Revell 1/32 P-47D Hub Zempke
By John Formon
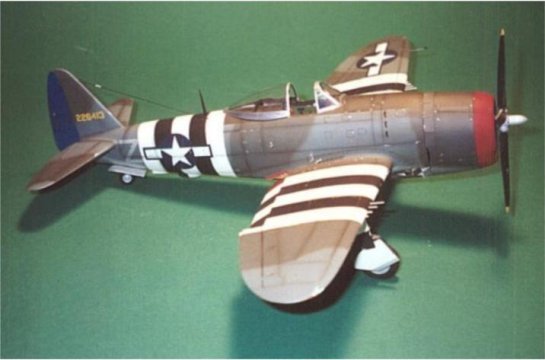
Here she is gang…… after a full years work…Revell's 1/32 P-47D in 56th FG colors circa June 5th 1944. This ship is "Oregon's Britannia / Happy Warrior" flown by Group Commander Col. Hub Zemke. I did a tremendous amount of research and actually talked to various members of the 56th FG in order to get the color scheme as accurate as possible…..and I am still not 100% sure it is correct (i.e. I have no conclusive photo evidence). The 2 areas of contention are the wrap around invasion stripes and the unpainted aluminum undersurfaces. I chose both…based on my references. I purchased this kit 10 years ago from AAA Hobby in Marietta Ga. (I think it was actually out of production even back then). I always planned on building into a museum piece. It was only last year that I got the inspiration to do so. The kit itself is pretty ruff. Nothing is useable except for the major components (wings, fuselage, stabilizers). But the basic outline of these parts compares well with scale drawings……so you will end up with a pretty good looking Jug. I even saved the cowl…and after some rework got it looking pretty accurate.
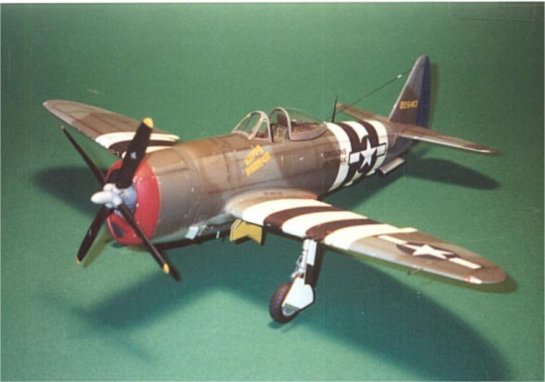
I scratched just about EVERYTHING on this bird. I am a real die hard. I like to feel it is a "one off" bird and when it goes to contests it will be all original. You could save yourself loads of time by using Jerry Rutman's excellent resin parts. The scratch built items are as follows; -Prop -PW 2800 engine -cowl flaps -complete interior (inst. panel, gun sight, stick, seat, side walls etc…etc….) -Landing gear and gear bays -Wheels and tires…including tail wheel. -All gear bay doors -Fowler style flaps -etc…. The key to scratchbuilding is to collect some good references and TAKE YOUR TIME! I cant tell you how many times I would scratch build a part and I would be unhappy with the results so I would make another…… It is something I learned from Rodney Williams. Remember, all of your parts won't be perfect, and you will have to try, try again.
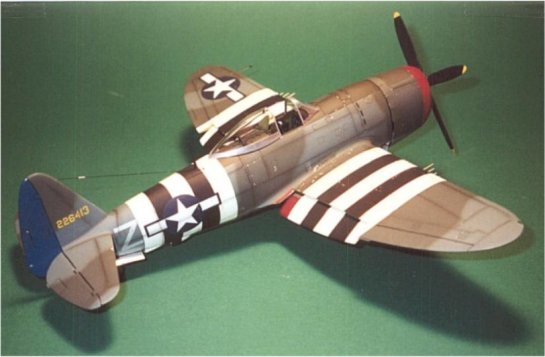
Here are some tips based on my P-47 experience… I spent a lot of time scratch building the PW 2800. Although I know it is "all in there" you can't see much of it from the front. Lesson…make a cowl panel removable…or spend less time scratchbuilding the back of the engine. Dropping the flaps was a hell of a lot of work. Since they are Fowler style (they drop down AND back) you have to scratch build the flap bay and reproduce the actuator arms…..then get it all to line up correctly. But…it sure does look good and I don't think you will see many 1/32 scale Jugs with the flaps dropped. Make sure the machine gun barrels are PARALLEL TO THE GROUND. They don't follow the dihedral of the wing (common mistake). When building the wings I "scabbed" in a good size piece of solid Evergreen styrene stock in the gun barrel area. This gave me an excellent mounting platform for my barrels. The barrels were then "scribed in" when the model was in its assembly jig (more to follow). The barrels themselves are S.S. tubing of appropriate size. Believe it or not…… I used the kit canopy. I fully expected to have to vacuum form a new one but after close study I simply reworked the kit part. All it takes is patience. File off the inside rail detail…then begin sanding both inside and out. Start with 400 grit, 600, 1000, 1500, then polish. THEN dip in Future. The canopy will really "pop". Ditto for the front windscreen. I scratch built the canopy latch mechanism. The canopy framing is buffed out lead tape with the rivet detail added with a needle. Cowl flaps are .005 Evergreen styrene sheet. Cowl was slightly reshaped with styrene and putty then rescribed. I don't know if it is perfect…..but it looks pretty good to me.
