Metal Foil Tips and Tricks
By Mike McLeod
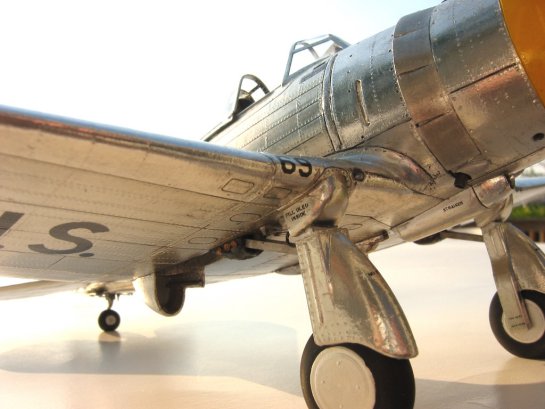
Instead of finishing a scale model with various types of "metalized" and silver paints in an effort to achieve the much sought after "Natural Metal Finish" (a.k.a. "NMF"), metal foil presents a unique and viable alternative. The following article outlines some of the methods and techniques I have come to find useful in recent months while researching this elusive, sometimes-difficult, finish. As with many modeling pursuits, there is probably much room to grow and expand upon these methods and each modeler may find variations on the theme to better suit their specific project or abilities. The basics outlined below should suffice to get any intermediate or above level modeler off to a good start on a foil-based NMF. As usual, practice will greatly improve results and use of alternative tools and methods may be required for the specific needs of a given project. While foil does have some superior characteristics to any form of paint medium in certain areas, it cannot be used in extremely irregular and high relief applications. For these cases, using a mixed-media approach is recommended to appropriately blend the finishes of foil with paints. In my experiences, one of the most resilient NMF finishes achieved by paint is from ALCLAD II applied over an appropriate base coat primer.
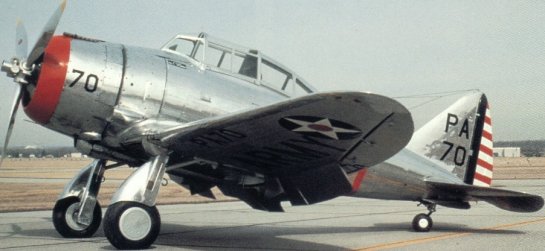
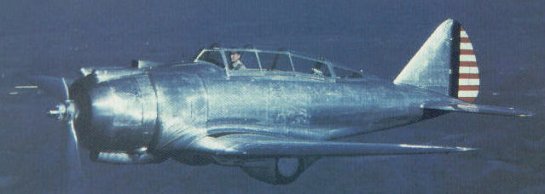
TOOLS - THE BASIC STUFF
Let's begin by reviewing some of the tools required to accomplish a metal foil finished NMF model. Most of these tools are basic and easily obtained. A few others are in the specialty category and may take a bit of research to find in certain areas, although with today's Internet capabilities this should not pose a major problem for most modelers. Scribers come in various designs and each person seems to have a favorite. I have found the different designs to come in handy at different times depending on the application. I use both the "chisel tip" and "pointed tip" commercial scribing tools in addition to a homemade needle-in-a-dowel. Another indispensable scribing tool is the back edge of the tip on my X-acto blades and scalpel blades. The X-acto's are a bit more heavy duty and rigid while the scalpels allow very fine and deep scraping of material. In the end, I use eight different tools when scribing. Next up are the pounce wheels. These may be tricky to find but are really required. One problem with them is that each tooth on the wheel is actually like a small slotted screwdriver when examined closely. They will not properly make a round "rivet" in the plastic and must be reworked. I used my Dremel tool to carefully regrind each wheel to make the teeth into points vice little wedges. Also, you may have to gently crimp the fork holding the wheel to ensure it is tight enough to not wobble, but not so tight as to prevent rolling freely. The wheel is apparently high in iron content and will rust / corrode if not given a light shot of anti-corrosion compound. For the various access panels and hatches, not to mention connections and variations of panel lines, a set of scribing templates is a must. I have a set, which was purchased on the Internet from Verlinden, and they have served me well.
