My Tools
By Rodney Williams
Over the past couple of years, modelers around the globe ask about my tools... "WHAT KIND OF TOOLS DO YOU HAVE TO MAKE ALL THOSE HAND MADE SCRATCH BUILT PARTS?"
Sanding
Almost two decades ago when I painted my first model with "SnJ" Spray Metal Aluminum, I had many, many scratches showing through the "Bare Metal Aluminum" paint finish. I was told to go seek out finer sandpaper.
There's a auto parts store here in San Jose, CA USA; by the name of "COOK'S AUTOMOTIVE SUPPLY, INC." They specialize in auto paint supplies, including 3M fine sandpaper, and "Fine-Line" masking tape made by "3M." The sandpaper comes in the following grits: #500, #600, #800, #1000, #1200, #1500, & #2000. I was told to place my sandpaper in water and leave it there for 2-3 days before I use it. This softens the backing paper, which prevents it from cracking, when you wrap it around your home made sanding tools. I've found that by cutting my sandpaper into 1" to 2" squares, it works for most all applications. In the first photo, you will see that I have marked the backs of the paper. This tells me what grit it is; (EG: 8 equals 800 grit, 2 stands for 2000 grit).
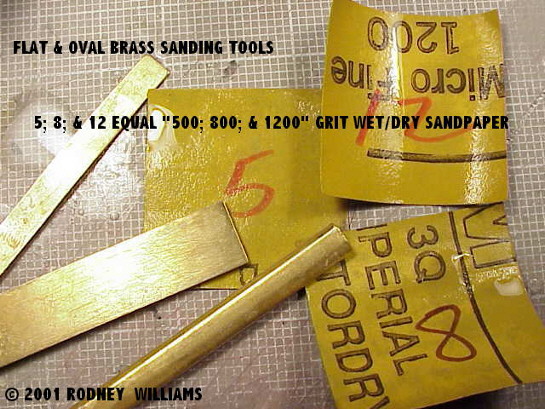
You should change your water EVERY TIME you change grits, bar none! This water change eliminates the possibility of any previous grit getting onto your next finer grit sandpaper, and making a big scratch in the plastic. As mentioned in my model stories, you must at all cost sand down to 2000 grit, if you are going to apply "SnJ" Aluminum Paint.
See my story on "How I Apply SnJ To My Models," on the SKYWRITERS web site at www.skywriters.net.
These "sanding sticks" are great tools! A few years ago, Dave Balderrama, who comes to my weekly "workshop" showed me several of them. Dave buy's them at "Sally's Beauty Supply" here in San Jose. I think they may be national chain store in the US I've found them at our local drugs stores, in the women's cosmetic department. Price ranges from .80¢ to a $1.25 each. They come in different grits, and different sizes. It's best to use them with water, and clean them frequently. Using a wooden handle brush. Brushes come in brass, stainless steel, and/or nylon fiber. I cut some of the sanding sticks into different pointed shapes.
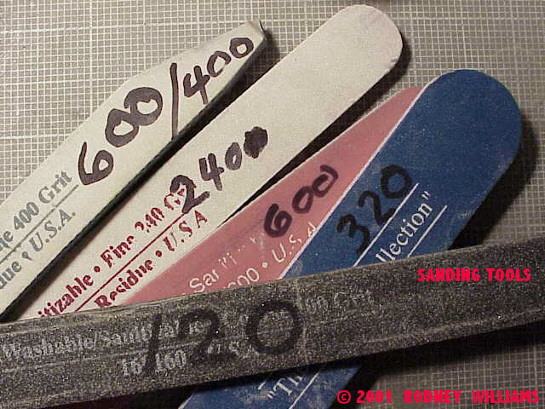
I got this bright idea one day! When the "sanding sticks" wear out, I clean off all the residue with water and a wire brush, and let them dry. I buy the standard 8-1/2" x 11" sheets of 3M wet/dry sandpaper for about a "dollar" per sheet. I lay the sheet of sandpaper "grit side" down on a smooth flat surface. I place the stick onto the paper backing, and draw on a pencil outline. I apply thin super glue in the center of the "penciled in" outline on the paper, and press down the sanding stick. I use one of my super glue wire applicators and add more super glue around the edges. Once dry, I trim off the sandpaper around the sanding stick. "PRESTO!!" I have a new sanding stick, at a fraction of the cost of the original sanding stick. You can get several new sanding stick from one sheet of sandpaper. I apply the grit number; ( EG: 320) on the new sandpaper. Go for it!
