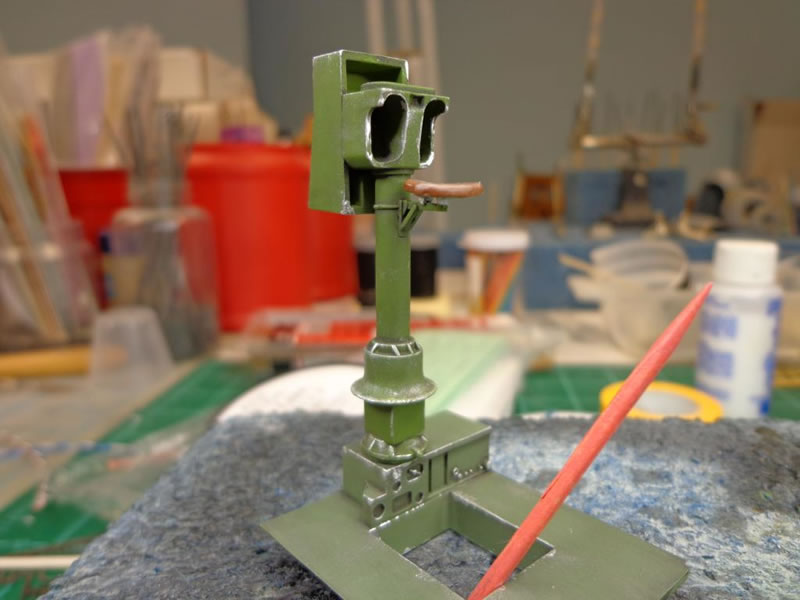
Then moved on to complete the tail gunners section, again utilizing textile belts from HGW, and some Eduard PE since this area was setting under a lot of “glass” and would be much more visible in the end than other hidden areas of the build:
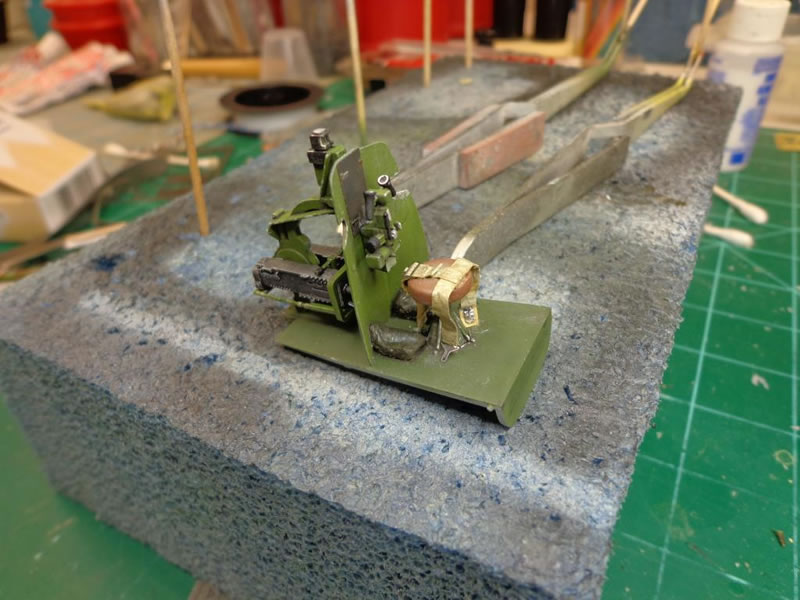
Although there are now AM parts, I fashioned my own scratched up tail gun .50 canvas cover out of some tissue/paper towels soaked in thin CA, with the stock OOB holes cut out and inserted, then painted as I the OOB parts were just WAY, WAY to pronounced, and anyone using the OOB tail gun cover will soon discover that this part prevents the .50 cal barrels from actually being inserted into the OOB .50 cal bodies:
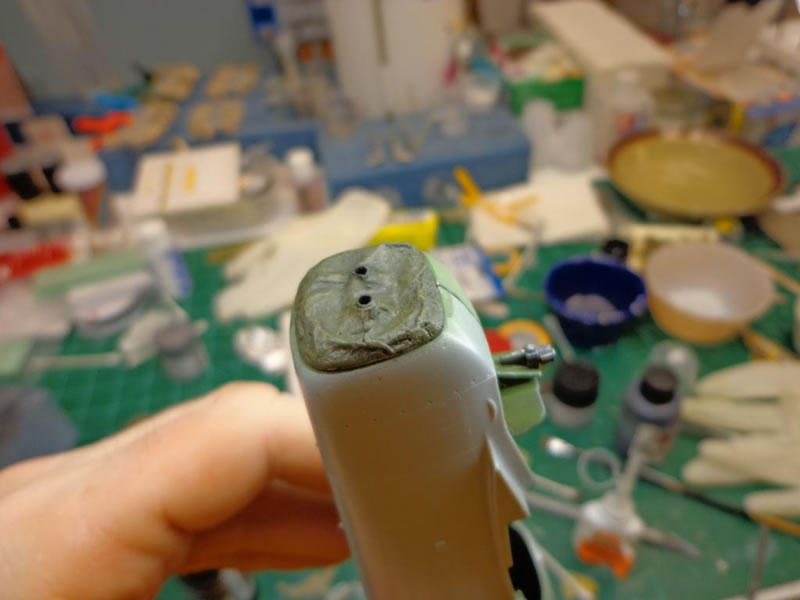
You can see my scratched part VS the OOB part, and it gives you an Idea of how out of scale and pronounced the stock part really is:
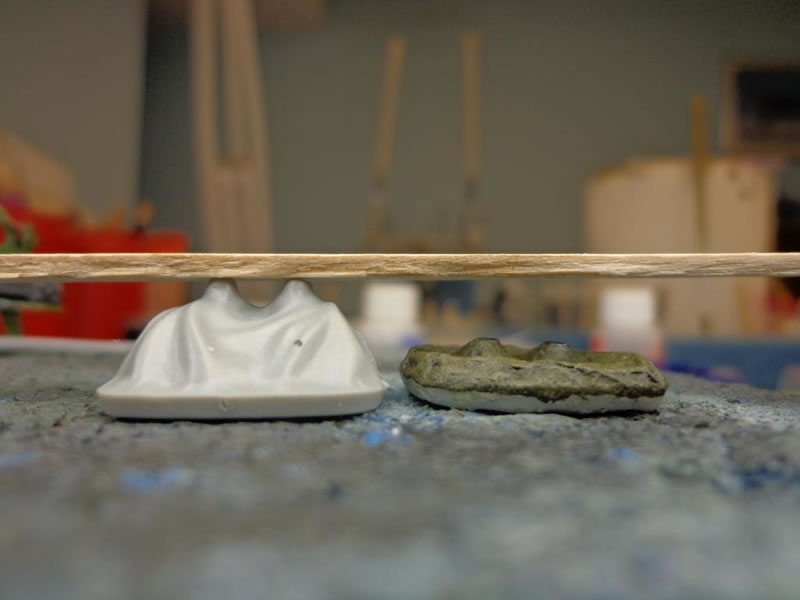
After completing the pit, bomb-bay, upper turret position, & tail gunner’s position it was time to close up the fuselage. I used normal slow drying plastic cement here to give me time to get things aligned correctly. TAKE YOUR TIME HERE! Slow down and double/triple check here because there is a LOT that needs to come together to have the fuse fit right.