The last tool, and probably the most critical in foil application, is a set of burnishing sticks. When applying the foil, it must be worked and burnished into the surface gradually to allow it to actually bend, stretch, and form along contours without tearing. This is done with wood sticks as metal is too harsh. A small diameter acrylic or soft plastic stick may work as well on heavier thickness foil like that used on radio control aircraft, but I have been using wood as it is a bit more gentle on the foil. The primary stick is an ordinary round (not square or flat) toothpick. Sand one end to a round tip and the other to a soft edged chisel (no sharp corners or edges that will tear the foil). Another stick is a ¼-inch square medium balsa stick, again shaped with a round and chisel end. Occasionally I find use for one of my blending stumps. These are the tightly rolled gray paper sticks with a pointy tip used in blending charcoal, pencil, and pastel drawings. Like the balsa stick they will become fuzzed up and worn with use but are easily returned to shape with a coarse emery board. Finally, a small piece from an old, soft cotton tee shirt for buffing up patches of foil as desired. I have a bit of metal polish on the rag, not much though, which helps remove any worked-in surface scratches you don't want after the foil is down.
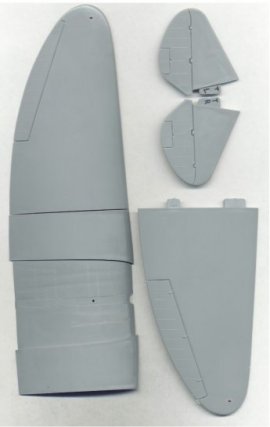
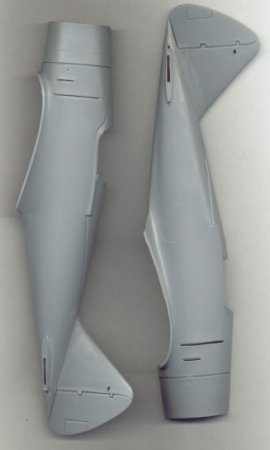
SURFACE PREPARATION
The basis of a correct and accurate model is your documentation. Gather up the source material you need and study it well. Use this information to plan ahead for all the surface details you desire to apply. Where needed, you may have to make sketches and diagrams to plan the scribing and rivet job. A useful method is to lay the model parts directly on a home scanner and make prints from them. These prints will be exactly 1:1 and can be drawn upon with pencil to plan out the panel lines and rivet details. To avoid clutter a scheme can be developed, for example, whereby panel lines are thin pencil, single rivet lines are dashed lines, double rivet lines are dash-dot-dash lines, and if rivets are staggered a crossed hatch on every other dash, et cetra. Be inventive and have fun with it!
Because of the way the surface details must be developed, an order of detailing is required. First the surfaces must be marked correctly. Use an erasable soft mechanical pencil rather than an indelible or water color marker, which will clutter up the area. When all the panel lines are marked and the underlying structure of the real machine is apparent, mark location of all hatches and access panels and erase where panel lines cross them. After all panel lines and hatches / access panels are set into the surface, rivets will be applied. It is important to have accurate panel definition so the rivet orientations will be correct and places where rivets run along underlying structure with no adjacent surface panel line will be in the right spot. When planning rivet runs care must be taken to allow for the spacing of multiple rows of rivets between panel lines or along the edges of a panel line. Likewise, rows of multiple rivets must be planned according to their spacing as even "side-by-side" or staggered in a "zigzag" pattern.
Once the panels and rivets are defined and applied additional surface work may be called for. Specifically, the dents and dimples that often appear along riveted metal. As the thin aluminum skin metal is riveted down it will sometimes pucker and leave ripples and surface undulations, which add a lot of character to the model. These surface anomalies are applied last and will destroy some rivets however, replacing the rivets is easy. Lastly, make sure all the panel lines and rivet runs cross glue seams smoothly and accurately.