Applying Glue
Around 1985, another modeler made his own super glue applicators. Matt Matsushita used different diameters of brass and steel rods inserted into round wooden "Q-TIPS." He used modeling clay and made small depressions in the clay with the bottom ends of his "X-ACTO" knife handles. You can use other items to make smaller holes in the clay. Just apply the super glue into these depressions, dip in the applicators, then apply it to the area on your models. I assemble all my parts, using this method. On final assembly, I attach many parts using .004" & .006" diameter brass rods. With a bit of practice, you will be able to apply a tiny "micro-dot" of super glue to any location. The applicator will become clogged with the super glue. I use a cigarette lighter, and burn off the glue, then brush off the carbon residue with my wire brush. At times, I use a worn out #11 blade to scrape off the residue. Eventually, the ends of the small wires will "crystallize" and break off. Just cut the end off and bend the end into a "half moon" circle. Many modelers use this method! I got away from using "fillers," and use only super glue. When all the holes in the clay fill up with dried super glue, remove the dried glue, and roll the clay into a ball. Place the ball of clay onto the flat styrene, flatten it out, put in the new holes, and your ready to go!
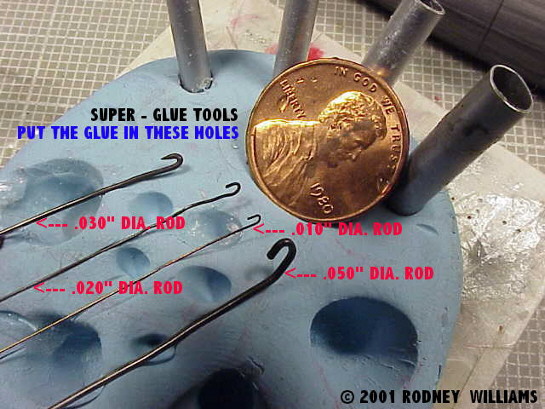
Scribing
This big "GREEN" plastic circle item is another tool I use!
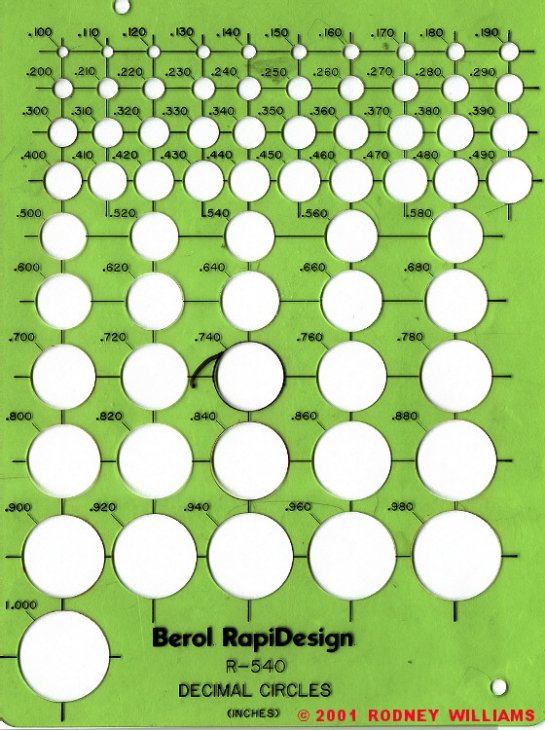
Here's my set of scribing templates made by Tri Tool, who I heard, went out of business. I understand that "Verlinden" makes some.