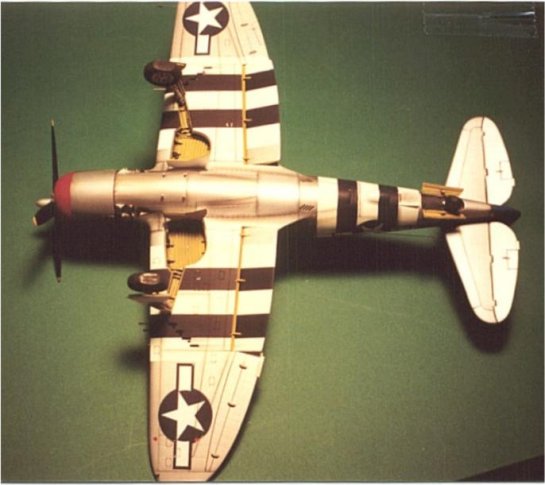
Underside of my Jug is aluminum finish. All of my references point to this. The underside is painted with Model Master Aluminum plate with some lacquer thinner added. I have found the lacquer thinner gives the paint more "bite". Then, some of the underside panels are covered with aluminum foil. I always wanted to try this technique and am quite happy with the outcome. The foil is a heavier gage than bare metal foil , and on 1/32 scale aircraft it just looks better in my opinion. ALL of the rivet detail and panel lines were sanded off. Then the airplane was rescribed using the needle and Dymo tape technique. All Dzus fasteners were added back with a pin vise. After close study of a real Jug I decided not to add back the rivet detail. The rivets were quite flush and well hidden. One thing I did notice however was the aircraft skin was "pulled down" to the internal stringers forming a very slight linear depression in the skin. (Look down the side of a riveted skin aircraft and you will see what I mean). I reproduced this by LIGHTLY scrapping this skin depression along all the rivet lines. BE CAREFUL. You want this to be very very subtle. If you over do it the airplane will look horrible. I erred on the side of too subtle and it came out just right. If you catch the skin in the right light and angle you can see this detail. It does make the skin look riveted on…way cool (it is hard to see in the photos).
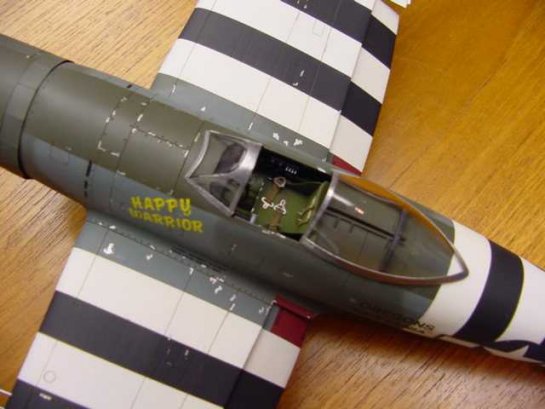
A big area that most of us modelers fall down on is alignment. We glue together all the major components, fill all the seams, put on a perfect paint job…then notice the wing dihedral is inconsistent or that the stabs are crooked or that the gear is misaligned…arrrrgh. Not me…not anymore. What I do now is for every model I build I build an appropriate assembly jig. During major component construction the ship goes "in the jigs" and all alignment and bonding gets done here.
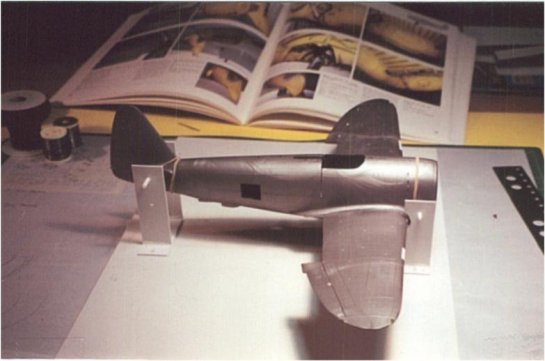
I began by drilling very accurate 1/8 inch holes in the front and back half of the fuselage. These holes then have 1/8 styrene rod placed through them. This rod then aligns the fuselage in the scratch built jig. These "construction holes" will get filled in later. The key is to use your common sense and ingenuity here. The jig does not have to be expensive…but it does have to be accurate. I learned this technique from the writings of Rodney Williams, George Lee and John Alcorn. Once this jig is built you will be amazed at how much you will use it. On this project I used it for the following: -Wing Alignment -Horizontal stab alignment -Dropped flap alignment -Dropped tail surface alignment -Machine gun barrel alignment -Landing gear alignment -Landing gear door alignment -Engine alignment -Prop alignment Let me tell you folks…… I never would have got this airplane "squared up and right" without the jig.