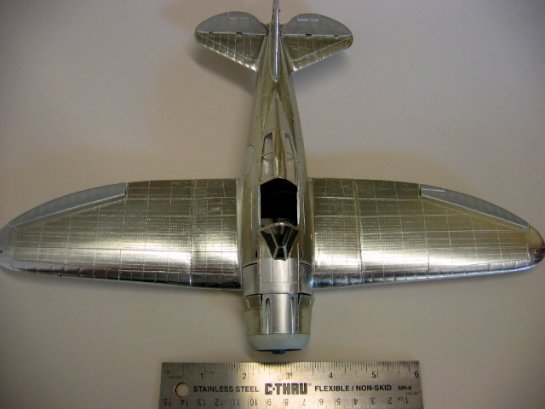
DETAIL APPLICATION
Before any foil job may begin, a thorough preparation of the surface is mandatory. Once all the surface details are identified and studied, the model parts can be marked using a soft lead mechanical pencil to allow accuracy, detail, and erasability for the goofs that will occur. Marking, scribing, and riveting should be done to the maximum extent possible on all parts before assembly due to the rough handling they will receive. If the model has raised panel lines, they must be sanded smooth first, or scribed along the raised lines to establish the recessed panel line before sanding off the raised part. Carefully mark all the panel lines per the documentation, then mark all hatches and access panels that break a continuous panel line. This will prevent you from scribing a line "through" a panel or hatch. To scribe in the panel lines, use a piece of DYMO brand label tape cut in half-lengthwise. This will lay flat and steady on the part and act as a straightedge. In cases of slightly curved panel lines, the DYMO tape may be cut more narrow and "bent" as it is laid down or cut at a gentle curve to match the desired contour. Don't try to over use the tape as it will loose its stickiness and may slip as the scribing tool runs along the edge. Stop panel lines short of hatches and access panels and use scribing templates to make these. Of critical importance is that you do not run the scribes lines all the way to the edge of any parts where a glue seam will be. It will be impossible to accurately scribe two parts and have the lines "meet" at the seam. Leave some room and the lines will be "connected" after the parts are glued together and the seam is cleaned up.
After the panel lines and hatches are established the rivet runs will be applied. For this I recommend the pounce wheel to ensure linear rivet runs and consistent spacing. In some tight spaces or awkward angles the pounce wheel may not fit and the rivets will have to be applied manually. For this I simply use my pin stick and work carefully for the few that must be made. As in the case of panel lines, use DYMO tape to mark the line where a run of rivets will lie. Place the teeth of the pounce wheel into the edge of the tape at a slightly inclined angle of 70 degrees or so to allow the teeth to track along the edge of the tape and not "wander" away. Use a gentle downward pressure and a somewhat "rocking" motion to advance the pounce wheel forward and backward along the tapeline. Making the sawing motion allows you to control a correct level of pressure and achieve a uniform row of "rivets". The rivets will in actuality be little "craters" or "volcanoes" on the surface that appear as a hole. While you will see the hole, you won't necessarily notice the raised "rim" of the crater. Once the foil goes over this, the hole will be invisible and the rim will define a microscopic rivet! Cool! Use care not to overly handle and smash down these bumps for the remainder of construction or you will be loosing your rivet detail.
One important note is that rivet lines may not be a single row but may be double or more adjacent rows. Also, the rivets in adjacent rows may be evenly aligned side-by-side or staggered zigzag along the rivet run. To do this you must mark one tooth of the pounce wheel with a permanent marker and use this "index tooth" as the starting point on multi-row runs. (Note: this indexing is also important for ALL rivet runs so that you can run over the line again and not have the pounce wheel create a "shadow" set of rivets next to the originals!) This is required since the tooth spacing on a pounce wheel is NOT even and varies slightly around the circumference of the wheel. When beginning a run, start at the edge with the indexed tooth. For the adjacent even row re-apply the tape in a parallel line but moved over approximately half to one millimeter. Now place the indexed tooth in the first hole of the existing rivet line and gently move it sideways to touch the DYMO tape and gently press it down to grab the surface. Then make the rivet line with the rocking back and forth motion along the length of the tapeline as far as needed. To make a staggered line, find the first rivet with the indexed tooth and move it half way to the second hole, then slide it over to touch the tape. It is now aligned to that each tooth will be pressing into the plastic half way between adjacent rivet holes. These technique takes a little practice to master, but will provide consistent and accurate rivet lines.