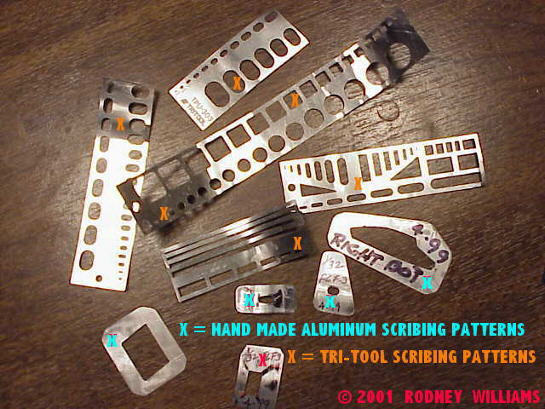
I started years ago making my own templates, using the .005" thick aluminum from soda pop/beer aluminum cans. "Here's several photos showing how I make them!"
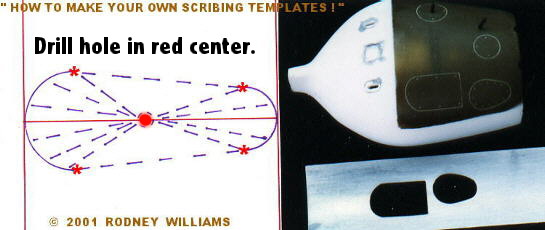
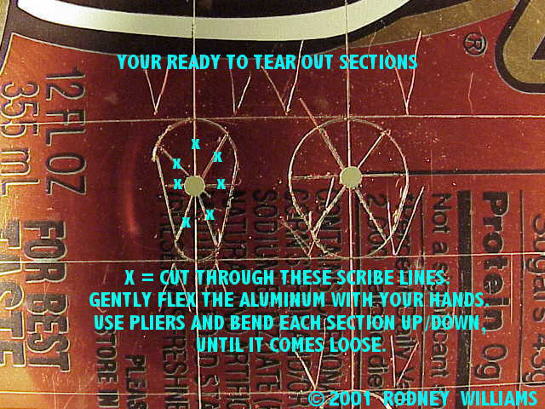
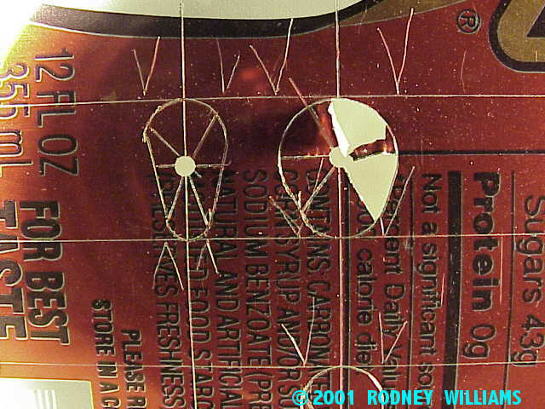
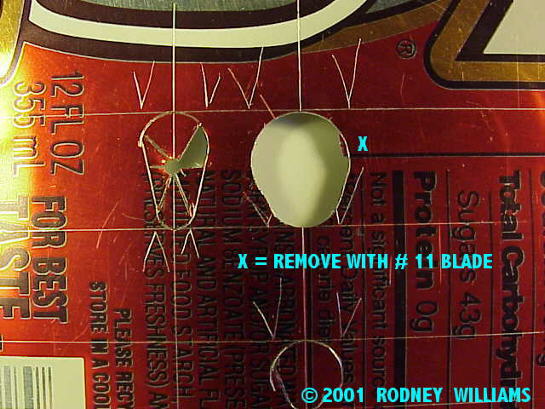
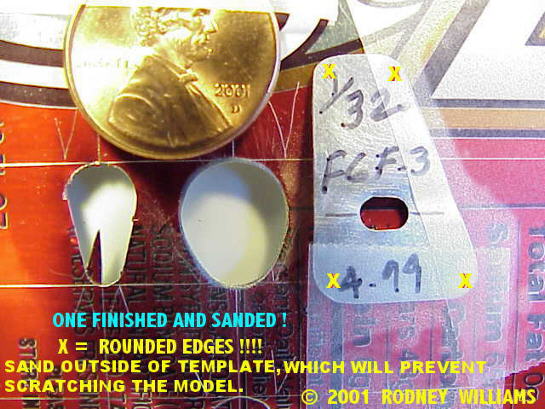
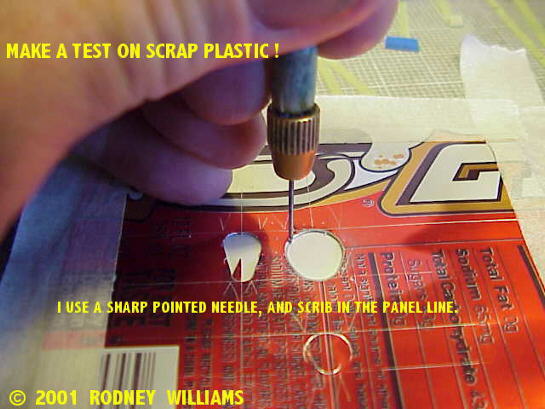
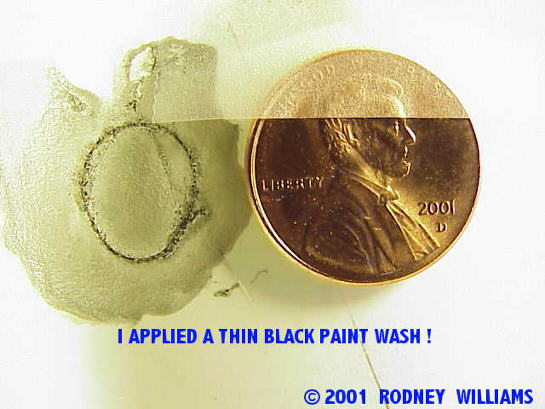
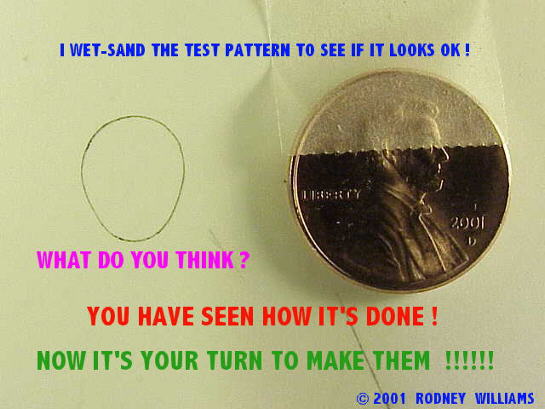