It was at this stage I test fit the wings, and started to get an idea of how really big this kit was going to be:
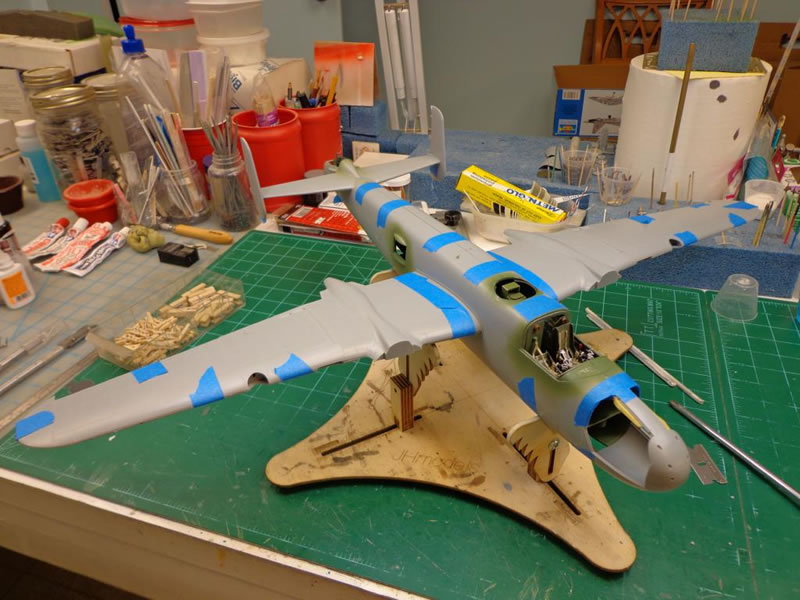
Next up, I started dry fitting the very nice Eduard/Brassin resin wheels for this kit. The wheels are very nice, but again, not being able to leave things alone I did NOT like how the stock appearance of these wheels really looked to me like they were almost bordering on flat. So, I took them and added a strip of flat card stock to the bottom of all 3 wheels, then added in my own continued tread detail, and primed before paint:
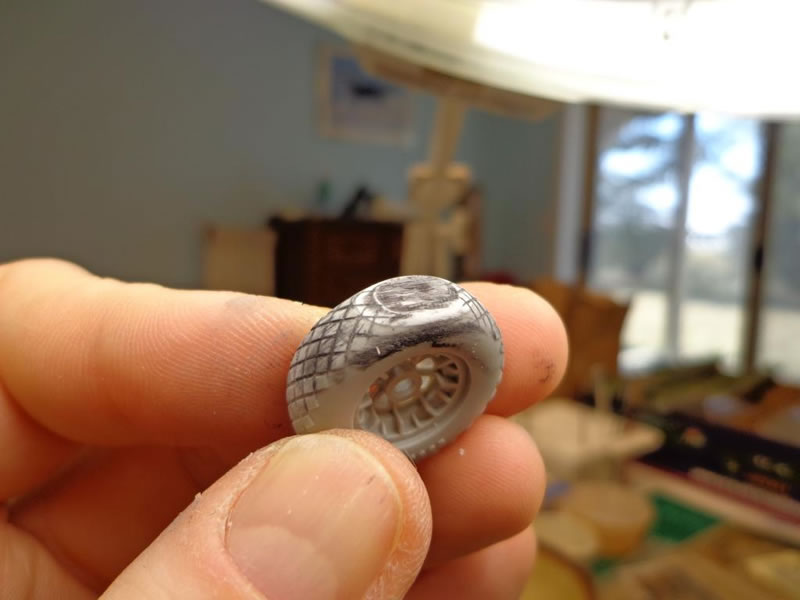
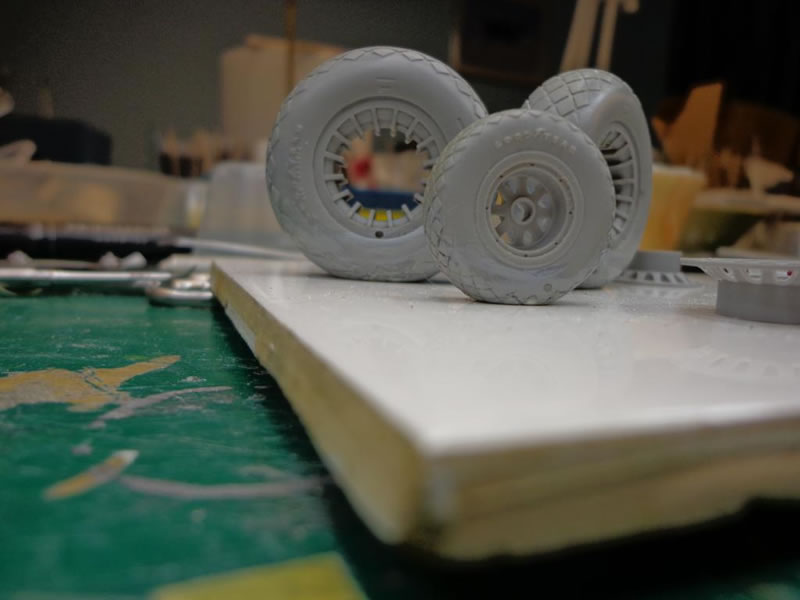
Next, utilizing the wonderful G-factor AM brass gear (HIGHLY recommended for this kit!). I taped the nose on for fit, and set her up on her gear to see the new stance of the model:
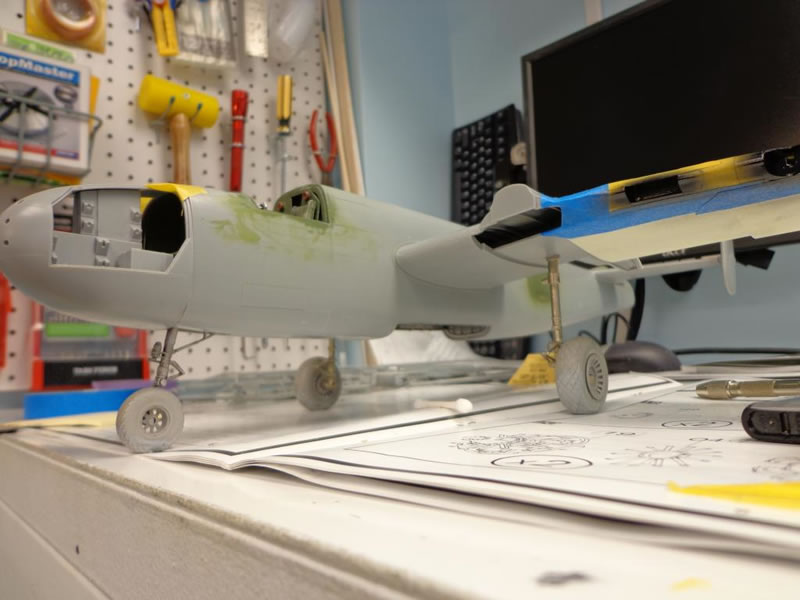
After dry fitting the nose, I discovered that she was going to need a lot of nose weight to keep her from dragging her rear. A LOT of weight. I purchased the Terry Dean weight set, which weighed in at a hefty 6.5 Oz. Again not really liking the positioning of where these weights had to be put, I chose to add in my own weight of #9 lead shot-gun shot. I wanted to be SURE she would set on her nose, so I put damn near 6.9 Oz of lead under the gun compartment, in the center .50 cal housing, and also some ¼ Oz self sticking lead squares on the back wall behind the .50 cal center console:
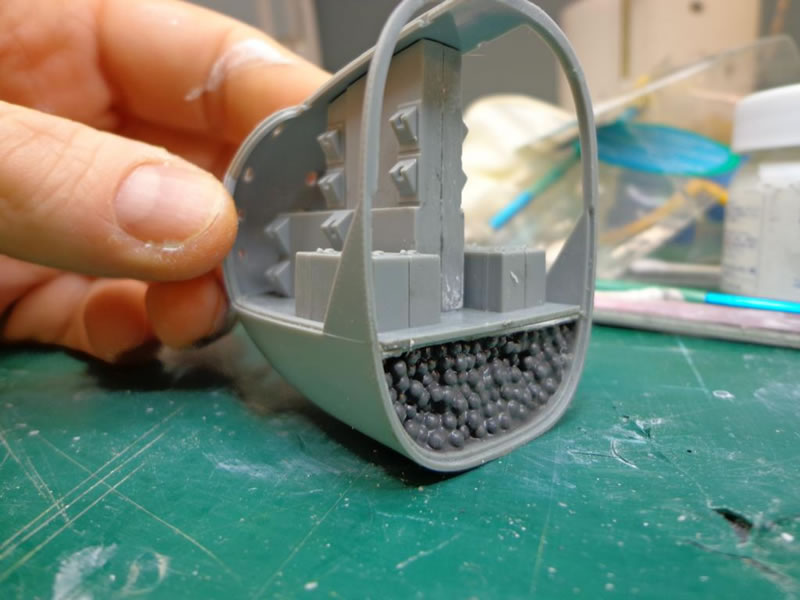
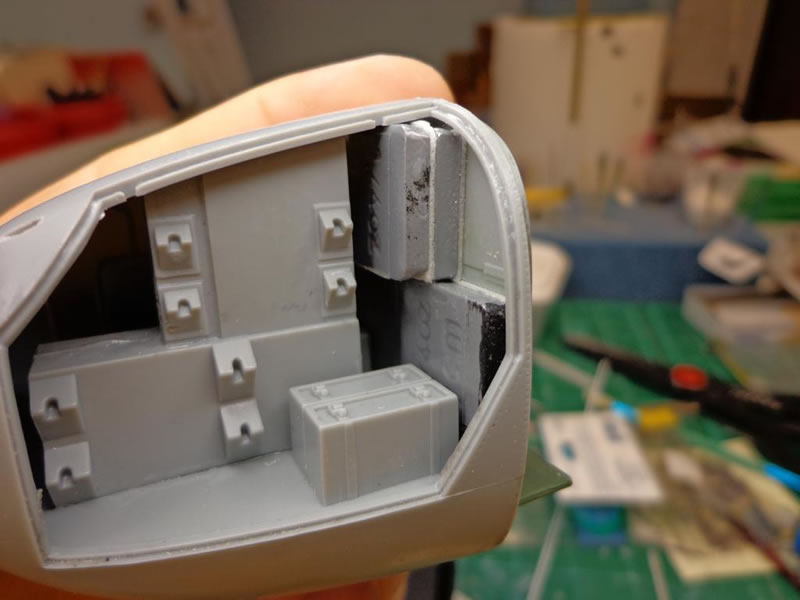
Now it was time for the power-eggs and the propellers. This is another slight area (not really too many of these type of areas in this kit) of this kit that is a let down. The engines are really great, but have an issue with the pushrods - There is an entire extra set of them:
The issue here is you cant just leave the erroneous set out, or the engine does not set as far forward as it needs to, to get prop clearance, and set in the cowl properly. What I did, is just to chop off the push-rods from the OOB push-rod ring, and install the ring without the extra set. For those who are not opening up the engine cowls, this should be a satisfactory solution. For those who are opening up the engine cowls, you may need to find another solution, since the empty ring will possibly be very visible from the side:
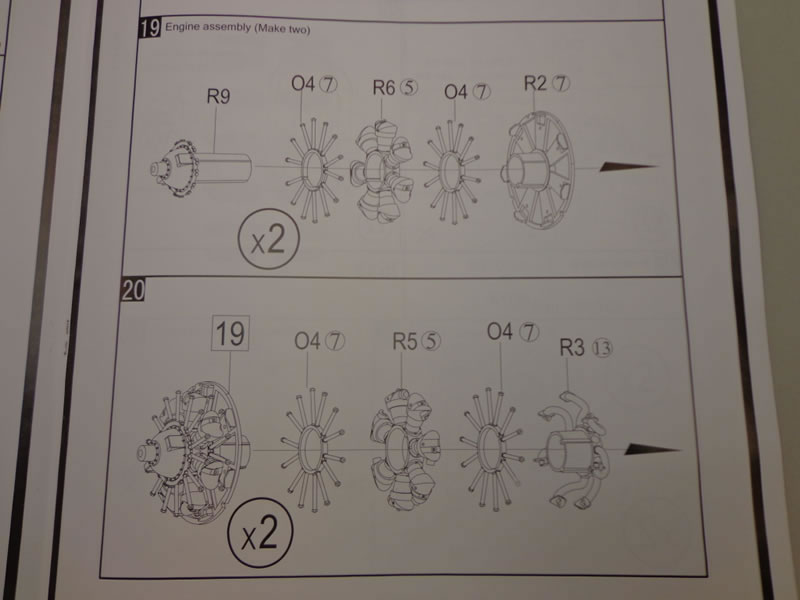
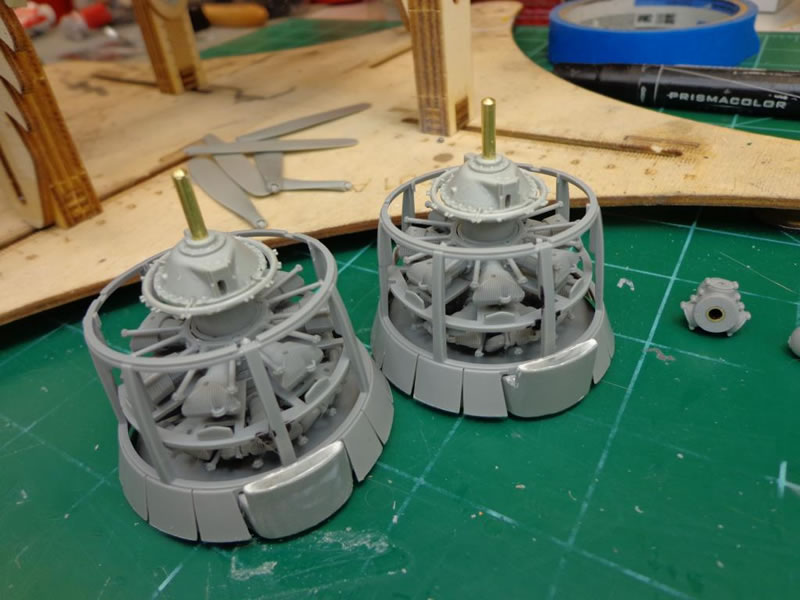
The last of my fairly minor gripes is the continued miss on the props. There are 6 blades, and they set very prominently out there, as in all big twins, so their very evident “waffle ball bat” shape stands out quite distinctly:
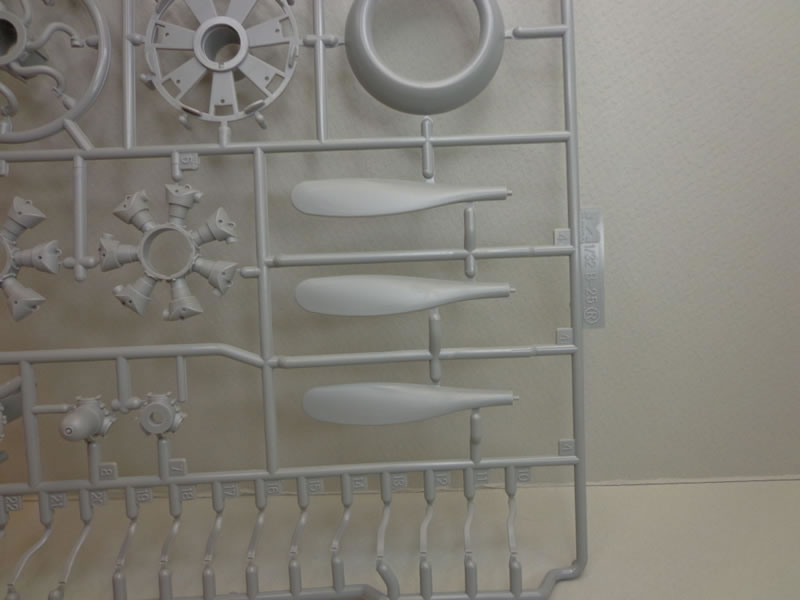
I solved this by utilizing another wonderful AM correction set from Harold @ AMS Models that gives you a full set of 6 corrected blades, as well as the missing governors for each engine the HKM did not include as well.
I used another wonderful invention for us modelers with extensive AMS disease; the 1/32nd “Prop-Master” jig for assembling AM props from 2 to 5 blades. This made it way easier to use the OOB hubs and incorporate Harold's props at the correct angle:
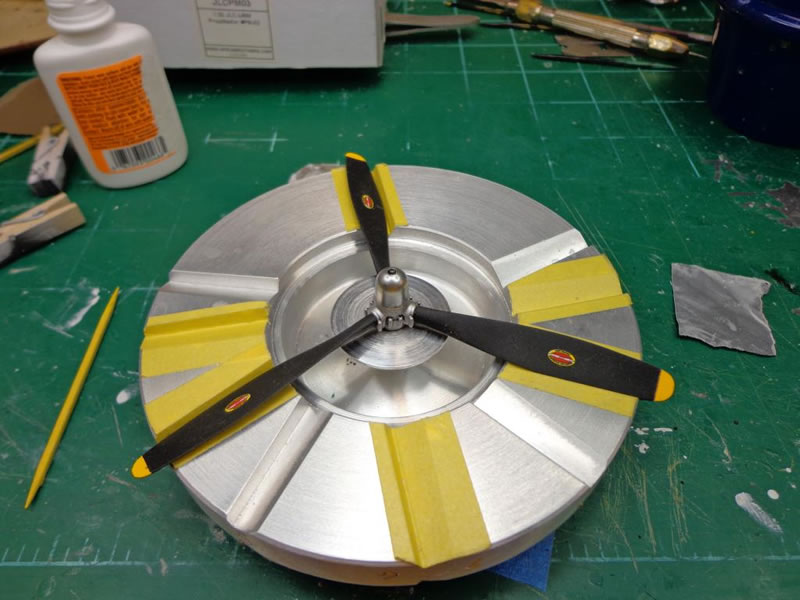
I then completed & weathered the wonderful-looking HKM engines along with Harold's prop set, again utilizing some lead fishing wire, and brass nuts from SP to add some detail and realism:
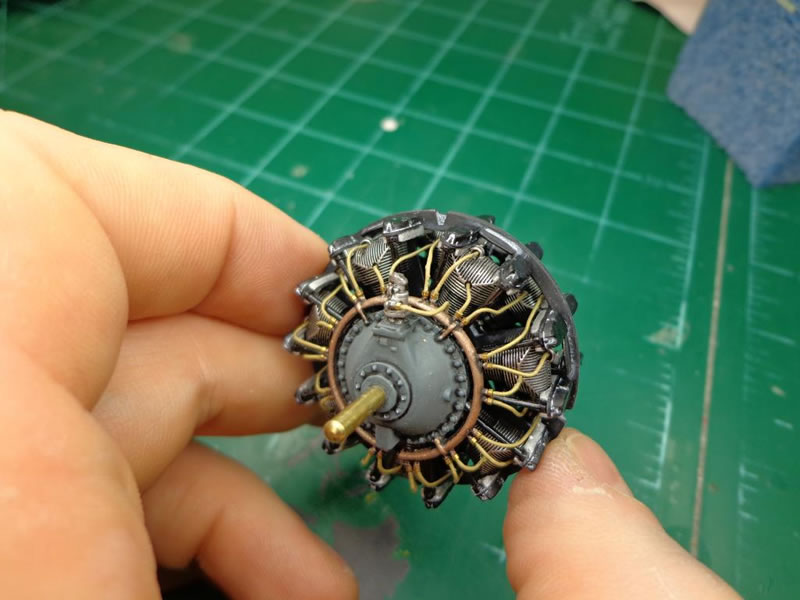
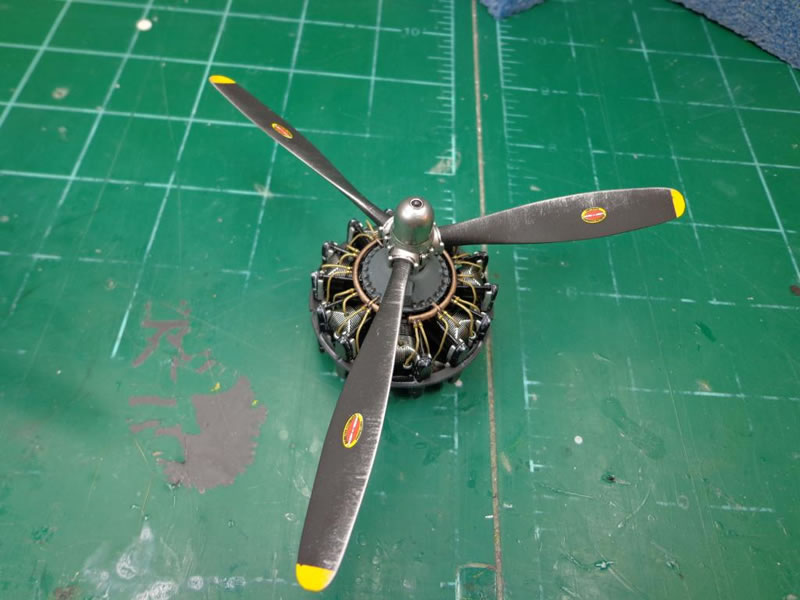
Now it was time to address something that really did bother me about the looks of the kit that had to this point not been address by any build reviews (not that I could see anyway).