Many aircraft, which have riveted skins also, suffer from a slight buckling and wrinkling of the skin in the vicinity of some rivet lines. This subtle variation is sometimes random, sometimes consistent, and must be evaluated based upon your documentation. Since these variations are not molded into the model you must apply them yourself in the appropriate locations. To do so you must complete all the panel lines and hatches, and establish as many of the rivet runs as possible. Using a #15 scalpel blade scrape along the length of a rivet line where needed to remove some plastic and make a bit of a shallow trench on the surface. Next use 600 and 1500 grit sandpaper wrapped on a stick, or carefully with your fingernail, to sand across and along the trench to smooth the edges and make it blend into the surrounding surface. Use care to work small areas and not destroy too many nearby rivets. Keep in mind that ANY scratches from the scalpel blade or sanding marks will show through the foil and work to make the dent/dimple a smoothly flowed "surface defect". After completing the dents and dimples, you will need to go back and re-establish the rivets scraped and sanded away. This is where having the indexed tooth is very important! Start at the beginning of the run with the indexed tooth or you will have a set of rivets which "walk over" the original set. If in doubt of the correct spacing, gently roll the pounce wheel over the rivets and see if the teeth cleanly engage each hole or begin to run up onto the local surface and get "out of sync". Again, a little practice on scrap stock will go a long way in perfecting this technique. This can be next to impossible on white plastic! Good quality medium gray seems to be just about right for this step.
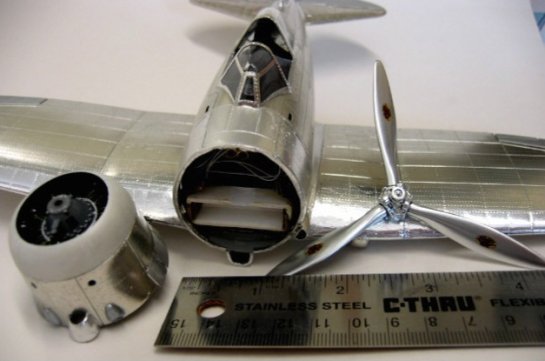
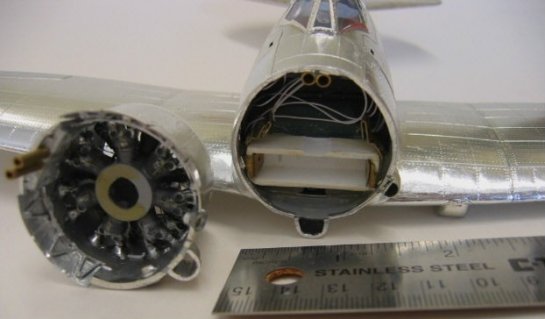
FOIL APPLICATION
Depending on your model subject, you may find a need for using multiple grades of foil. Not only does it come in shades and sheens of aluminum, but in gold and copper too. One of the neat subtleties of the foil is the way in which the different grades take on different hues. While all looking like "silver metal", the ultra-chrome has a blue tone, the chrome a sandy tone, and the matte aluminum a white tone. This variation will give you additional flexibility in replicating natural metal finishes. The chrome and ultra-chrome are very thin, soft, pliable and show all details very well. The matte-aluminum is a bit less soft and feels somewhat stiffer. When peeling from the backing, use care to not just pull it away and have it roll up into itself! It's impossible to unstick sometimes. Gently lift a corner or edge and while keeping slight tension on the foil with your tweezers, pull up and away from the backing so that the foil and the backing sheet form an angle of approximately 10 to 20 degrees. Keep the foil as straight as possible and bend the backing down and away from the foil but stop just before the foil will separate from the backing. Then grasp the foil and the backing where they still make contact and gently pull the foil as you "roll" your finger tips to the edge and let the backing paper separate until it only contacts the foil over a few square millimeters. All this time the foil has remained essentially flat and straight. Now, as the backing is allowed to fall away, a tiny bit of curling may occur along a millimeter or two of the edge, but the rest of the sheet is straight and ready for use. This technique is also very useful when pulling off a long thin strip of foil to avoid curling. Plan ahead and use the grades and finishes desired while starting from the lower aft part of the model and working your way up and forward. Covering small separate pieces will help refine your technique before tackling major assemblies. If you goof, don't worry! Just peel it off right away and do it again. The Bare Metal Foil will come off easily unless it has "set" for too long. After it is "set", peeling it off is very difficult as it will break up and you will find yourself picking at thousands of stuck down foil chips on a sticky surface...not fun.