This photo shows the different masking tapes I use on my models. I need not explain how I mask off a model, for painting, and/or scribing in panel lines. You all know how to do it? RIGHT?
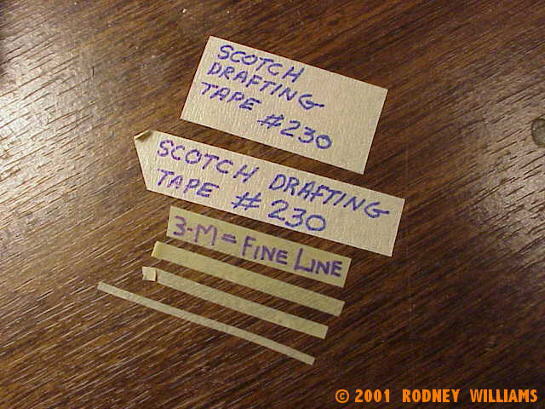
This photo showing the tail on my 1/72 scale B-58A Hustler shows how I apply the masking tape to it, so I can scribe in some missing panel lines, including the different scribing tools. I but the tape at the panel lines on both sides. Be sure to leave a tiny gap between the edges of the two strips of tape. This gives your scribing tool room to move, and peel out the plastic. If you don't leave room for the tool, you will have problems scribing.