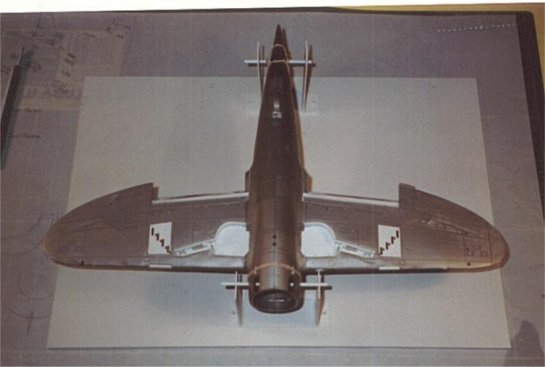
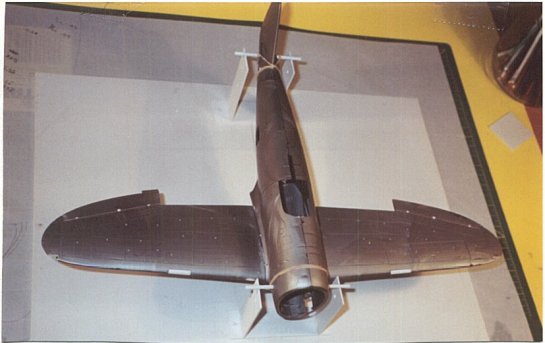
The aircraft wings were tied together at various locations along its chord with .025 styrene rod. Simply drill a hole through both sides of the wing…and insert the rod for strength. I use super thin super glue to secure the rods because it sands out so well. This technique will make your wings super stiff and strong. No more worries about popped wing seams. (ANOTHER Rodney Williams lesson…thx Rodney). Here is my painting/finishing technique… After the model is sanded, scribed, sanded, washed and ready for paint… Give the bird a few light coats of Future. I have found this blends the panel lines and fills any tiny surface blemishes. -Paint with Model Master Enamels. I love these paints. Don't care for Acrylics. -Overcoat with Model Master Clear Top Coat Gloss Enamel. I love this stuff. Let dry 3 days. -Add Decals. My Nat insignias were from the spares box. All other decals were hand made or painted. I love to use Letraset dry transfers on clear decal film. -Overcoat with Model Master Clear Gloss. Let dry 3 days. -Accent