In general, the foil is soft and will hug amazingly well on convex or concave surfaces. It appears that if the foil won't hack the curve on the model, aluminum sheet didn't hack the curve on the real plane either and there will be a seam or panel line present to offer relief. I guess things just have a way of working out. To apply a piece, carefully set the foil over the area (trimmed so as not to waste too much material!) and orient it. Beginning in the middle of the area, start making a circular, swirling pattern with the rounded end of the toothpick just enough to tack the foil down and flatten out an area about 3 mm across. Check that the foil will make it to all the edges desired. If not, gently peel up and re-orient or get a new piece and start again. Now start working it down by continuing to make circular swirling patterns while gently pressing the foil into the surface. You will notice right away how the foil is soft and begins to distort. Make the progress slow and allow the foil to bend and adapt to the curves as you go and work to advance the line of contact between the foil and plastic. On very aggressive contours, you may have to make a relief cut to allow the foil to warp into shape, just use care not to cut too far into the part of the foil which will remain on the model. Once laid down, you may want to use the chisel end to run it up to a corner or work it into a panel line. Trim it along the panel line with a gentle cut from the tip of a NEW scalpel blade, or in a pinch use an X-acto blade. Don't press too hard, and don't stretch blade use too far or you may snag the foil and get a tear. Peel up the excess, then buff the panel with the cloth. Sometimes a tiny wrinkle may form as you go, just try to burnish a little harder and work "along the contact line" carefully. Minor wrinkles may be eliminated by aggressive burnishing using the round end of the toothpick. This is okay, but on the matte-aluminum foil aggressive burnishing will cause the foil to lose its rough surface and shine up, looking like chrome foil...which may be desired in some cases if controlled.
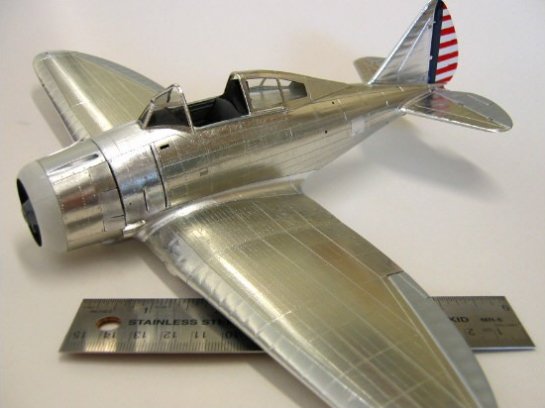
While foiling, be extra cautious about keeping the area clean and free of dust. You don't want a fan blowing or any other activity in the area. The most tiny, almost microscopic speck of dust or hair under the foil will show up with unbelievable clarity. Wiping the working area to be covered and your hands periodically with a tack rag is a good idea.
Certain areas need care when applying the foil. In particular sharp turns like trailing edges are susceptible to being peeled up until they are fully "set". When covering these, do the bottom first and burnish the foil up from the lower surface and trim it so the edge of the foil is 90 percent around the curve to the top surface. A firm burnishing from the edge towards the center of the upper surface with the balsa stick will press the edge down well and not leave any ridge to show through on the upper surface foil. Then, when covering the upper surface, wrap it around 90 percent to the bottom edge to ensure overlap and give it a firm balsa burninshing. Use care throughout the remainder of construction not to rake any tools or fingers across the trailing edges in such a way that it will peel up the foil. After some set time and the clear coat protection, there won't be any problems with peeling. On very large surfaces covered in one piece, a small bubble may appear where the foil was firmly attached earlier. Just re-burnish with the balsa stick. This may happen in the same spot several times, in which case you may want to gently pin prick the bubble to let air escape and burnish down.
Covering a canopy frame is easily done. Prepare the canopy by filing and sanding so it will fit on the model like a glove, since you don't want to be doing any more sanding or filling than required after it is attached. Do the Future dip routine and let it cure for a few days. Along the inner frames use the needle stick to press in the required rivets using gentle pressure while "rolling" the stick in a circular motion such that the end opposite the pin makes a small circle with the pin pressing on the plastic. This will make a small "crater" on the inside of the clear plastic canopy. And yes, be careful on the edges because WHEN the needle slips it does not slow down very much while it bores through your fingertip (trust me on this one...). Cut thin strips of foil the width of the frames and place them on the inside of the canopy. Use wider strips to cover the inner edges where the canopy will be glued and trim them to the edge. Keep all the strips correctly oriented, gently burnish them down and avoid scratching the interior of the canopy. Check the fit and trim away the foil where contact is made with the fuselage. Now go to the outside of the canopy and make a matching rivet on the outer surface, opposite to each of the inner surface rivets. Attach the canopy with a minimum amount of cement (a Touch-n-Flow is great for this part) and clean up the joint. Do not cover the outside of the canopy until you get to that part when covering the fuselage. When complete, the canopy will look like tiny plates of Plexiglas sandwiched into a riveted metal frame.