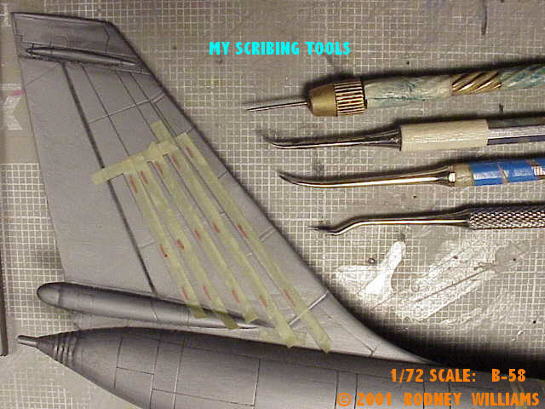
Cutting and Filing
A decade or more ago, Mark Ryan sent me one of these "Flex-I-files" I tried it. What a fantastic tool. I bought a whole bunch of them. I needed smaller widths. I laid the sanding strips, grit side down onto a flat surface, then placed my steel ruler on the strip and cut it, using a single edge razor blade. In those days, the owner "Fred" didn't make 600 grit. Well you know the outcome!!! I called Fred on the phone, and told him that if he wanted to capture the market for modelers, he has to make 600 grit. Not long after that, I got a hole bunch of 600 grit sanding strips from Fred. I let him know that this was: "What The Doctor Ordered," which is an American English expression. You can thank Mark Ryan for sending one to me, then thank me for letting Fred know about the 600 grit, then thank Fred for making them!
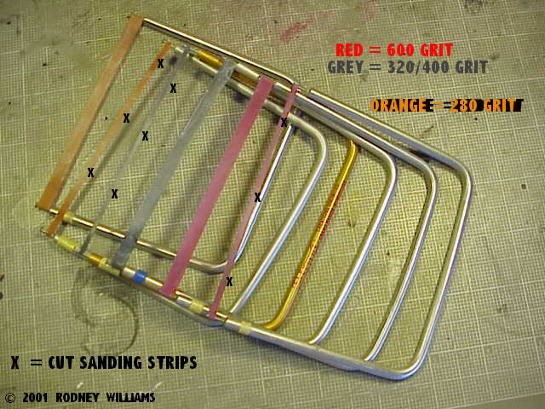
This photo shows all my Dremel Motor cutting tools. There's no explanation necessary!
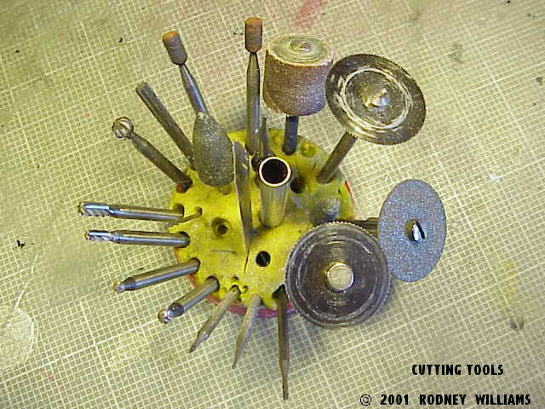
These photos show my file sets, which I bought from "Star Struck, Inc." www.starswtruck.com over a decade ago. The cost was around $65.00 to $75.00 US per set. Very expensive, but worth their weight in gold! Today some people say: "It's worth its' weight in Marijuana!!!" Gold sells for around $300.00 per ounce, while Marijuana sells for $400.00+ per ounce. They are called "jeweler's" files. There are 12 files in each set. You can buy the 4" & 6" long sets in number "four," and number "six" cuts. They are super fine, and will load up real fast with the material you are filling.
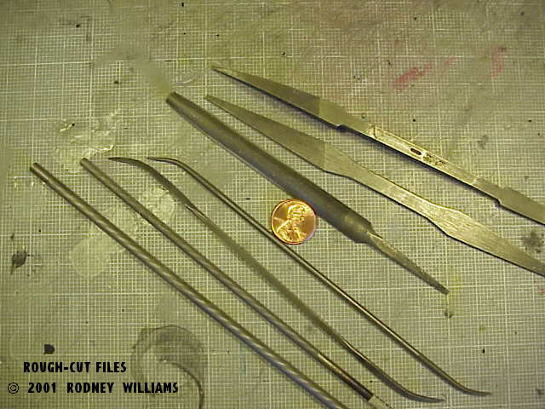
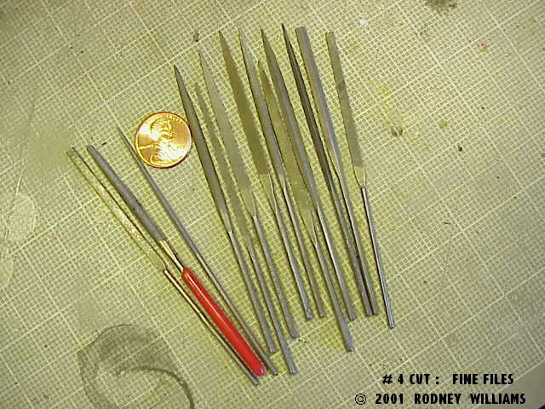

A "tip" from the master modeler.......me!" I use water with the files, when I file any type of plastic material. I use my household "3 - in - 1" oil when I file any material made of metal. I brush out the filings with my "brass" and/or stainless steel brushes. Sometimes I have to carefully pick out some of the filings with the point of my needle in my pin vise, and/or the point of a #11 X-ACTO BLADE. After any water application, you "must" dry the files, or they will start to rust. To remove the "3 - in - 1" oil from them so you can file plastic, use either mineral spirits, and/or lacquer thinner, then denatured alcohol.