That was the cowl openings. I guess certain things just bother certain people, and this really seemed to bother me. I kept wondering what it was that seemed a bit “off” about some of these builds that I saw completed as far as the engine cowl openings went. It was the fact that when compared to pics of the real thing, the HKM cowl openings were way too closed off, and their lip wrapped around quite substantially into the cowl itself, where the 1:1 had much more of an open appearance:
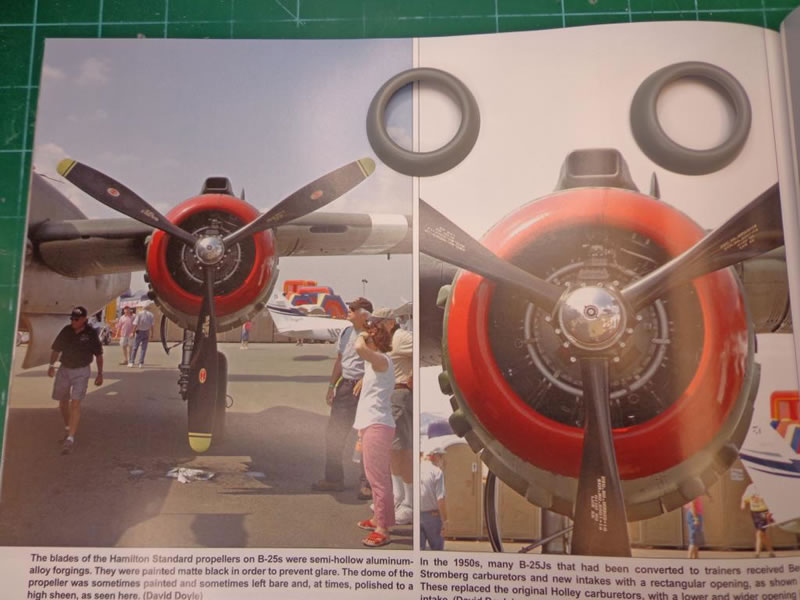
I solved this by having a professional wood worker turn me a wooden dowel down to the appropriate taper, as to center the new wider opening, and have things just slightly more open than the stock parts:
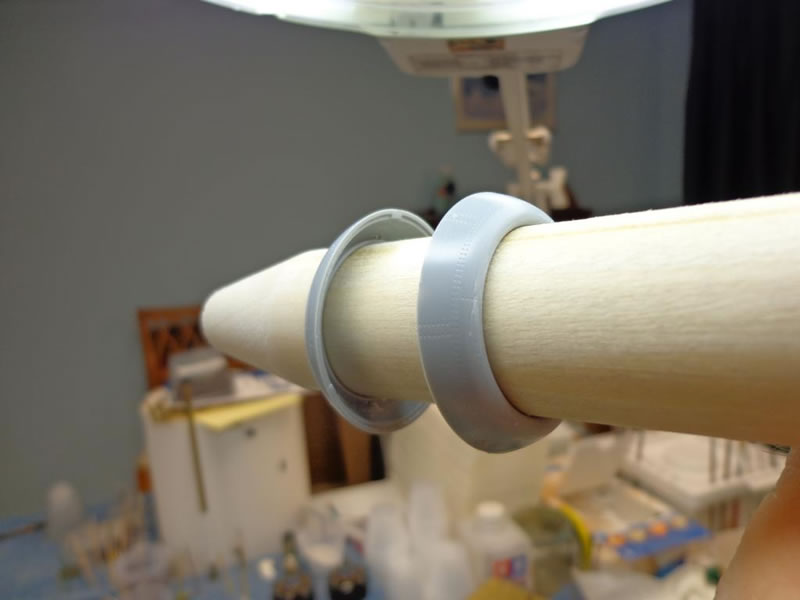
After sanding and shaping the openings till I was satisfied that they appeared MUCH more scale looking in appearance, I held the stock OOB cowl openings over my improved parts & the .5 or 1mm difference in opening size (IMHO anyway) becomes VERY evident:
Stock OOB:
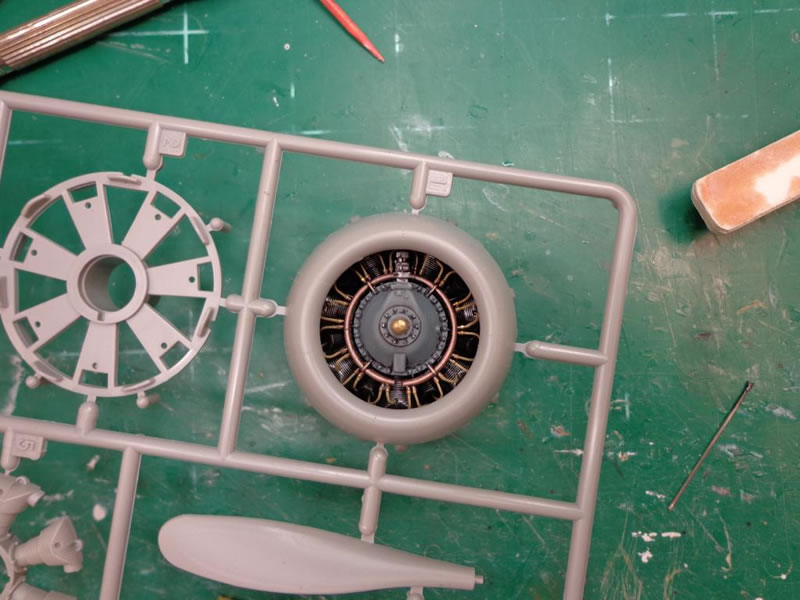
Opened up part:
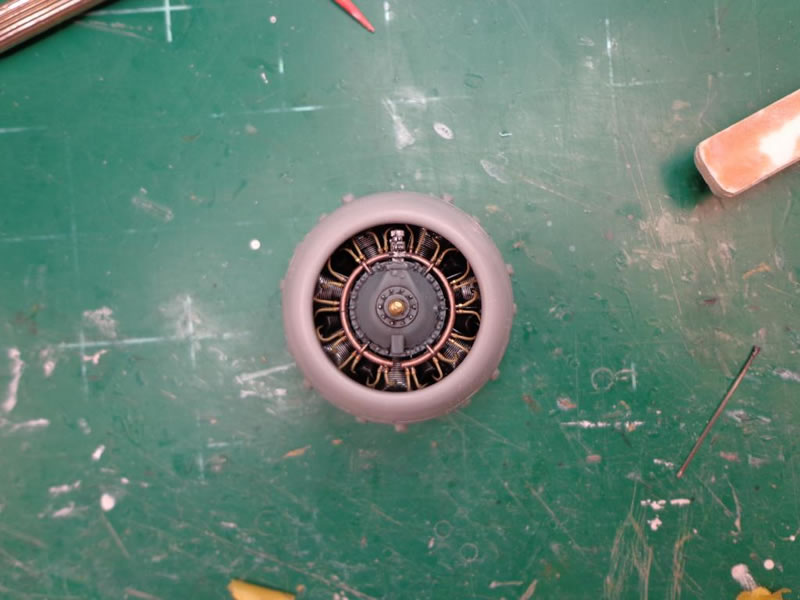
To my eyes that small change made a night and day difference:
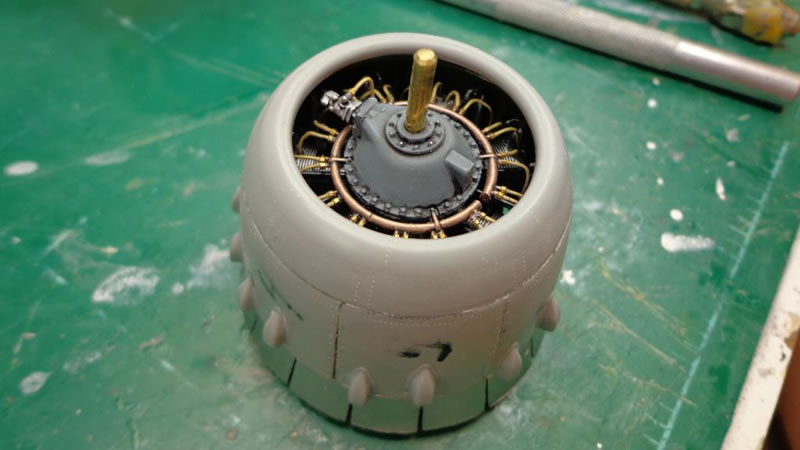
I then painted and weathered the cowls, and would end up adding the power eggs at a later stage in the build to avoid damaging them:
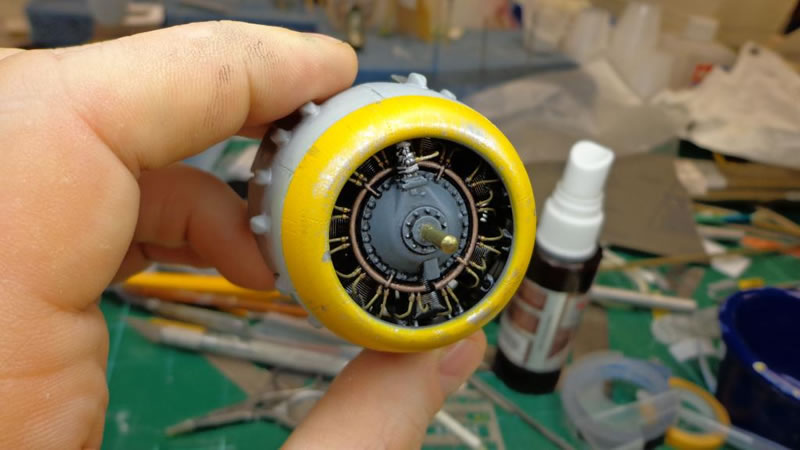
Before adding the oil cooler flaps, (which HKM only had depicted as rods sticking out of non-existent holes) I marked off the sections behind the ring, and opened up holes for the oil cooler flap actuators for another bit of realism:
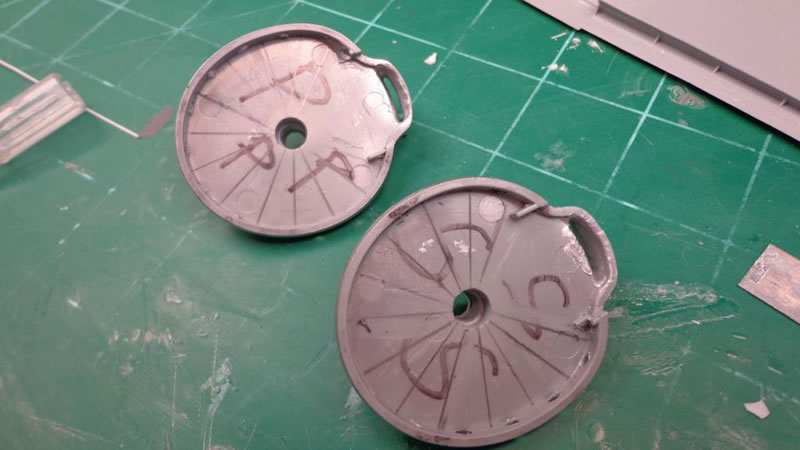
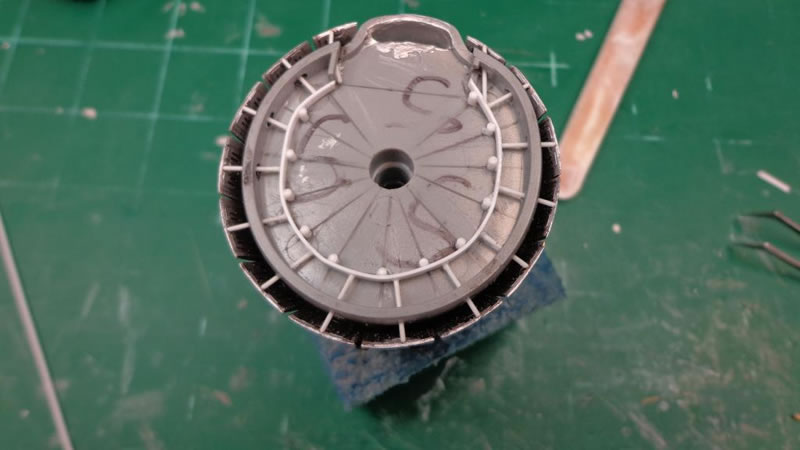
After deciding really from the get-go what scheme I wanted, it was time to start on the finish. I decided early on, I wanted to use Eli’s decals from Zotz, to represent the 345th BG, as “Lady LiL”, a NMF airframe with lots of color, and some great nose art. The Zotz decals were awesome and I really have to give Eli at Zots a lot of credit here. Because I have never really had any luck with/nor like the looks of Alclad as an overall finish, AND because a mentor of mine (Ken Friend) taught me how, this was an opportunity to do something with the big Mitchell that I had not seen yet, and that is use kitchen foil to represent the natural metal finish.