WEATHERING AND PAINTING
Once all your foil is burnished down and firmly attached its time to begin the weathering. While some subjects may call for the clinically sterile, just rolled out the factory door look, aircraft used in operational flying seldom kept up appearances for long. Some examples were well maintained, such as a Commanding Officers plane, but some normal wear and tear is always present. Applying such weathering and selective discoloring is a tricky task at best and can easily be overdone. On a NMF job it takes a different approach to get the "used machine" look. While painted surfaces can be worked with many forms of dry brushing, pastels, washes, and off-toned scale effect paint, the foil surface lends itself to a form of "physical weathering" which paint cannot withstand. Look closely at a vintage or WW II NMF subject and you will notice thousands of micro-scratches and areas of dull metal where people worked or walked. On some of the aircraft extremities the finish is quite a bit nicer as not much activity occurred out there, such as on the wing tips or the tip of the vertical fin. Thus a primary method of weathering a foil job is to selectively apply micro-scratches and dull the finish where appropriate. Normal oil and exhaust staining and washes can be applies also, but these should be left until the surface physical weathering is complete and sealed.
So, how should we scratch the surface? Do not use regular sandpaper! The foil is tissue thin and normal sandpaper will instantly tear through it. A better method us to use tiny square or oval pieces of 1500 grit paper about 3 mm by 5 mm. Glue the tiny patch of 1500 grit on the end of a thin wood stick with a slightly rounded end, and use it where needed. The technique I prefer is to gently twist and roll the end of the stick around an area in a PLANNED fashion. This is so you can put the micro-scratches in the proper area and make them look random at the same time. Work slowly and hold the stick at various angles as you use it. Periodically stop and examine the area by rotating the model around so you will see the multitude of scratches from many angles. The goal here is to work the scratches in inconsistent directions so they emulate the look of random scuffing.
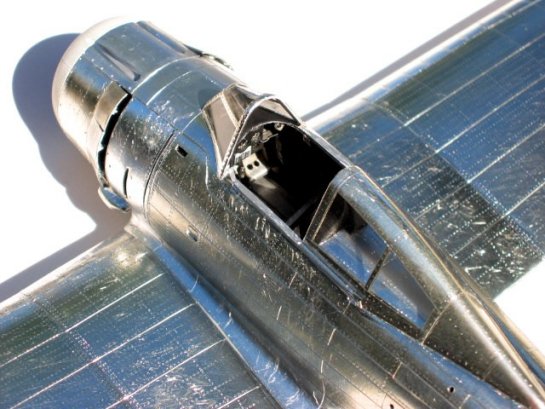
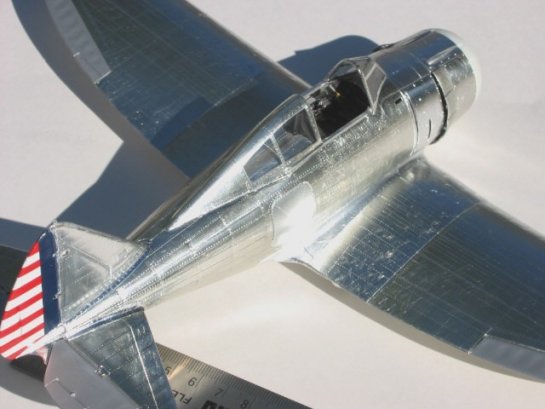
Another weathering technique involves making a specific panel, or an area, more dull than other local metal, without exactly looking like the matte-aluminum. Again, sandpaper won't serve this task well, not even the 1500 grit, just too abrasive. The choice of material for this application is a small trimmed square of green Scotch-Brite pad. The Scotch-Brite offers enough abrasion to gently get into the surface without tearing through. To use this type of dulling it is recommended that the area to be worked be masked off with a very low tack tape. Using the Scotch-Brite, and very gently pressure, make circular swirling motions and gradually take the shine off the foil and achieve a uniform dullness. In certain applications it may be desirable to make the strokes in a consistent, unidirectional pattern. This will give the look of brushed metal. Varying the direction of strokes on adjacent panels will give them different reflective characteristics in almost any lighting situation. Again, let your documentation guide you and work slowly since you can add a few strokes if needed, but unscratching the foil is not too easy.