This photo of my 1/72 F2G Corsair prop blade shows the end results, using the "Flex-I-Files" I used the 4" long #4 & #6 cut files. I'm certain I could not have achieved a near perfect finished prop and hub without these simple tools. I was able to save all the tiny molded in bolts on the hub.
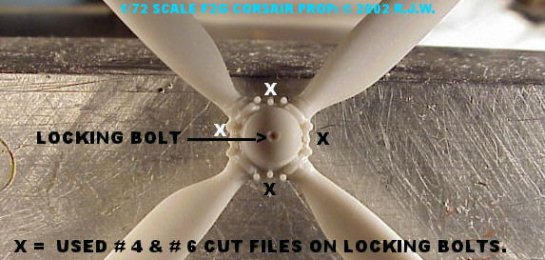
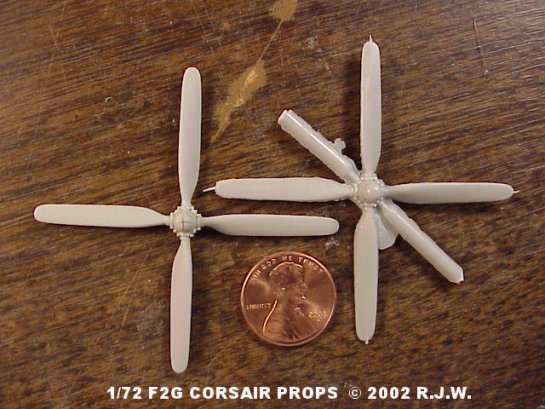
Drilling and Cutting
THE TINY DRILLS come from "SMALL PARTS, INC." ......... www.smallparts.com They are located in Miami Lakes, Florida USA They will send you a free catalogue! The drills are a must for me, and maybe for you. The tiny .006" to .012.5" diameters drills will break real easy. With experience, I very seldom break any of them now days. I use the "3 in 1 " oil when drilling into metal. I've never used anything when drilling into kit plastic or styrene. If you order these drill, get a half dozen each.........you will break some, that's for sure. I acquired the pin vises from "Micro Mart," but I have no address for them. They are located in the US
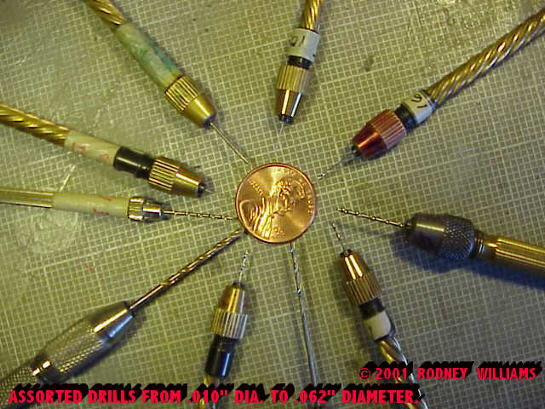
Look real close at the finished F2G prop hub(above). I drilled a .016" diameter hole into the hub, then I drilled a .010.5" diameter hole in the center of the .016" diameter hole, then inserted a round red .010" diameter rod to represent the locking bolt. Looks like the real thing!
My professional "circle" cutting tool is a must for cutting professional top quality circles. I use it for cutting out the round circles for American, British, and Japanese insignias. I bought it at a local drafting tool supply establishment. When making two identical parts, a "micrometer" is a must.