To do this I utilized all my tricks of the trade, including various burnishing tools and a lot of different materials to “grain” the foil to get rid of that super shiny look, and get a more realistic dull/titanium/oxidized look that aluminum gets when exposed to the elements:
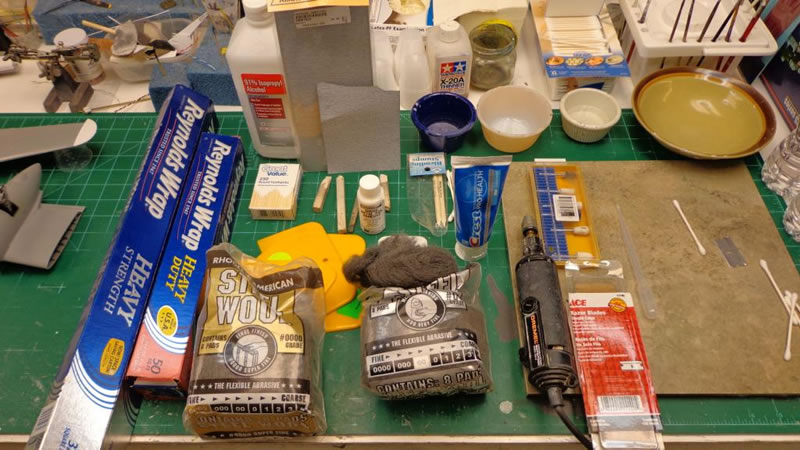
The process starts off by graining the foil first with the material of choice (toothpaste, sandpaper, steel wool etc, etc) then cutting an oversized piece of foil, and applying thinned Micro-Scale metal foil glue to the back side using an air-brush at very low PSI:
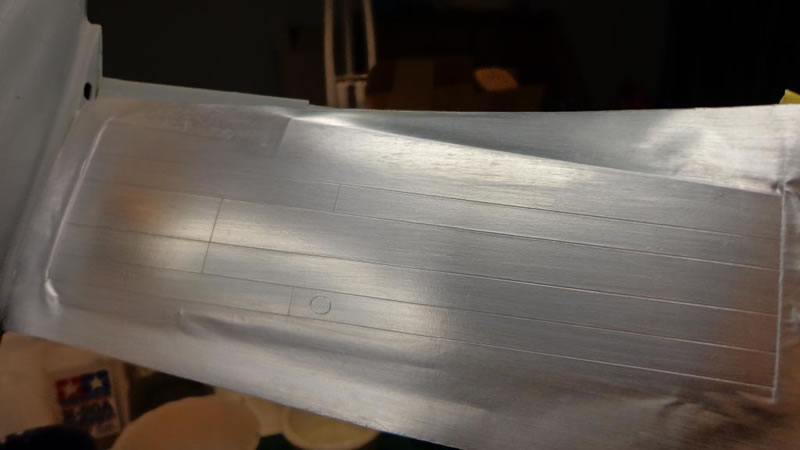
This is a VERY labor-intensive process, as the way I apply the foil is similar to the way the real thing is assembled, and that is panel by panel. I won’t cover this entire process here as there are some tutorials on LSP on this, and there is just way too much to go over to explain the entire process thoroughly. So, as this is about building the kit itself, I will just show some in progress shots of the foiling process as it went on, panel by panel. As you can see, the graining process does create some nice effects and differences to each panel, as even panels right next to each other reflect the light slightly different:
When you grain these panels, it gives the foil a microscopic (seemingly) level rough surface which is perfect for paint adhesion. I use strictly enamels for overall paint on airframes and when the foil is grained, you don’t even need to use primer to have the enamel paint stick. Here (using the Zotz paint masks included with their decal set) I applied the same yellow right over the foil, that I used on the engine cowlings, as well as shooting the OD for the anti-glare panel:
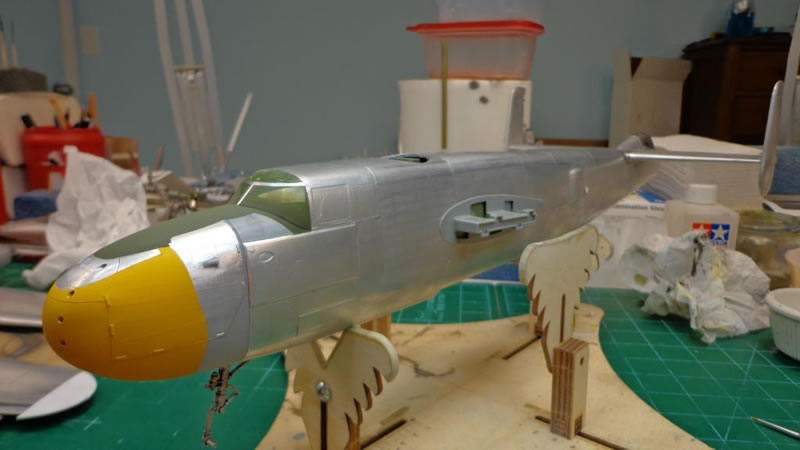
"Lady Lil" had its side pack .50 cal cheek pack guns removed completely after joining the 345th BG, for structural reasons, but this left her with very prominent gun blast marks that could be seen in period pics of her in the Philippines in 1945:
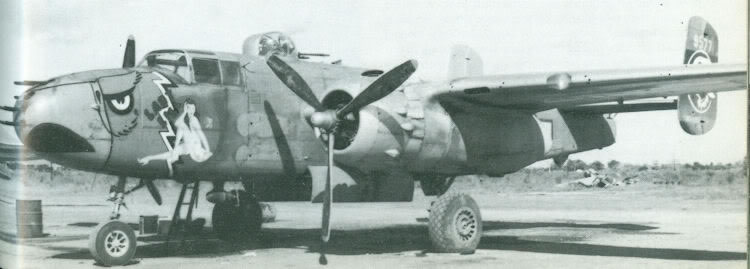
I replicated this using Tamiya smoke, followed by a gloss coat, then applied the Zotz decals over this:
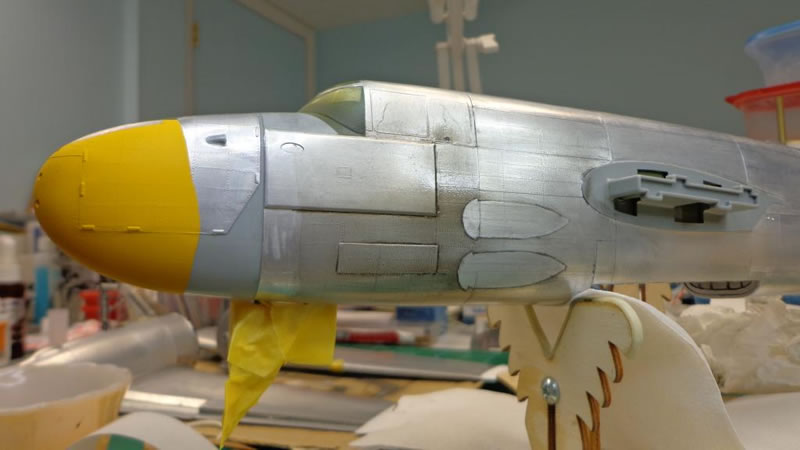
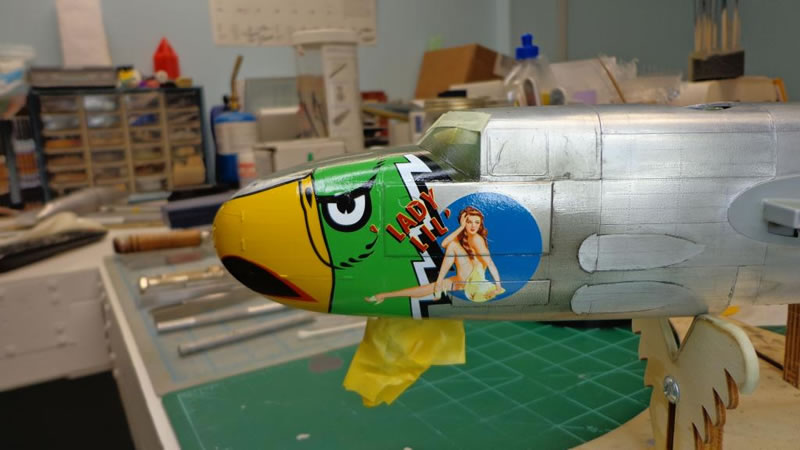
This was followed up by a flat coat of Model Master Lacquer flat, and a start on the stars and bars decals:
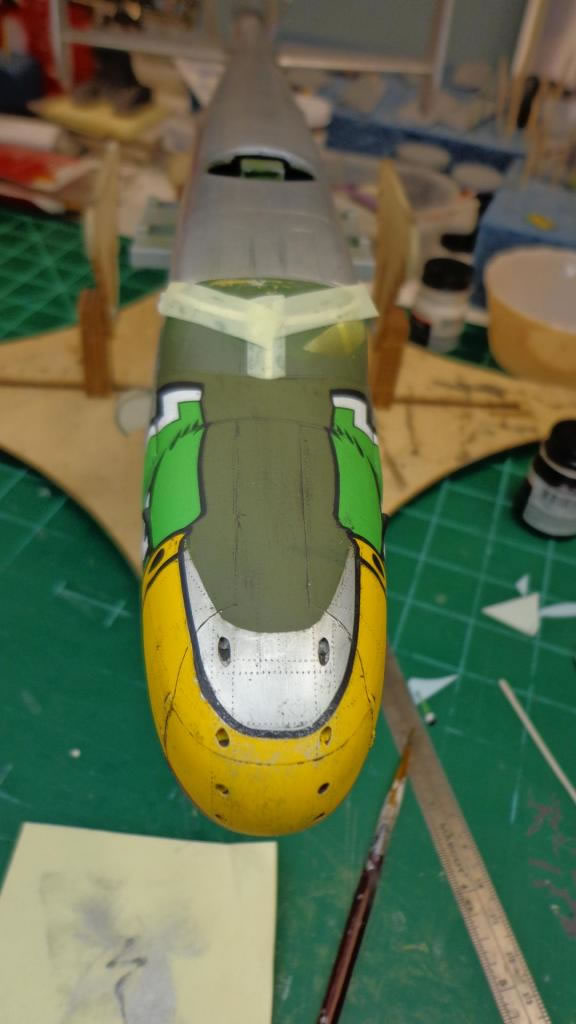
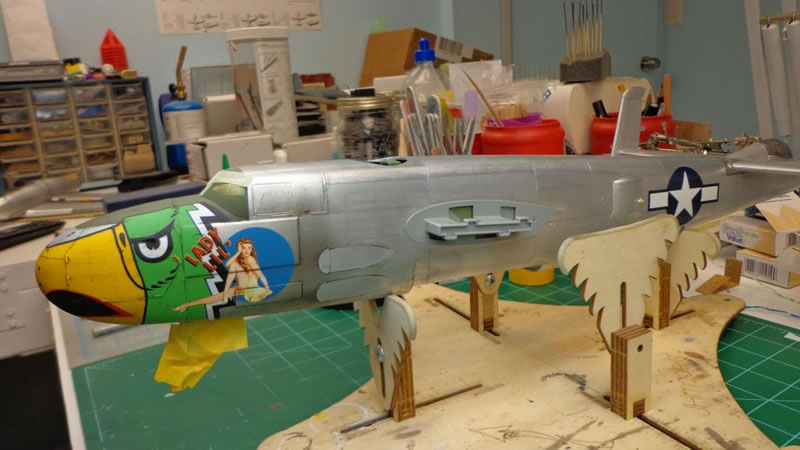
Then, it was time to add the wings and get them glued in their final resting place. HKM did a fantastic job on the fuselage to wing connections…the best I've seen yet as a matter of fact.