After panels have been dulled with the Scotch-Brite pad the surface is very rough compared to plain foil and will take pastels, washes, et cetra quite readily. The good part here is that if you make a mistake, just swipe it with a cloth and it all comes off. Using pastels or washes can really impart some color to the finish and add depth, however you must plan to make these additions one of the last weathering steps and not handle the model too much. Since these are easy to take off, and the fact that the foil itself is a rather soft material susceptible to additional unwanted scratches, the surface must be sealed and protected. My tests showed that properly cleaned foil would take most paints very well. I chose to use Tamiya X-22 clear acrylic since it is ultra clear and flows on very smoothly with little chance of any yellowing like clear enamel. I refer to X-22 as "ultra-pure-filtered-Future", because that is how it seems to behave and it looks less cloudy. Once you are happy with the finish and weathering, just shoot a light coat of clear over the entire model (masked windows) and the surface is "locked in".
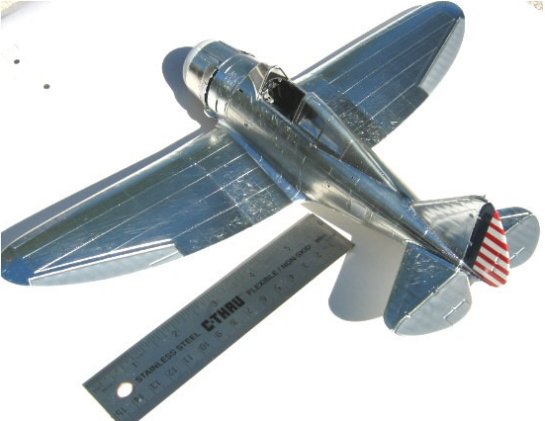
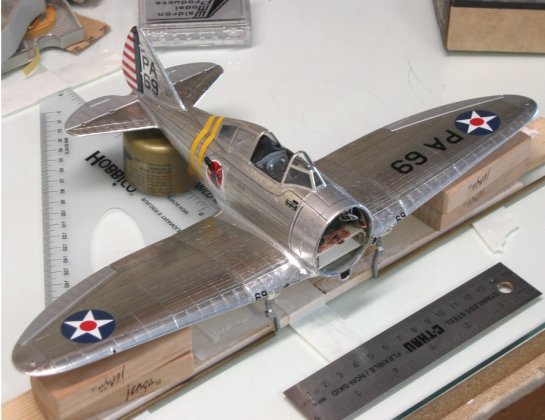
There may be a need to paint over the final finishes and this can be done safely is care is used. Applying masking tape over any foil creates a risk of lifting the foil with the tape. As stated earlier, the longer the foil sets the stronger its bond, but the risk is still there. The best approach is to use a very low tack type tape. The difficult part involved here is that you will not be able to trim the tape while it is on the surface or you will score into the foil. If this happens you are almost guaranteed to pull off the foil. Any masking to be done must be planned and the masks pre-cut so they may be applied and removed without cutting on the model. One technique is to use your decals as templates for complex shapes and stripes. Scan the decal 1:1 onto regular paper. Lay strips of wide Tamiya masking tape on wax paper with a slight 4-5 mm overlap. I like the Tamiya tape because it is fiber-like and trims nicely, adheres and seals to the surface well, yet has relatively non-aggressive adhesive. Using a glue-stick, smoothly tack the scanned decal onto the tape and use a very sharp blade to trim exactly around the color portion of the decal. Now the tape under the decal can be removed from the wax paper and gently laid in place on the model, but do not rub it or burnish it. Next use the portions of tape "outside" the decal to surround the decal on the model, laying them right up to the edges and matching everything up. Carefully peel away the "decal" part and leave the tape that surrounds the image. Gently burnish the edges and shoot a light mist of clear acrylic to seal the edge. Now you can paint away, but be ready to work quickly when you put the airbrush down. While the paint is still wet, VERY carefully, and VERY SLOWLY peel away the tape. Use the technique whereby the tape is pulled away from the painted area at a steep angle to prevent any lifting or paint hairs getting on the surface. Make sure the tape is not pulled "up" but rather is kept close to the surface, and pulled slowly to avoid any stresses or lifting of the foil. An analogy is peeling a paper label from a prescription bottle. If you peel or pull too hard the label rips. Going agonizingly slow allows the glue on the label to stretch and separate without damaging the paper label. Here we do the same thing and allow the low-tack tape to release and not put stress on the foil to plastic bond. Don't forget to mist on a light coat of flat white or light gray primer before shooting very light colors on the foil.