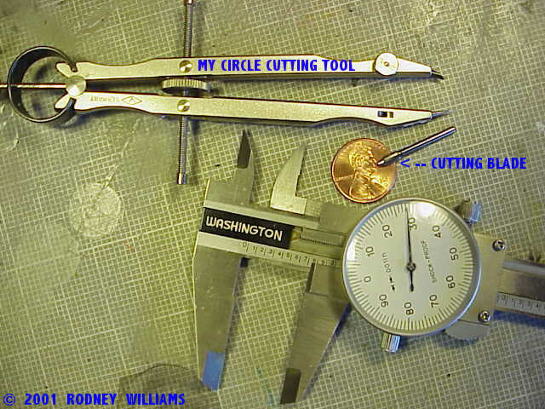
Here are some other tools, a jewelers cutting saw, a small tube cutter, which I got from Small Parts, Inc.
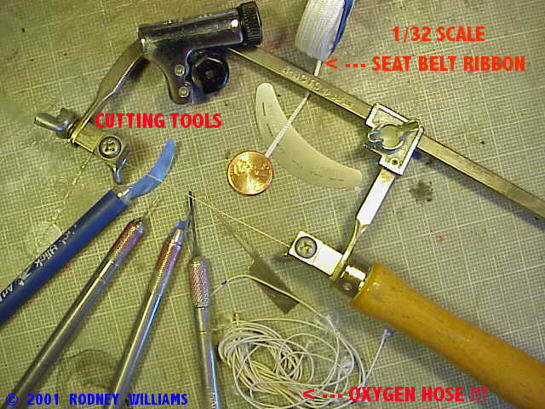
I love this small cordless Dremel motor tool! Next to it is my old but reliable 3/8" variable speed drill. It's used as a "hand held" drill press, etc. You just eyeball it while drilling a hole into something at a 90 degree angle.
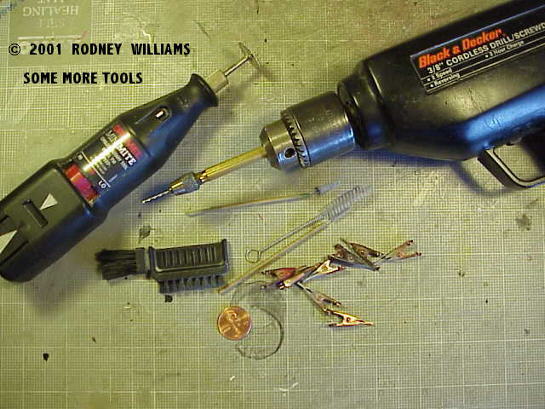
Punching
Both "Waldron Punch Sets" are a must for me. The attached photo diagram shows how not to destroy a punch set like I did.
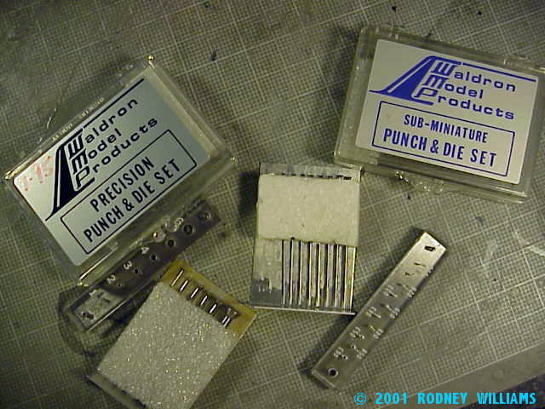
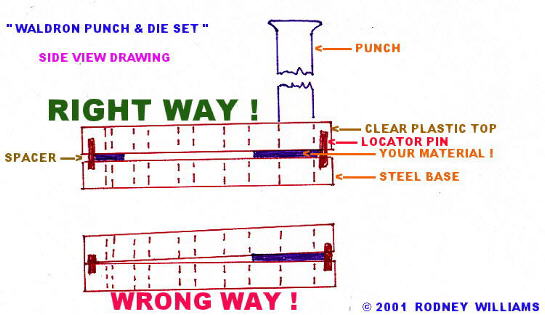
Vac-U-Forming
In 1984, while at a local model club meeting, a guy told me to make a box, with a perforated top, and a hole for my vacuum cleaner, "DA! DA! DA! Then he told me to buy some "bass wood" and carve out my "canopy/windscreen mold" for my 1/32 F2G Super Corsair. I went home from the meeting, and had no damn idea what he was talking about. Here is the end result. I've perfected the system since then. During the past ten years running my weekly "free" workshop, I have given several "demos" concerning making molds and doing the "vac-u-forming. "Nothing like seeing it done to believing how east it is to do."