The connections are VERY tight (as they should be) but slipping the wings on is no easy task when you have a bunch delicate stuff hanging off of the airframe, like bomb-bay doors, 14 .50 cal guns, antenna and the like. If you choose to keep the wings removable, the likelihood of breaking one of these delicate parts off when attaching or removing the wings for a competition, or show, is quite high each and every time it’s done.
So, as good as the wing/fuse connections are, in my case I chose to attach them permanently to reduce the risk of breaking parts off. I used some 15 min epoxy to join the wings on, and prior to the epoxy setting it actually acted as a lubricant and the wings snapped into place with MUCH more ease then when attempting this dry.
WORD TO THE WISE – IF you do keep the wings removable use a natural/non oil based substance to lube the wing/fuse joint and you will be MUCH happier I guarantee.
Wings now fitted permanently in place:
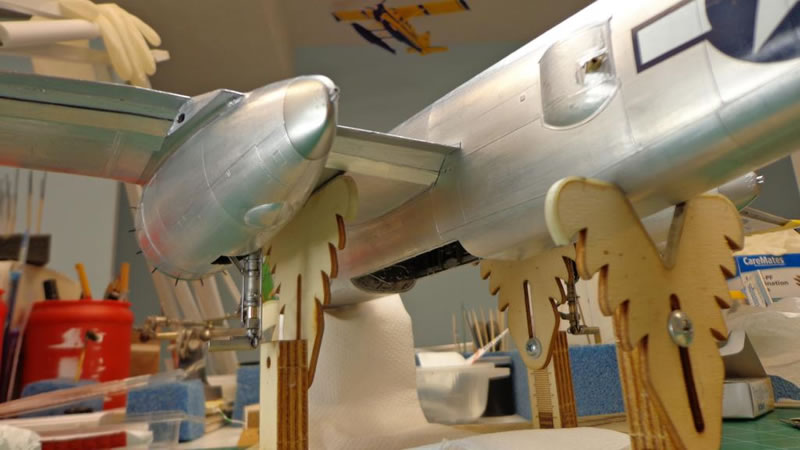
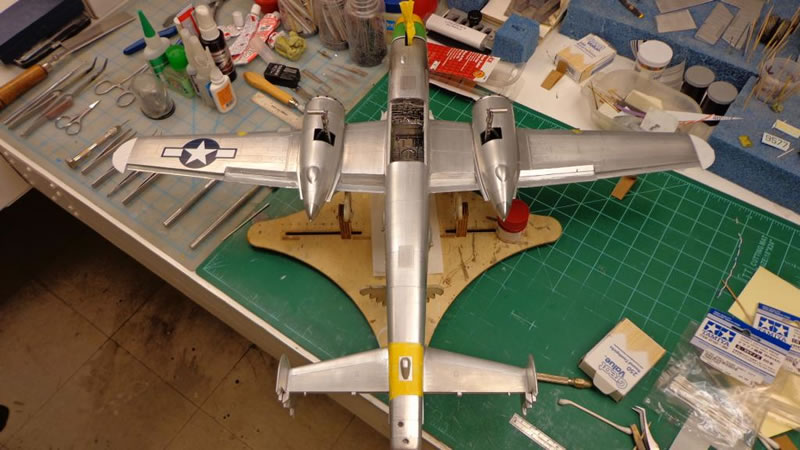
Then I finished applying the wonderful Zotz decals, and finished up some of the detail bits like the bomb-bay doors, again utilizing Eduard PE which IMHO added a great deal of detail and realism:
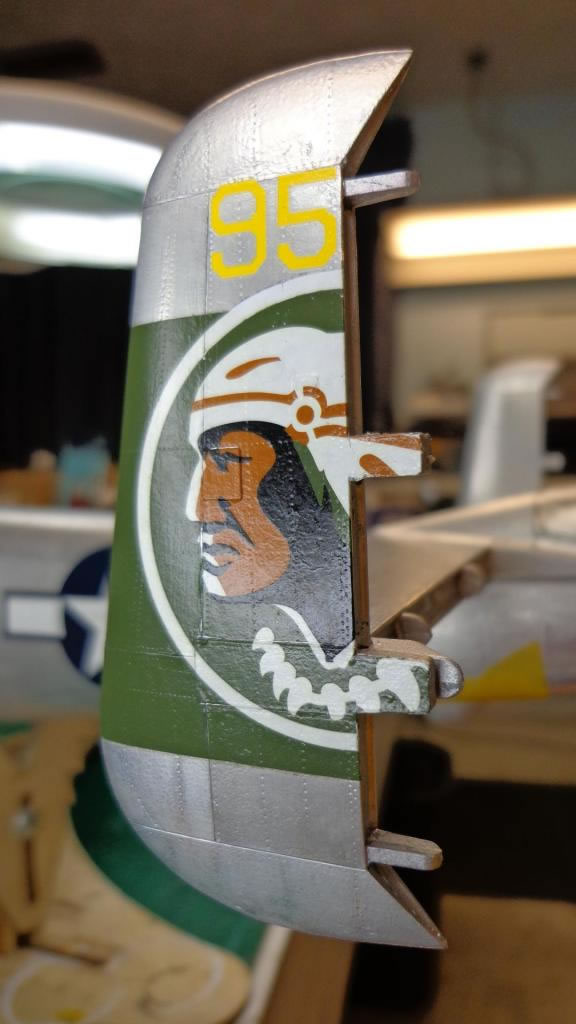
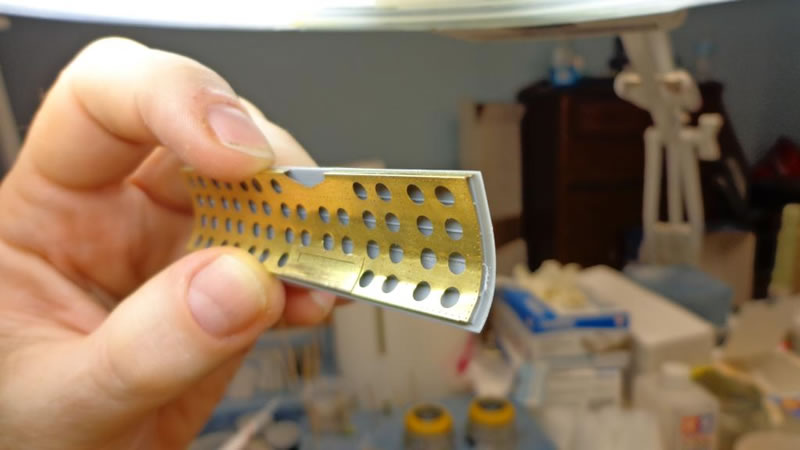
It was now time for final assembly and weathering. The NM foil finish takes VERY well to natural clay based washes and weathering, so it is very similar to weathering paint, only if you make a mistake and don’t like something, you can just wipe it off using anything from 90% alcohol to lacquer thinner!