Now your model is ready to accept decals, and the clear finish will help. Decals will go onto unprepared foil, but having the clear coat sealed surface ensures a uniform substrate upon which to work and protects the weathering materials from decal solutions. Trim the decals close since the small pieces outside the printed area are hard to hide on this type of surface. Be sure to use quality decals that are truly clear between letters and numbers since the Tamiya X-22 is crystal clear and any yellowed or off color decals will show up as a weird color patch around your lettering. When finished, give the entire model and decals another few thin coats of clear acrylic and let it cure. Now the fully sealed surface is ready for any washes you may want to apply. Using an oil based wash is handy since the acrylic coating resists the solvents allowing blending, gradual application, and correction of mistakes as you go.
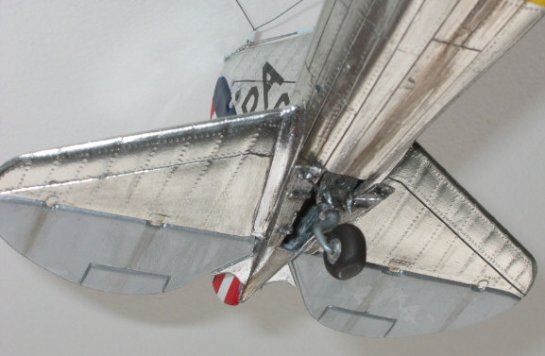
CONCLUSION
We are very fortunate to be model builders in this day and age when so much new technology and advanced materials are about. As kit manufacturers increase the fidelity of their reproductions we have the opportunity to build models to a level of quality not dreamed of before. The fun part is sometimes getting to think outside the box and develop our techniques and methods. Using metal foil as an adjunct to finishing materials allows us to make surface replications not feasible with paint alone. As modelers, developing the skills to work in various mixed media allows us to have a deeper, more complex bag of tricks to use in replicating the subjects of our choice. The suggestions put forth to you above are only a start, and will hopefully guide you to find more applications and increase your level of enjoyment in future modeling projects.
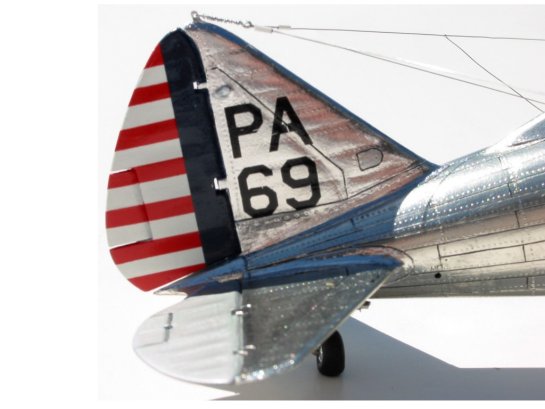
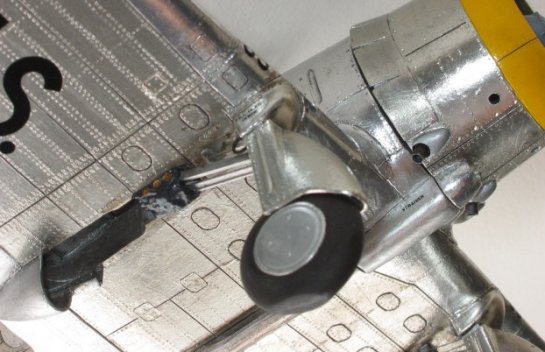
© Mike McLeod 2002
This article was published on Monday, November 02 2015; Last modified on Monday, November 02 2015