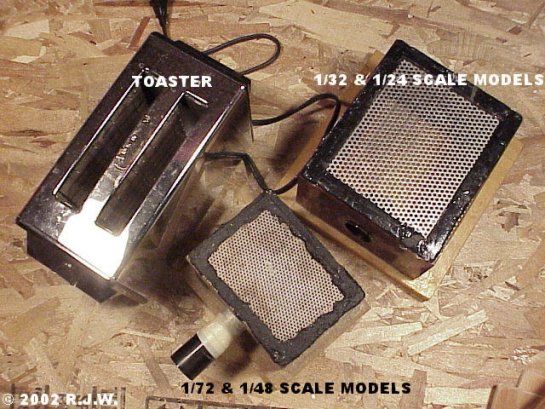
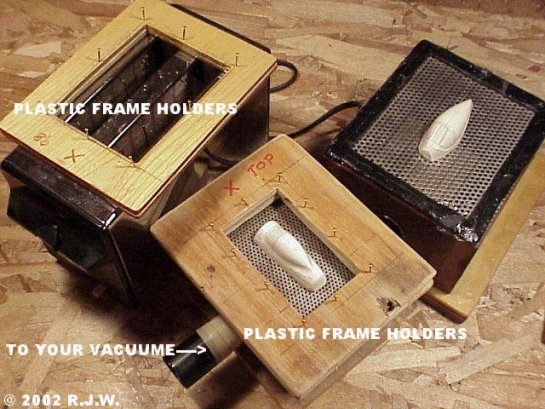
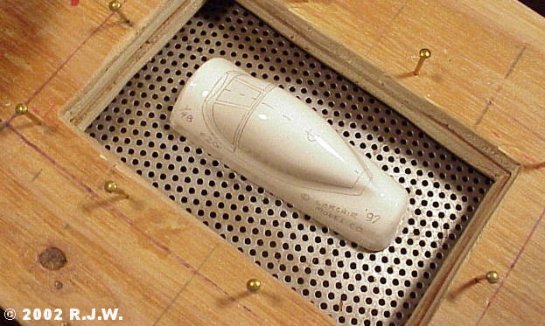
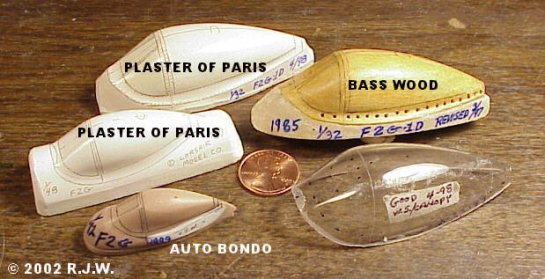
The Lair
This is my work station, where I pump out all these "hand made" model parts.
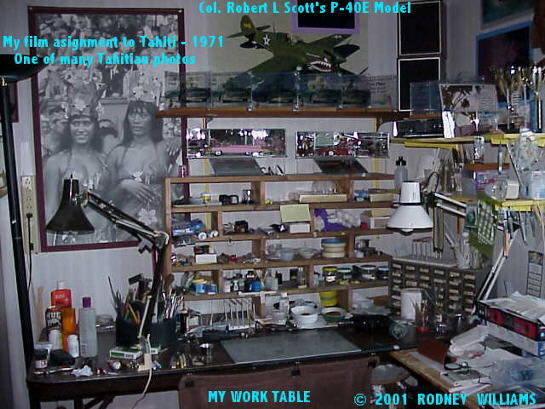
I hope this "tool story" helps you become a better model builder.
© Rodney Williams 2001
This article was published on Monday, November 02 2015; Last modified on Monday, November 02 2015