and weather all panel lines with Winsor Newton WATER COLORS. I love this technique. Your base coat is never in danger of being ruined. -Overcoat with a 50/50 mix of Testor Dullcote and Testor Metalizer sealer. I love this blend. Let dry 24 hours. -Final weather with pastels -Final overcoat with Dullcote / Sealer blend.
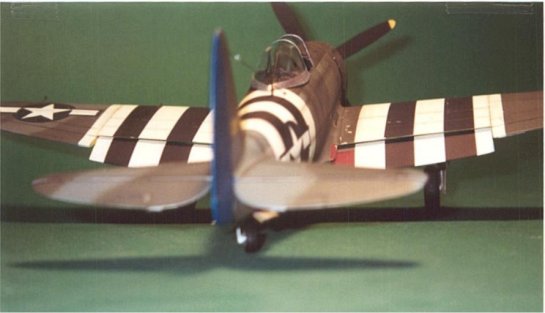
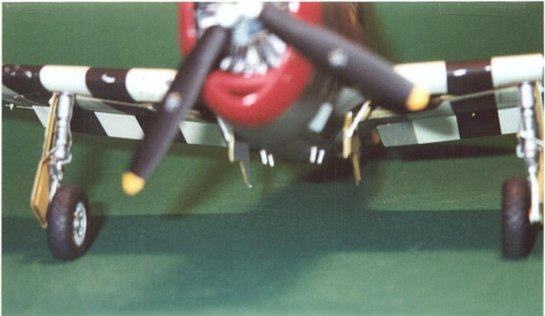
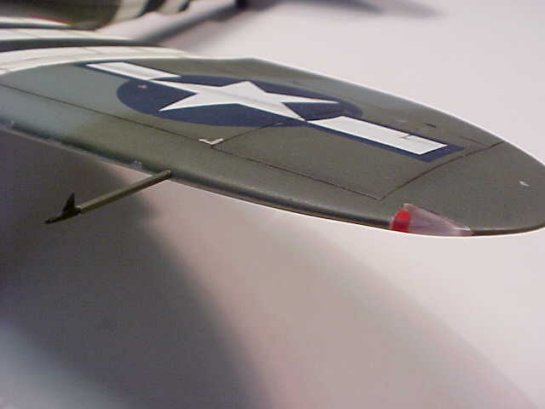
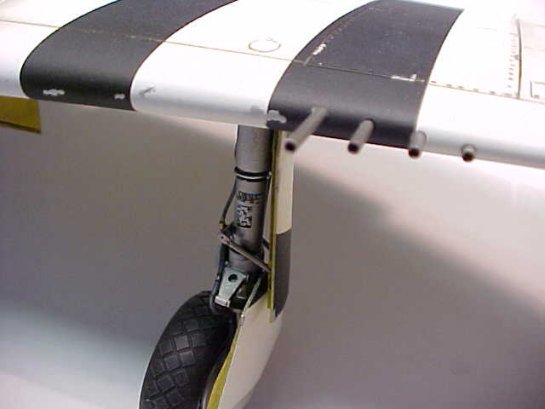
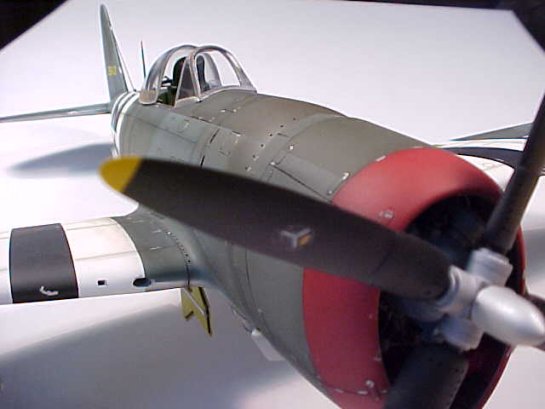
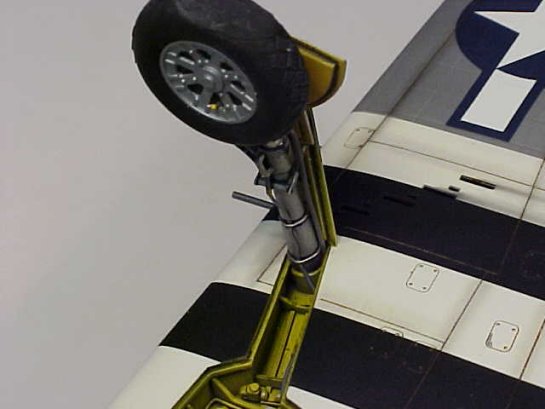
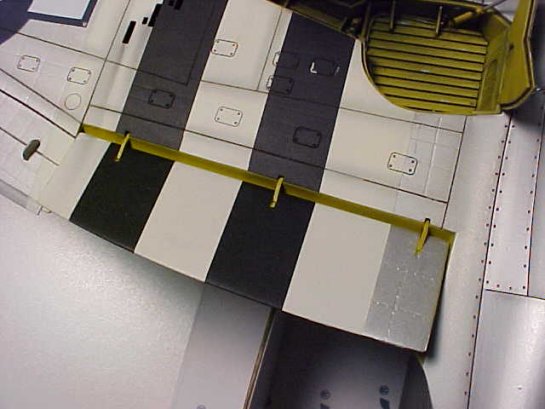
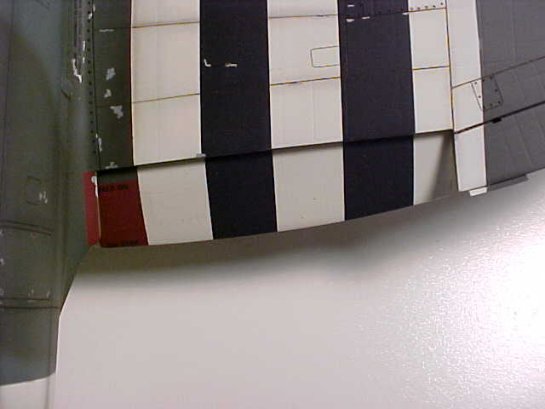
This baby was a lot of work…but well worth it and a lot of fun. I don't have above average modeling skills. Anyone can do this. It just takes INSPIRATION AND PERSPIRATION. Remember…if you count on having to do various steps "2 or 3 times until you get it right"…it wont be nearly as frustrating. Now where is that Razor back version hiding in my closet!
© John Formon
This article was published on Wednesday, July 20 2011; Last modified on Saturday, May 14 2016