Assembly proceeded; starting with attaching the power plants as well as using Tamiya dull aluminum to paint and attach the fabric flying surfaces:
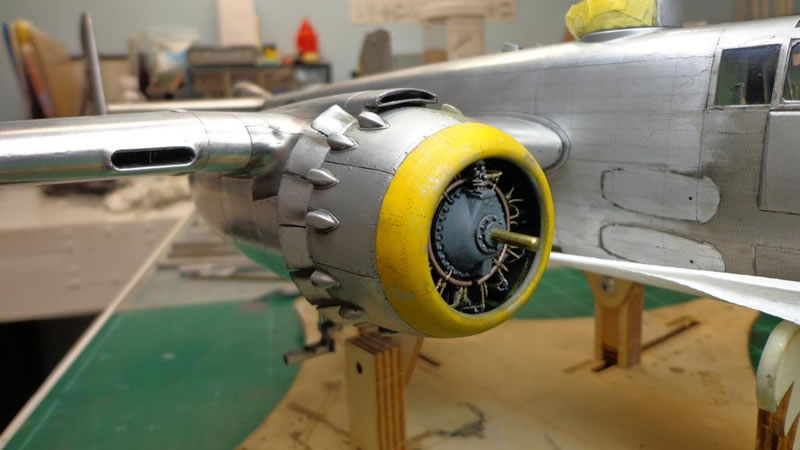
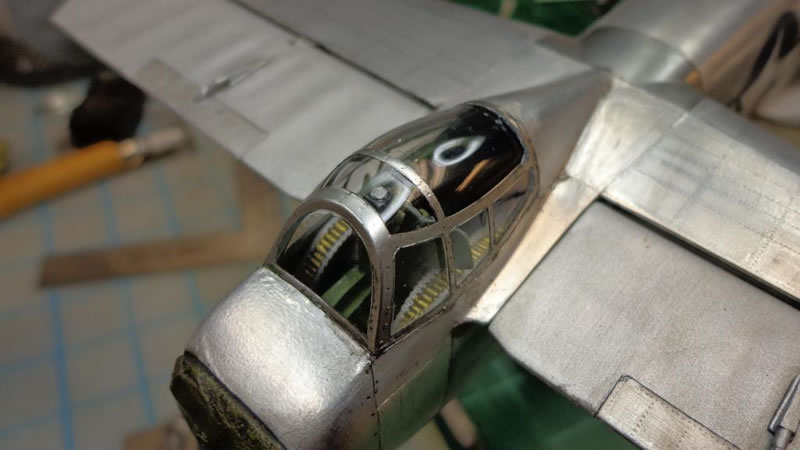
Now it came down to final assembly of the air-frame and detail parts. I foiled and attached the upper turret, and then used Tamiya weathering pallets to apply some egress oil cooler vent streaks as well as some fuel streaks:
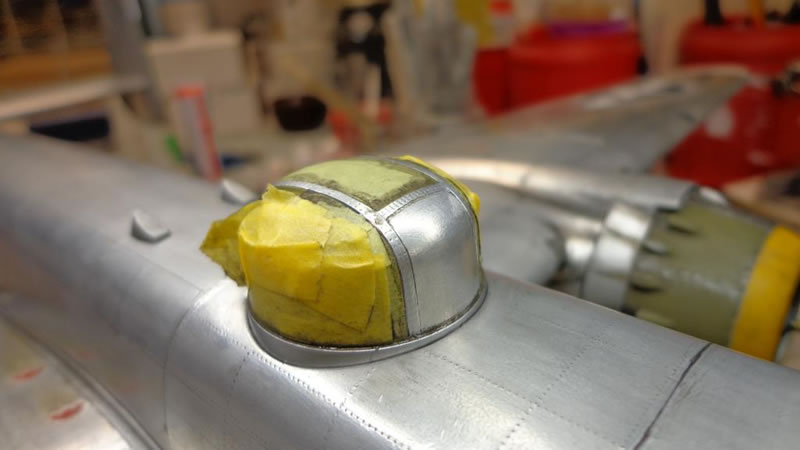
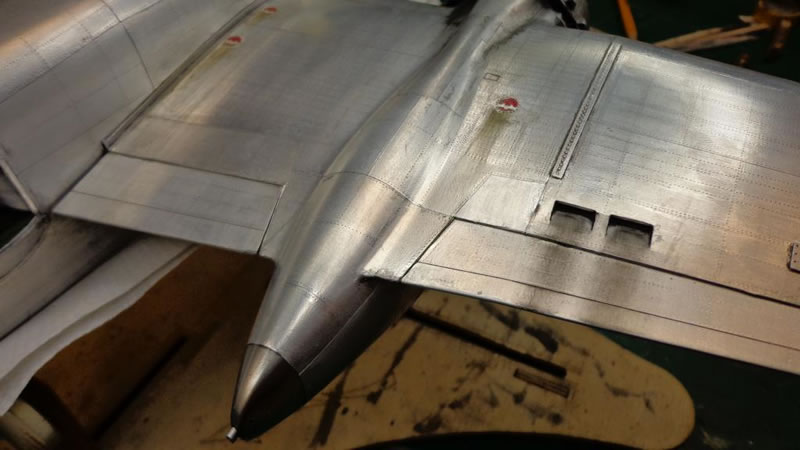
Finally I removed all of the Tamiya masking from the clear parts:
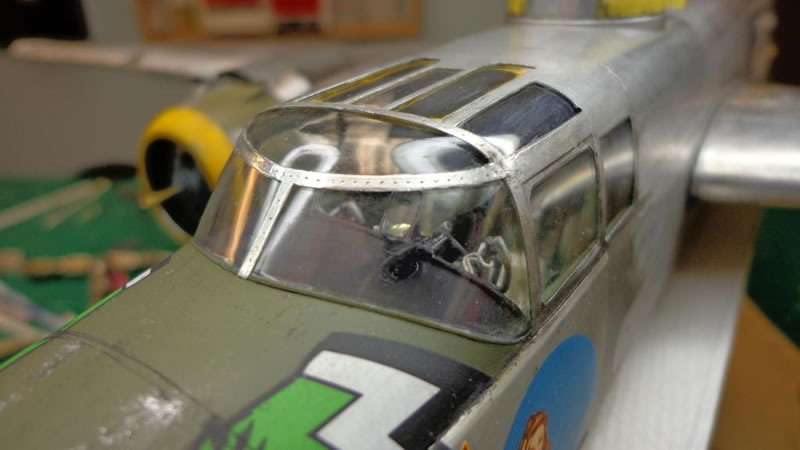
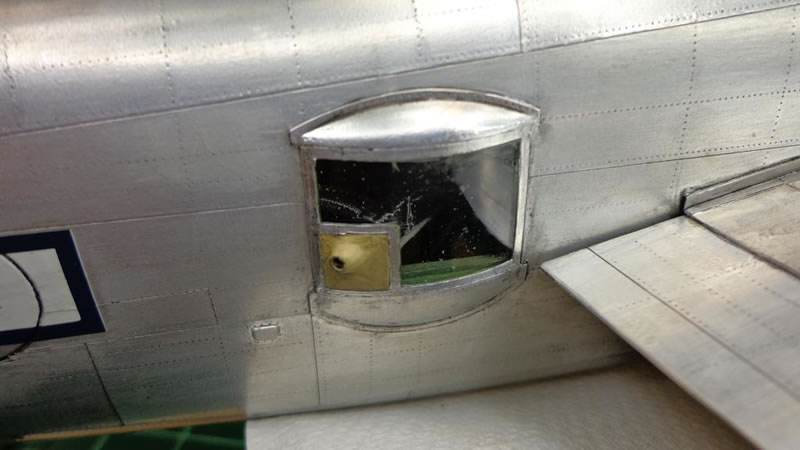
After the weathering was done it was down to the small details that may have gotten knocked off if added any sooner in the build. This included attaching the Brassin wheels using 15 min epoxy, and adding the bomb-bay doors, nose antenna using EZ Line, as well as the props and all 14 of the model master .50 cal barrels.
Here is the final finished product:
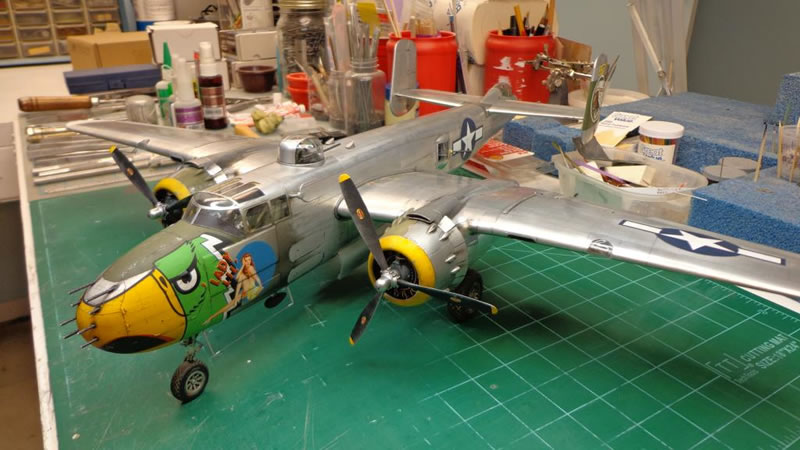
CONCLUSIONS
Although I chose to throw a lot of extra work at this kit as well as AM, none of it was truly necessary to make a really nice model. Things you may want to consider at a minimum changing or adding are:
- props/governors
- resin wheels
- AM decals
- G-Factor white brass gear
All of these things as I stated in my in-box review are minor, and you can get a really nice show stopper out of this kit even built OOB. Just take your time, as this kit is BIG, and has a lot of parts. Don’t rush things and build it the way you want, and you will have a definite winner on your hands.
This kit on the whole is quite spectacular, and goes together without a hitch, even for as large and complex as it is. There are some things HKM could have done differently to improve the kit, but NO kit is perfect and this one goes together, and looks about as good as you could ever hope for.
On a 1 – 10 scale w/ 10 being perfect and 1 being useless, I'd give the HKM B-25J a solid 8.5 on build-ability, and a solid 8.0 for overall accuracy and detail.
If you love (or even just like) the Mitchell you really cant go wrong building this kit. - HIGHLY recommended.
Thanks again to Ken Laurence at PCM for this review sample.
© Brian Leitch 2013
This review was published on Thursday, August 15 2013; Last modified on Monday, February 22 2016